Concrete tips: why effective curing practices are important
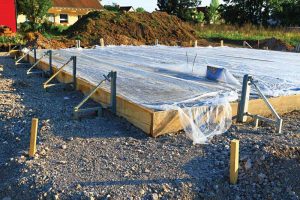
Methods of curing
ACI 308 discusses a few general systems for maintaining adequate moisture content for freshly placed concrete to achieve the desired design properties:
- Continuous or frequent application of water through ponding, fogging, steam, or saturated cover materials, such as burlap or cotton mats, rugs, sand, and straw or hay. None of these are recommended for slabs to receive a moisture-sensitive covering.
- Minimization of water loss from the concrete by use of plastic sheets or other moisture-retaining materials placed over the exposed surface for three to seven days after concrete placement. This is highly impractical on most jobsites, especially with elevated slabs.
- Application of a membrane-forming compound (commonly referred to as a curing compound) meeting the requirements of ASTM C309 or ASTM C1315.
For concrete slabs to receive moisture-sensitive flooring, adhered roofing, or coatings, most of the above methods are impractical, unfeasible, costly, or time consuming. Further, the duration of curing required to achieve the desired levels
of strength, durability, or both, depends on a complex set of factors, making it difficult to confidently state the minimum curing time. Since most curing methods cannot be used with slabs given the cost, unknown duration, wind, disruption to other trades, or overall project timelines, among other factors, concrete slabs are most often cured with curing compounds.
Curing compounds
There are substantial misconceptions surrounding curing compounds as well. Namely, many believe they are all the same. This misconception has led design and project teams to not specify or use these products. The truth of curing compounds, however, remains; they are not the same.
On a broader scale, curing compounds can be separated into two major classifications: one for only curing freshly placed concrete, and the other is formulated to cure and seal it. To aid in better understanding these products, there are two ASTM standards for each classification:
- ASTM C309-19, Standard Specification for Liquid Membrane-Forming Compounds for Curing Concrete
- ASTM C1315-19, Standard Specification for Liquid Membrane-Forming Compounds Having Special Properties for Curing and Sealing Concrete
Although they share similar traits and properties, one can easily misinterpret the products to be relatively equal from their descriptions. For example, both ASTM C309 and ASTM C1315 describe “liquid membrane-forming curing compounds” to not negatively react with the concrete surface, and both have water loss properties and drying time listed as requirements. However, ASTM C1315 products have a much more stringent water loss requirement than ASTM C309 products, and ASTM C1315 requires a pull-off test for adhesive applied over the cure-and-seal compound.
It is critical to understand the adhesion pull-off requirement of an ASTM C1315 product. The standard states, a cure-and-seal product must be independently tested for sufficient bond with a ceramic tile adhesive, but this does not cover every type of adhesive. When discussing specifying an ASTM C1315 product, it is noted, “there is an extremely wide range of adhesive types and formulations, and it’s inappropriate to extrapolate the performance of other adhesives from a test of only one.”12 This remains relevant to this day.