Closing the loop: Understanding the benefits of fluid coolers
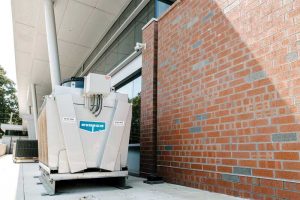
Case study: New School
When DLR Group, an integrated design and engineering firm with offices across the U.S., was hired to provide HVAC system design for a new school in Nebraska, its mechanical engineering department looked to a hybrid fluid cooler for heat rejection.
One of the main reasons the use of a fluid cooler was suggested over a traditional cooling tower is because eastern Nebraska has true shoulder seasons. In a climate like this, a heat sink that can operate wet or dry has a real advantage during part-load situations, or when the wet bulb temperature is lower. A heat sink dramatically conserves water and reduces sewer expenses.
A two-cell series fluid cooler was installed for the 14,400 m2 (155,000 sf) building. It is set up to provide 281 tonnes (310 tons) of cooling capacity in wet mode, but is capable of 317 tonnes (350 tons), allowing for some future capacity.
The fluid cooler at the new school maintains operation in dry cooling mode for as long as possible, providing sensible cooling to the process fluid within the coil. When the temperature set point can no longer be met during dry operation, the fluid cooler recirculating spray pump is energized, and evaporative cooling is activated. The fluid cooler has the capability of running completely dry while providing 100 percent capacity of the design load with an outdoor dry bulb air temperature of 7.05 C (44.7 F).
By eliminating the need for an open loop cooling tower and its associated components, it offers a substantial maintenance advantage as there is only one piece of equipment to maintain, instead of several.
In this case, first cost was not overlooked either. The total cost for the installed system for cooling towers and fluid coolers of similar capacity are comparable. The systems at the school have performed admirably, occupant comfort is high,
and the school sees desirable operating efficiencies.
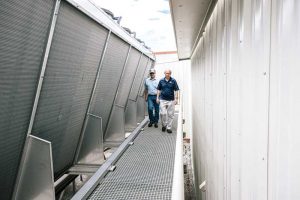
Operation schedule and state regulations
Adiabatic coolers function similarly to dry cooling systems, but with the addition of pre-cooling pads. Water runs over porous media while air is drawn through the pads, lowering the dry bulb temperature of the incoming air; this provides greater heat rejection. Adiabatic units also deliver the required cooling capacity in a smaller footprint and/or lower fan motor horsepower than a completely dry cooler.
If cooling capacity is needed during the winter, closed-circuit coolers are used. If there is no need for cooling capacity in the winter, open cooling towers and a heat exchanger are used.
This simple criterion is the leading consideration in many engineering firm’s decision-making process when deciding between a fluid cooler or cooling tower. Running a hybrid fluid cooler in dry mode (no water flowing) offers the ability to reject heat in the winter, while minimizing or eliminating the risk of ice formation in and around the unit.