Specifying corrosion inhibiting admixtures for concrete structures
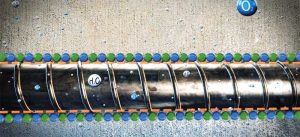
Where is corrosion a concern?
Since different environments are more corrosive than others, an engineer should take a structure’s location and intended purpose into account when specifying materials for the project. Regions that use a high volume of deicing salts in the winter are especially notorious for corrosion problems on reinforced concrete parking ramps. Bridges and seawalls in seaside environments are also under greater attack—sometimes from humid, salt-laden air, and other times by direct immersion in saltwater. Elevated temperatures also play a role, often accelerating corrosion in tropical or subtropical climates. In places such as the Middle East, high mineral sabkha soil and/or high-water tables (possibly with saltwater) add another dimension of corrosiveness. Functional factors can also play into the equation, as when concrete elements are built to handle seawater or brine at desalination plants, creating an obvious risk for an early corrosion attack.
Why use corrosion inhibiting admixtures?
There are many strategies to mitigate corrosion. These include using a lower water to cement ratioto decrease permeability, increasing concrete cover, using galvanized or epoxy-coated rebar or an alternative type of reinforcement, adding cathodic protection, and others. Many of these approaches have their tradeoffs—most often economically. For example, using epoxy-coated rebar, swapping black steel rebars with stainless steel, installing sacrificial anodes, or connecting to a power source for impressed current cathodic protection (ICCP) can add significant cost to the project price tag.
Corrosion inhibiting admixtures are typicallya more cost-effective approach for tight budgets. Similar to other admixtures, they are liquid or powder additive formulations that are mixed into the concrete batch at the ready-mix plant or onsite. When properly mixed, they are dispersed throughout the concrete batch, allowing them to either delay the onset of corrosion, slow down active corrosion rates, or both. Admixtures often constitute a very small percentage of the total building cost while significantly adding to service life predictions.
Economic issues aside, investing extra money in “more durable” materials is not failsafe: cracks can still occur in a thick concrete cover, leading to chloride ingress, and epoxy-coated rebar can corrode where the coating has chipped off. On the other hand, if funds are not lacking and maximum durability is required, corrosion inhibitors can add another level of protection when used in conjunction with one of these other corrosion inhibiting strategies.
What can qualify as a corrosion inhibiting admixture?
When it comes to industry standards, engineers often look to guidelines from the American Concrete Institute (ACI) for direction. While these guidelines do not give the final answer, they do compile information and opinions from experts in their fields. The “ACI PRC-222-19: Guide to Protection of Metals in Concrete Against Corrosion”2 outlines a variety of industry-accepted best practices for inhibiting corrosion. The “ACI 212.3R-16: Report on Chemical Admixtures for Concrete” focuses on concrete admixtures in general, with an entire chapter dedicated to admixtures that inhibit corrosion.3 These two guidelines define corrosion inhibiting admixtures as those that delay time to corrosion onset and/or reduce the corrosion rate. They refer to ASTM C1582, Standard Specification for Admixtures to Inhibit Chloride-Induced Corrosion of Reinforcing Steel in Concrete,4 which requires a corrosion inhibitor to reduce the rate and amount of corrosion, compared to a control. The ACI standards also imply that simply reducing chloride intrusion is not enough for a product to qualify as a corrosion inhibiting admixture.