Another kind of curtain wall
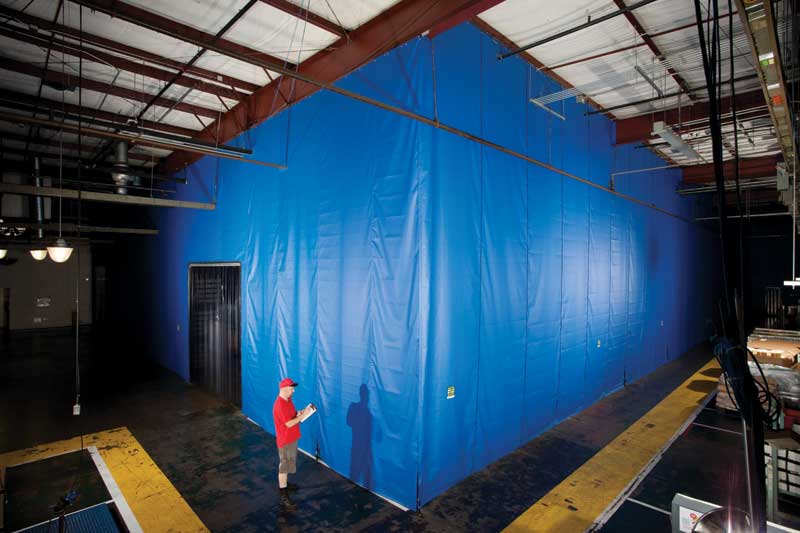
by Chuck Ashelin
The effects of machine or process noise in a commercial/industrial facility can range from an annoyance to a serious long-term safety issue for employees. The Occupational Safety and Health Administration (OSHA) estimates more than 30 million workers annually are exposed to hazardous sound levels in the United States.
The source of this exposure takes many forms:
- assembly and machine tool operation;
- process equipment (e.g. pumps, compressors, and blowers);
- material-handling equipment (e.g. conveyors and fork trucks); and
- power hand-tools (e.g. saws, grinders, and drills).
Reduction of excessive noise levels is important as an employee safety issue. The effects of human exposure to levels beyond 90 decibels (dB) are cumulative—that is, permanent hearing loss is related to accumulated time exposed to these high levels over a lifetime.
OSHA mandates employers to limit employee noise exposure to 90 dB or less on an eight-hour time-weighted average basis. In typical industrial environments, employers are obligated to monitor workplace sound levels to determine where they stand in relation to this threshold. If found to be above the 90-dB limit, they are required to take action to reduce employee exposure to levels below the limit. On such option would be the use of ‘curtain walls’—an assembly more literal than the glazed building enclosure many associate with this term.
Classic methods of addressing facility noise
Understanding the noise level in question is key to being able to affect the noise transmission. The lower the sound frequency (e.g. bass speakers from another car at a stoplight), the harder it is to mitigate. Mid-range and slightly higher frequencies are easier to manipulate. It is also important to know how the noise is being transmitted—is it being carried by vibration through a concrete floor (e.g. a stamping operation) or through the air from the inner working of machinery (e.g. gears grinding or compressors running)?
There are multiple ways to address noise control issues in an industrial environment, including redesign or replacement of the contributing equipment with new, quieter models. However, this approach may be unfeasible due to the cost or availability of quieter equipment. Noisy machines can sometimes be modified to reduce or eliminate noise-producing vibration—adding isolation pads or vibration dampeners are common approaches. Machines may also be encased in sound-absorbing enclosures or materials.
If these do not offer the desired result, or prove to be impractical to implement, noise-reduction barriers can be placed between offending equipment and the affected employees. This classically consists of rigid, insulated walls or partitions strategically placed to block the path of transmitted sound waves, and absorb and scatter them, reducing the total sound power level that actually reaches the employees.
The final defense against excessive noise involves personal hearing protection on individual employees, such as earplugs or ear muffs (either passive or noise-canceling). While effective protection, they have the shortcoming of only being useful while actually worn, and only when properly fitted. Additionally, in a facility where hearing protection is required, regular hearing testing of affected employees is mandated by OSHA.
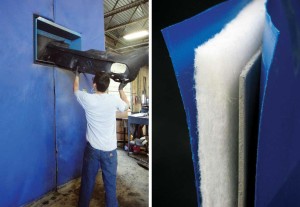
Flexible acoustic curtain walls
Flexible, acoustic ‘curtain walls’ represent a new approach to sound control. Sound-insulating industrial fabric curtains normally consist of two layers of a woven, coated material surrounding one or more layers of various insulating materials. These might include:
- fiber batting (polymer or glass);
- open-cell blown polyurethane foam sheets;
- densified ‘loaded’ vinyl; or
- another flexible polymer sheet material.
Each one plays its own important role in reducing sound levels impinging on the curtain surface. For example, the mass-loaded vinyl sheet in a sound curtain is more effective in lowering frequency noise than the other components (low-frequency sound is best absorbed or deflected with high-density solid materials). Fiber batting is effective in decreasing sound at mid- to higher-range frequencies. Open-cell foam (e.g. a viscoelastic) also offers noise reduction over a range of frequencies, but care must be taken to ensure the foam used is effectively treated for flame retardant.