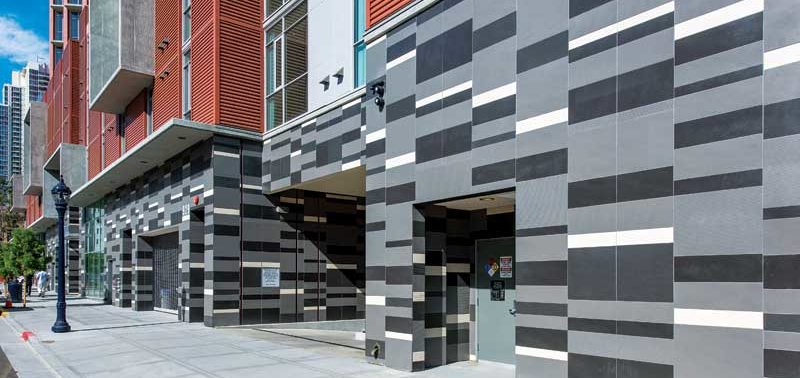
by Howard Jancy, CSI, CDT
A folk rhyme often attributed to Benjamin Franklin describes the unintended outcome of simply omitting a horseshoe nail—namely, the loss of a kingdom:
For the want of a nail the shoe was lost,
For the want of a shoe the horse was lost,
For the want of a horse the rider was lost,
For the want of a rider the kingdom was lost,
And all for the want of a horseshoe-nail.
This proverb illustrates a basic truth—quick and poorly thought-out decisions have consequences beyond the initial myopic moment. Though the rhyme is not modern in origin, its maligned nail is often the culprit in today’s construction failures. The ‘nail’ in this narrative, for example, is expansion and movement joints, and the unintended outcome is the failure of a building’s tiled exterior.
A project located in a Midwestern city provides an excellent example to illustrate this point. The complex consists of three residential buildings considered upscale apartments. The exteriors are clad with a brick veneer, 450 x 450-mm (18 x 18-in.) glazed porcelain tiles, and 600 x 600-mm (24 x 24-in.) unglazed, through-body porcelain tiles. The structures were completed in 2014. One year later, after exposure to a winter’s and summer’s temperature extremes, the larger porcelain tiles started to loosen and fall. Technical data for these light brown tiles indicated the tile was applicable for commercial and outdoor use, and was freeze-thaw-, thermal-shock-, and frost-resistant. Thermal cycling seemed to be the catalyst for the failures, yet the question remained—why? Why would construction materials and methods that were used successfully in the past suddenly exhibit such extensive failures?
The search for the proverbial nail begins.
A closer look
Tile failure was clearly evident on each building, occurring randomly. Though there was a clear indication that the failed tiles were not properly bonded during installation, this did not illuminate the initiating factor that pulled the tiles from the structure. A closer inspection of the tile installation revealed extensive cracking and debonding of the cement grout.
On further investigation, it became clear that no movement joints had been installed to accommodate expansion and contraction of the tile during freeze-thaw cycling in winter or thermal expansion during the summer. As the tiles expanded and contracted, correctly located and installed silicone soft joints in the assembly would have absorbed their movement without adhesive or cohesive failure, but not so with rigid cement grout. Once the grout cracked, moisture readily traveled behind the tiles, further deteriorating the already-tenuous adhesive bond between tile and mortar (Figure 1).
The Tile Council of North America (TCNA) Handbook for Ceramic, Glass, and Stone Tile Installation contains general recommendations for the use and installation of movement joints. Its section EJ171, “Movement Joint Guidelines for Ceramic, Glass, and Stone,” provides 12 details illustrating the correct design and placement of various types of movement joints. It states:
Because of the limitless conditions and structural systems on which tile can be installed, the architect or designer shall show the specific locations and details of movement joints on project drawings. Preparation of openings left by the tile contractor and installation of backup strip and sealant should be specified in the Caulking and Sealant section of the job specification.
More specifically:
- any joint through the tilework placed directly over a structural joint must never be narrower than the structural joint;
- movement joints should be located every 2.5 to 3.7 m (8 to 12 ft) in every direction for exterior installations;
- a movement joint filled with a silicone sealant material meeting ASTM C920, Standard Specification for Elastomeric Joint Sealants, must be three to four times wider than the anticipated movement, allowing for proper elongation and compression of the sealant; and
- joint width for an all-tile exterior must be at least 10 mm (3⁄8 in.) for joints 2.4 m (8 ft) on center and 13 mm (1⁄2 in.) for joints 3.7 m (12 ft) on center, and these minimum widths must be increased by 2 mm (1⁄16 in.) for each 9 C (15 F) tile surface temperature change greater than 38 C (100 F) between summer high and winter low.
