Best practices for architectural coatings
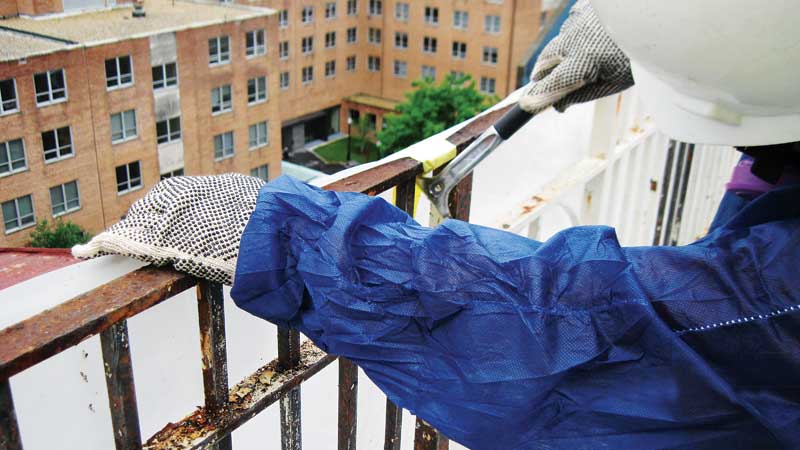
Coating selection
The substrate material and condition determines the coating application type, as well as what surface preparation is deemed necessary for ensuring durability and long-term performance.
Of primary consideration when selecting a coating is whether it is designed for interior or exterior use. For example, the coating requirements for interior window frame and sash components are likely to be different from the coating requirements for exterior exposures. For interior applications, VOCs and odor will be the principal environmental considerations in coating selection.
For exterior applications, considerations include weather conditions, such as acid rain, wind-driven rain, ice, standing water, and freeze-thaw cycling. Some coatings can only be exposed to UV light for a limited time, as established by the manufacturer and driven by project warranty requirements. The manufacturer also typically stipulates application within specific ranges of temperature and humidity.
Cost may also be a consideration when selecting a coating. Higher-performance coating systems cost more, and the determining factor in choosing a product is often price rather than life expectancy. In calculating a coating’s true price tag, though, owners and managers would do well to consider not just installation and material cost alone, but also the life cycle cost. Since much of the expense of a painting or coating project is in labor, cutting costs by opting for a cheaper paint with a shorter lifespan may actually increase overall life cycle expenditures.
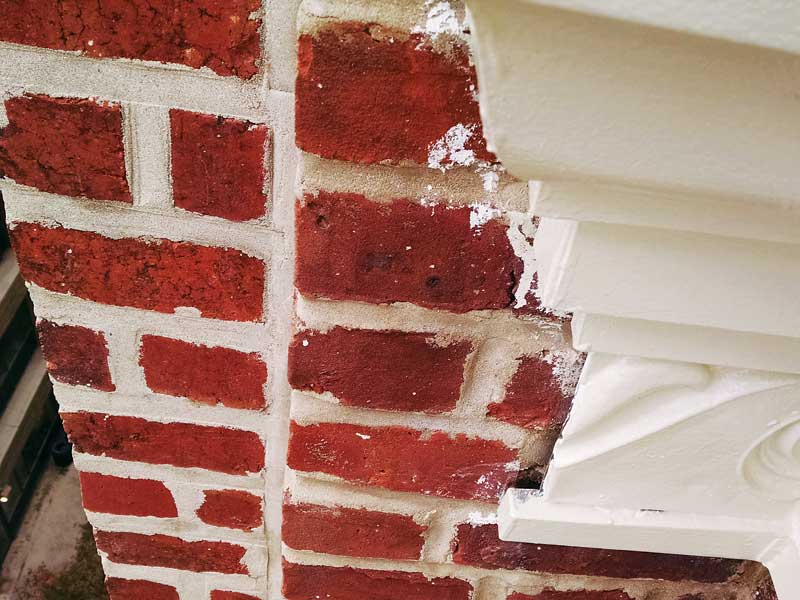
To avoid incompatibility between coats, it is usually advisable to select a complete coating system from a single manufacturer. If different brands of primers, paints, or finishing coats are combined, the design professional should evaluate the proposed system with the manufacturers to confirm compatibility and to verify the combination will not adversely affect the warranty.
Water-repellent and waterproof coatings
Intended to prevent liquid water from penetrating the surface while allowing water vapor to escape to the exterior, water-repellent coatings are transparent and intended to be invisible, although they may darken the substrate or impart a sheen/gloss. In contrast, waterproof coatings create a barrier impermeable to both liquid water and water vapor. Often opaque, waterproof coatings include bituminous, cementitious, and some elastomeric products.
Early water-repellent coatings were typically acrylic or silicone resins in organic solvents, which worked by forming a film on the surface of the building material. Newer water-based coatings are composed of modified siloxanes, silanes, alkoysilanes, or metallic stearates—these water-repellents penetrate into wood, concrete, or masonry, and are almost imperceptible if properly applied. However, some formulations may cause undesirable shine or darkening of the substrate. A mockup of the coating application is highly recommended in order to confirm the coated material’s appearance is acceptable.
Considerations for water-repellent coatings include substrates subject to frequent wetting, which have experienced severe or pervasive damage as a consequence. Water repellents greatly reduce the amount of moisture that comes in contact with a coated substrate, but their application is an irreversible treatment. Once a substrate is coated, it is impossible to return to an uncoated state—even if the coating fails.
Since coatings typically require periodic reapplication, a water-repellent coating creates an ongoing maintenance need for the life of the building. Compared with the expense of patch repairs or material replacement, coating to protect a fragile or high-exposure substrate can sometimes be a cost-effective repair.
Water-repellent coatings should be applied to clean and dry surfaces. If applied to already deteriorated surfaces, these products may exacerbate the damage by trapping moisture, accelerating deterioration, and even pulling off the face of the building element should the coating fail. Water-repellent coatings are not consolidants, so they cannot be used to strengthen deteriorating brick, concrete, or stone. If the façade is kept in good repair, water-repellent coatings are usually not necessary or recommended.