New purposes for cold-formed steel
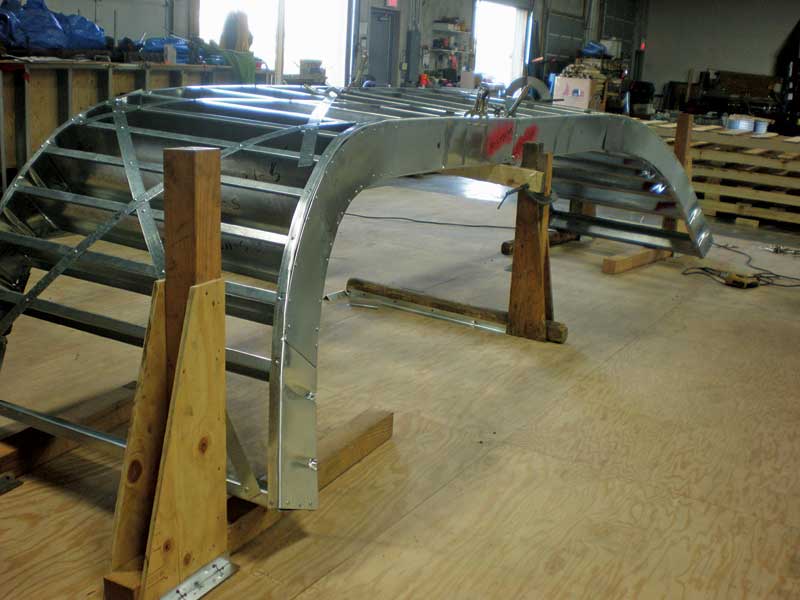
Hard Rock Café.
Panelized arches create intimacy at Hard Rock Café
Creating a sense of intimacy in bars and restaurants can be challenging, especially when working with large, cavernous spaces. For Tampa, Florida’s Hard Rock Café (pictured on the cover), the architects were looking for a distinctive new image for the project. The retrofit of a former nightclub called for a grand gesture—a series of five back-to-back arches made up of complex, compound curves. Together, the five arches comprise a dramatic interior canopy for patrons of the bar and restaurant—at its largest it is 5.8 m (19 ft) high, 15 m (49 ft) wide, and 12.5 m (41 ft) long. To create the canopy effect, each arch is a different shape and size.
Unlike a typical arch construction beginning at the base, this project was done in reverse. The unitized panels were hung starting with the center ‘keystone’ and built working toward the ground on each side of the arch. As the materials were manufactured offsite in Minneapolis, Minnesota, panel assembly and installation had to be extremely precise given the large size and complex geometry. Each section had to be fabricated to fit with the next, and the placement of each arch in relation to the adjacent arch had to be carefully managed. The design team used 3-D models, installation drawings, and a custom color-coding system to simplify the process. Construction crews on the ground were able to schedule and take delivery of the panels when they were needed, enabling the other interior retrofit work to continue on schedule.
Unitized panels help bring sunlight into transit center
Unitized panels were used in a completely different way to construct a giant oculus in New York City, which sits atop the Fulton Street Transit Center in lower Manhattan. As the new transit and retail hub’s most striking design feature, the daylight-delivering circular opening brings natural light deep into the building through a glass-enclosed central atrium.
Grimshaw Architects, with Arup, designed the Fulton Center building to solve the safety and aesthetic concerns that marred the old space. The changes include the replacement of the poorly marked Fulton Street subway entrance with well-lit, highly visible access points as well as a pedestrian concourse.
According to the project manager at New York’s Donaldson Interiors, the core and shell contractor at the job, the original plan was to stick-build the oculus. However, building the oculus wall onsite would have required workers to complete the construction of the complex, sloping walls while working five stories above ground. Additionally, due to its location near the water, the area is prone to severe storms—Hurricane Irene hit during construction. On top of less than ideal working conditions, the oculus had to meet rigid standards for construction site and public safety due to its proximity to the September 11 memorial sites.
The tight urban construction site operated adjacent to a major transportation hub serving more than 250,000 passengers daily. A limited number of general outages or disturbances to subway traffic were granted and assigned to times when no trains were running, allowing work on or near the subway tracks to be performed.
Additionally, onsite contractors were required to maintain safe passage for subway riders from one line to another, which meant the construction of temporary staircases. At street level, construction crews scheduled and sequenced activities without causing lane restrictions and minimal noise or exhaust discharge.
Re-routing and maintaining under-street utilities serving residential and commercial facilities adjacent to the site presented another set of regulations. At the time, demolition involved hazardous materials and contractors to follow Occupational Safety and Health Administration (OSHA) guidelines for abatement. To side step some of these complications, the team developed an alternate construction method.
Pre-fabricated panels assembled offsite were used for constructing the oculus. However, this also presented a significant challenge. The conical oculus measures almost 18.3 m (60 ft) tall at its highest point and spans 27.4 m (90 ft) across at its base diameter, covering a total surface area of 770 m2 (8294 sf). The job required 44 panels, each measuring about 2.4 by 5.8 m (8 by 19 ft), which were installed in two tiers. Each panel contained seven layers of protective material, and was sheathed in stainless steel cladding. When delivered to the jobsite, the panels fit together seamlessly, thanks to the use of 3-D computer modeling, accurate and economical detailing, and specific attention to connections. The specified unitized panels saved time and labor costs. The installation only took two-and-a-half weeks and averaged seven panels per day.
A final challenge was the creation of a parapet at the top of the oculus, which required the creation of a crisp finished circular tapered edge. A proprietary knife-edge panel solution, perfected on a previous collaboration at Frank Gehry’s New World Symphony project in Miami, was used to create the exacting detail required.
Twisted metal: Curved hat channel inspires
Hat channels are not new, but pre-curved hat channels are proving to be a lower cost solution for various projects. CFS hat channels are easy to install because the hat’s ‘brim’ provides a flat surface for fastening. For more complex projects, pre-curved hat channels can be an economical option to stud framing and other methods, such as cold rolled channel.