Caring for glazed architectural terra cotta
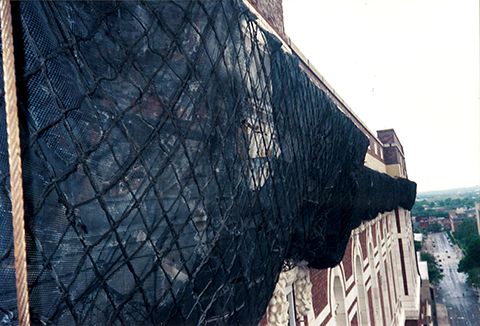
Precast concrete
This material is cost-effective, offers rapid production times, and can usually replicate original detailing. When cast hollow with lightweight aggregate, its weight is comparable to terra cotta, and it typically produces good results in color matching. For visual compatibility and waterproofing, a clear masonry coating should be applied to the weather face. On the downside, precast concrete may not be as long-lasting as terra cotta.
GFRC
Glass-fiber-reinforced-concrete (GFRC) is a precast product composed of a portland cement-based composite with alkali-resistant glass fibers randomly dispersed throughout to add flexural, tensile, and impact strength. Strong and lightweight, GFRC may be formed into complex shapes and offers a range of colors, textures, and surface finishes.
While similar to terra cotta in terms of weight and wall thickness, GFRC typically has no structural capacity. Some varieties incorporate different glass content and admixtures to gain some structural strength. The material is perhaps most appealing for its substantial cost savings over terra cotta, typically upward of 50 percent. However, it may be difficult to match the finish of existing terra cotta.
GFRP or fiberglass
Glass-fiber-reinforced plastic (GFRP) or fiberglass can be cast from intact pieces of original terra cotta and has limited use as a replacement material for elements with fine detail, provided the size and scale are not too large. Originating in the boat-building industry, GFRP is lighter than terra cotta and may be a viable option for buildings in areas of high seismic activity, or where existing structural supports proved inadequate. Surface gelcoats offer a wide range of colors and patterns; however, ultraviolet light degradation, and fire resistance are considerations.
Several blends of resin, gelcoat, and glass fibers may need to be tested to obtain the requisite strength and finish properties.

Alternative materials
Micro-cotta, a polymer-based composite concrete, is a proprietary product developed for terra cotta rehabilitation. Lightweight and capable of reproducing detail with sharp definition, it uses a finer aggregate than cement-based concrete and has a lower absorption rate. However, there is some evidence early formulations tended to fade and yellow in sunlight, and may have been susceptible to excessive crazing.
Toward a durable solution
Many architecturally significant buildings from the late 19th and early 20th centuries in the United States incorporate terra cotta façade elements. As these buildings age, they demand ongoing care and maintenance. Restoration of glazed architectural terra cotta should employ the same level of care and attention that went into its original design, fabrication, and installation.
When cared for diligently, terra cotta is a resilient and relatively low-maintenance material. By repairing minor cracks, spalls, and other signs of deterioration promptly, building owners and managers can break the cycle of deterioration before damage becomes severe and irreversible. When coordinated among owner, design professional, fabricator, and contractor, terra cotta rehabilitation can revitalize the distinctive façades of historic terra cotta structures, while providing durable repair solutions that stand the test of time.
WORKING WITH LANDMARKS AGENCIES |
For state or local landmarks or buildings listed as part of a historic district, it may be necessary to submit a permit application prior to undertaking terra cotta restoration. Permits are not typically required for routine maintenance, such as caulking or removing graffiti. For most restoration work, including repairs, repointing, resurfacing, replacement, and cleaning, a permit is usually compulsory. Landmarks agencies typically require documentation the restoration program is based on evidence of original conditions and will not alter the historic fabric. For terra cotta replacement, the design professional may need to document deterioration and show the proposed methods and materials replicate the original texture, color, dimensions, and details, and that they are consistent with accepted preservation practice. Substitute materials are typically approved only for limited areas. For specific guidelines, one should refer to the local landmarks authority or historic preservation commission. |
Arthur L. Sanders, AIA, is senior vice president and director of architecture at Hoffmann Architects, an architecture and engineering firm specializing in the rehabilitation of building exteriors. He has more than 30 years of experience in the restoration of historic façade systems. Sanders can be reached at a.sanders@hoffarch.com.
Kara L. Shypula, Assoc. AIA, is the project coordinator at Hoffmann Architects in New York City, where she provides investigation, document preparation, and construction administration services for building envelope projects. She can be reached at k.shypula@hoffarch.com.