Specifying EQ coatings for steel studs
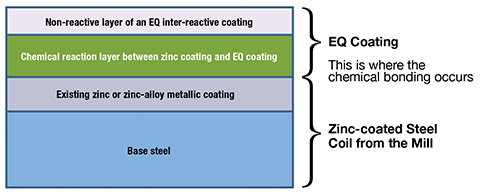
The minimum protective coating requirement of ASTM C645 is G40. In order to explain the meaning of this coating designation, the letter ‘G’ indicates the coating is galvanized or zinc-based and the ‘40’ refers to the total weight of zinc on the surfaces of the steel sheet in grams per square meter or ounces per square foot. Using G40 as an example, the coating weight on 1m2 (10.7 sf) of the steel sheet shall have a triple-spot test (TST) average minimum of 120 g/m2 (0.40 oz/sf). If the coating is equally applied to both sides of the sheet, there would be a minimum of 60 g/m2 (0.20 oz/sf). The TST measures the coating weight of three sample test coupons obtained from the centerline of the galvanized steel sheet and from the edge of each sheet. The three individual results are then averaged to generate the TST minimum.
For nonstructural steel studs, however, ASTM requires only a single-spot test (SST) as these studs are produced from steel sheets less than 457 mm (18 in.) wide. Thus, the SST is the proper test criteria for steel sheets with a width of 457 mm or less. The SST designations specify the minimum allowable coating mass for any galvanized steel sheet. When the SST is used, the minimum for G40 is a total coating weight of 90 g/m2 (0.30 oz/sf).
EQ meets performance requirements
Cold-formed nonstructural members utilizing EQ coatings have been proven by salt-spray tests to perform better than the minimum G40 permitted for use by ASTM C645. For instance, the typical G40 metallic coated substrate that meets ASTM A653 standard for galvanized sheet steel, are assumed to have a 120 g/m2 (0.40 oz/sf) total coating weight for both sides of the sheet. In closer review of the tolerances allowed by ASTM, the actual coating weight can be as low as 36 g/m2 (0.12 oz/sf) on a single side. The galvanizing process can also create a surface with valleys, fractures, pits, and porosity in the zinc metallic surface.
In this example, the surface of hot-dipped steel looks smooth to the naked eye. When magnified, the imperfections in the form of cracks and voids become obvious. EQ coatings fill in these cracks and voids, providing combined coating that is superior to the minimum G40 performance requirement.
Results from numerous salt spray tests, from multiple laboratories, reveal EQ coatings exceed the performance level of a standard G40-coated steel. During the tests, G40 steel samples with an additional chemical treatment protective coating began failing at 120 hours of exposure to salt spray and rapidly reached the 10 percent surface rust failure threshold at 192 hours on average. By comparison, EQ-coated samples did not climb above five percent surface rust, even after 240 hours of exposure. Further, each test was run beyond the 10 percent surface rust failure point of G40 steel. In thousands of tests, the EQ-coated samples did not reach failure, even after hundreds of hours of salt spray exposure. Testing was conducted in accordance with the ASTM B117, Standard Practice for Operating Salt Spray (Fog) Apparatus, standard and was performed at the laboratories accredited by the International Accreditation Services (IAS) a subsidiary of the International Code Council (ICC).
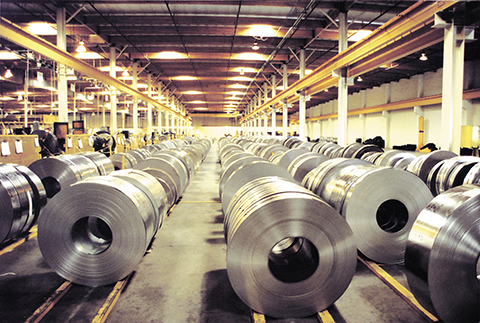