Caring for glazed architectural terra cotta
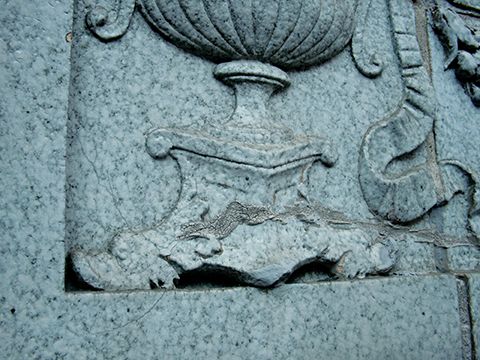
Moisture infiltration
Water penetrating between the clay bisque and finish glaze tends to migrate through the porous clay, leading to the disintegration of the terra cotta. One source of water entry might be delamination of the finish glaze, which can occur when the thermal coefficient of expansion between the clay and the glaze do not match. Alternatively, the original design may have supposed exaggerated waterproofing properties of the finish glaze, and systems for water management, such as flashings, weep holes, and drip edges, were never incorporated.
Cyclic wetting/drying and freezing/thawing can lead to glaze deterioration, cracks and spalls in the body of the terra cotta, and fracturing and displacement of the units. Crazing, the formation of small random cracks in the glaze, occurs when the terra cotta unit absorbs moisture from the air and expands over many years. When new terra cotta is removed from the kiln, firing has shrunk it to its smallest size. Over time, the porous clay grows, and the glaze goes into tension. Once the glaze strength has been exceeded, it cracks and shatters, increasing the water absorption of the terra cotta unit and exacerbating water infiltration in a self-perpetuating cycle.
When water enters the wall system through poor detailing, insufficient maintenance, rising damp, or a leaking roof, the impervious glaze may impede moisture migration and trap water inside the terra cotta unit. As temperature fluctuations increase pressure, glazing sections or the terra cotta itself may break off or spall. Glaze spalling tends to begin as blistering, when trapped water migrates to the surface and builds up pressure behind the glaze, eventually forcing pieces off the unit face. Glaze spalling may also be caused by corrosion of internal metal anchors.
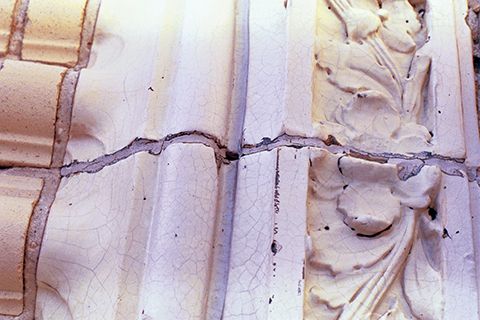
When the terra cotta itself breaks apart or spalls, the result is a loss of visual integrity. With the porous underbody and anchoring exposed to the elements, the potential for water entry and further destructive effects increases.
Corrosion of embedded steel
As water penetrates, it comes in contact with embedded steel anchors and reinforcement. In historic applications, steel was often untreated, making it particularly susceptible to corrosion. As it corrodes, the steel expands, exerting pressure on the surrounding terra cotta and causing cracking and displacement. Embedded steel corrosion may be caused by unmaintained roof drainage systems, which admit water into the cladding assembly.
Embedded steel corrosion can be challenging to treat because it tends to be difficult to diagnose unless it is severe. By the time symptoms are visible at the surface, corrosion is likely already advanced. Initial outward signs of metal anchoring deterioration might include staining and spalling. Total anchoring failure can result in loose terra cotta units, which are in danger of falling from the building.
Structural and thermal movement
Large cracks running through multiple units or stories usually indicate problems with embedded structural elements. Rehabilitation often requires removal of pieces to examine and treat defects, such as corroded steel columns.
Most high-rise buildings from the early 1900s had little or no provisions for movement, so the unaccommodated thermal expansion and contraction—along with building-frame shortening under load—placed sufficient strain on building materials to cause displacement and cracking. Without proper expansion joints, buildings create their own, in the form of long cracks allowing significant water infiltration and inviting further problems.
Improper repairs
Many repairs prematurely fail because they do not address the root cause of distress or failure. Often, repair materials do not last and are incompatible with the existing terra cotta, creating a poor visual match and a short-term fix. Where repairs fail, they tend to make deterioration worse.
Poor detailing, including failure to properly anchor the patch to the backup, leads to failure of not only the repair area, but also the surrounding terra cotta. For example, replacement brick and cement stucco are neither watertight nor flexible enough to help accommodate movement, so they tend to pull free or crack and spall. Likewise, surface-applied sealants are not watertight, and bituminous patches are ineffective and aesthetically unsuited to terra cotta repair. In an effort to keep out water, non-breathable coatings are sometimes applied. These have the effect of trapping water inside the terra cotta, particularly if the source of water entry has not been addressed.
The misuse of sealant in place of mortar for joint repairs serves to trap water within the terra cotta, leading to corrosion of embedded steel and cracking and spalling of terra cotta. Unlike impervious sealants, mortar is porous and allows moisture to escape.
Alterations and additions to the building, such as signage, screens, marquees, and bird-proofing components, may also cause damage, where anchoring involves boring holes or cutting into the glazed terra cotta. When the appurtenances deteriorate or are removed, the holes remain, admitting water infiltration.