Closing the loop: Understanding the benefits of fluid coolers
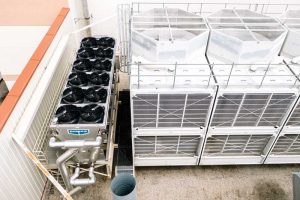
Aside from selecting the appropriate cooler style, there is a crucial design parameter called “the dry bulb switchover temperature” which must be specified to ensure the cooler can run 100 percent dry during colder months. The cooler will run in dry mode when the ambient temperature outside drops below the dry bulb switchover point for that specific cooler.
Two things impacting the dry bulb switchover temperature are surface area of the heat transfer coil and airflow. This results in the end user operating a fluid cooler that does not consume water in the winter, and therefore eliminates the risk of icing.
Dry and adiabatic fluid coolers are becoming more attractive to end users as they can save time and money by not having to register the unit, or test the recirculating water for Legionella, as they would for an evaporative unit such as an open cooling tower or fluid cooler.
Case study: Utah State University
As the name implies, dry coolers avoid the use of water altogether. In a dry cooler, heat from the process loop fluid dissipates through the coil tube surface and comes out to the fins—not through evaporation. Ambient air is drawn across the coil surface by a fan located at the top of the unit. Heat from the process fluid transfers to the air via sensible cooling and discharges to the atmosphere. Dry coolers are best specified where water conservation, reduced maintenance, and eliminating the risk of freezing are the key considerations.
Utah State University’s (USU’s) main campus is perched 1,371 m (4,500 ft) above sea level and is subject to very harsh winter conditions.
The campus district cooling system is served by an open-loop cooling tower capable of 5,443 tonnes (6,000 tons). During winter, when ambient temperatures can fall as low as -34 C (-30 F), the campus cooling load drops more than 90 percent. For roughly half the year, only server rooms and a constant temperature room in the library call for cooling capacity.
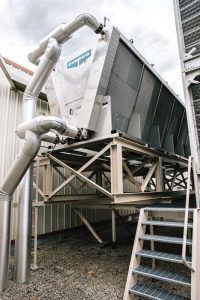
During this time, the cooling towers at USU would freeze solid, building up so much weight that the unit sustained damage. After a decade of this, several of the cells required complete fill media replacement at a tremendous expense, despite efforts to combat the issue.
Ultimately, the decision was made to select a configuration dry cooler. The unit’s competitive price, the availability of stainless-steel construction, correct physical dimensions, and the provision of maximum cooling capacity made it the winning combination.