Caring for glazed architectural terra cotta
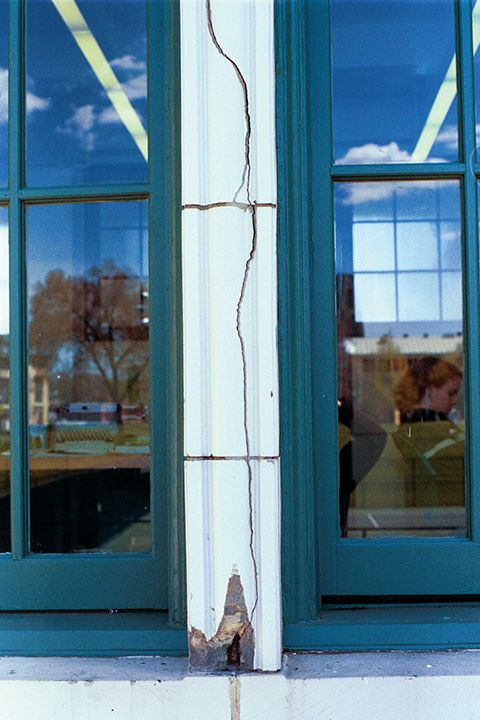
Investigating terra cotta conditions
Before a comprehensive investigation, it may be helpful to clean terra cotta, as dirt can conceal problems. A unit-by-unit visual inspection should be performed to note surface deterioration, including staining, crazing, cracking, and spalling. Where possible, a hands-on, close-up examination is best.
To identify hidden deterioration, each unit can be struck with a wooden mallet. To the experienced ear, an undamaged unit gives a pronounced ring, where deteriorated units produce a flat, hollow sound. While inexact, this tapping method provides a measure of the integrity of terra cotta without invasive testing.
Metal detection, by means of an oscilloscope, may be used to confirm the anchor locations indicated on original drawings. A negative reading where an anchor would be expected may indicate it is missing or deteriorated.
Together with visual inspection and non-invasive testing, laboratory analysis can provide a picture of the terra cotta’s conditions and composition, to develop an appropriate repair program. The evaluation might include glaze absorption, permeability, and adhesion, as well as terra cotta porosity.
Other non-destructive test methods include infrared scanning, which uses a thermal camera to measure heat, and ultrasonic testing, which emits sound waves and reads the patterns that bounce back. Both methods compare the readings of intact terra cotta with those of damaged units to identify concealed conditions.
Proper maintenance and repair
Before attempting to fix terra cotta damage, causes must be addressed. Eliminating sources of moisture infiltration is critical and may necessitate adding flashings to protect water entry surfaces. For structural problems (e.g. long, vertical cracks at building corners), an engineer may need to evaluate the integrity of the embedded structure before repairs to terra cotta units are made.
Glazed terra cotta was designed to be cleaned cheaply and easily. Typically, water, detergent, and a natural or nylon bristle brush for gentle scrubbing are all that is required. Strong acid solutions may deteriorate mortar, release salts in the terra cotta, and cause efflorescence, and are best avoided. While generally unnecessary, some proprietary commercial solutions may be suitable for use on terra cotta; one should check the manufacturers’ recommendations. Abrasive cleaning, such as sandblasting, high-pressure water, or metal bristle brushes must be avoided as they can damage glazing irreversibly.
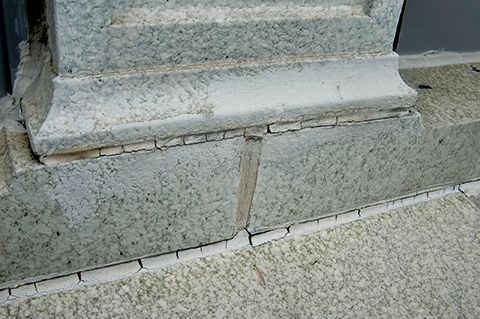
Although persistent water infiltration may make a waterproof coating seem like a good idea at the time, indiscriminate coating of the entire wall is generally inadvisable, as it may trap water and make matters worse. Although serious crazing may be treated on a limited scale, most glaze crazing does not substantially increase the water flow into the wall. Unless the source of moisture infiltration is addressed, applying an impervious coating only serves to prevent outward water migration from within the assembly.
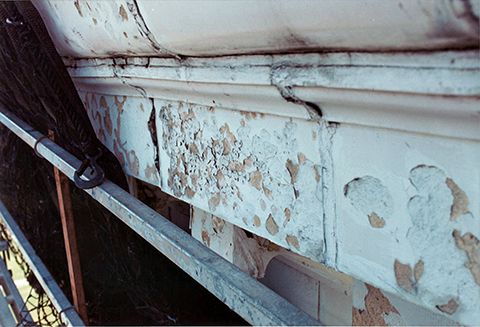
Maintaining mortar joints is very important to the lifespan of terra cotta. Periodic repointing prevents water entry and inhibits deterioration. It is important to use a mortar with a compressive strength lower than that of the adjacent terra cotta, since a hard mortar may prevent the outward migration of water and may cause point loading. One should never repoint with sealant, as this impedes moisture movement. Rather, sealant must be used
selectively, such as at joints in horizontal surfaces of copings and sills.
For spalled glazing, blistered areas should be coated or sealed to prevent water infiltration, using color-matched products. At lower stories where visual integrity is critical, the unit may need to be replaced. Patches tend to be aesthetically unappealing and do not bond well over the long term. Cementitious materials, especially, have a coefficient of expansion that differs from that of terra cotta. For major spalls, the only solution is to replace the unit. Partial repairs do not last, and may cause problems later.
As a stop-gap measure to prevent further water infiltration, structural cracks in units not slated for replacement may be sealed with a waterproof material that accommodates movement. For static cracks, butyl sealants or acrylic latex caulk may be recommended, while dynamic cracks are better sealed with polysulfide caulks or other proprietary products. It is important to ensure these compounds are not used for repointing; only mortar should be employed in mortar joints.
Where the existing steel has corroded, it should be treated, repaired, or replaced, as appropriate. For new anchors, protected stainless steel should be used in order to prevent future corrosion.
Deteriorated, unstable, or visually incompatible previous repairs, including cementitious stucco, bituminous compounds, and brick infill, should be removed and replaced with appropriate, properly detailed repairs. Rehabilitation should address the root cause of distress, using materials that are compatible with the existing terra cotta, and which do not compromise the assemblies breathability and moisture balance. Additionally, maintaining materials adjoining the terra cotta, including flashing, capping, roofing, and sealant at doors and windows, is vital to averting deterioration.