On some portions of the tile project, the grout was not even installed, readily allowing moisture behind the tiles. The extent of water intrusion behind the tiles can be clearly mapped by the darker, damp areas on the tiles’ surface (Figure 2).
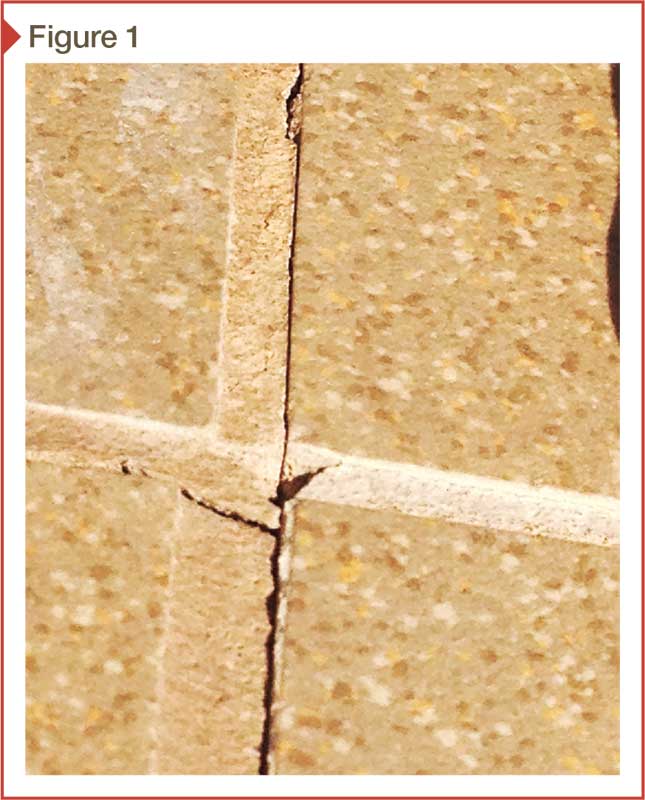
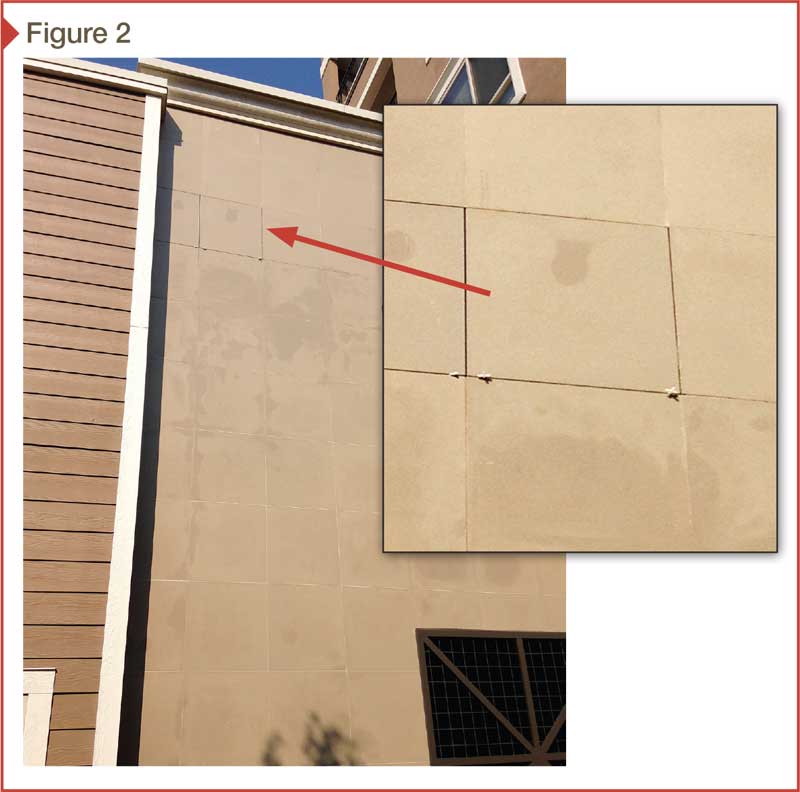