Best practices for architectural coatings
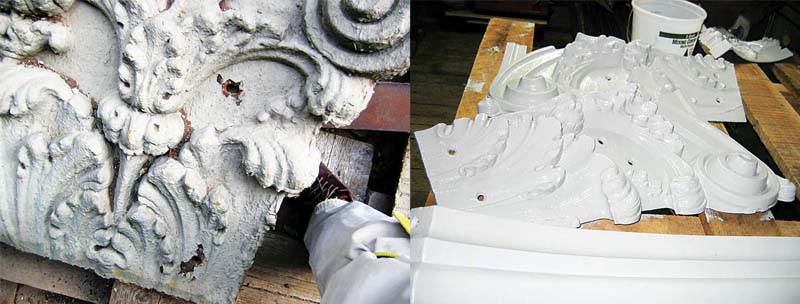
In some cases, water-repellents may be considered in selected areas or for specific substrates. The design professional should first evaluate the envelope’s watertightness and determine whether, despite proper rehabilitation measures, moisture is penetrating through exterior wall components. If water-repellent treatment is determined to be appropriate, it is best to treat only isolated problem materials or weaker areas, such as those exposed to weather extremes, rather than the entire building.
Unlike water-repellent coatings, waterproof coatings do not permit migration of water in any state—whether liquid or vapor—either into or out of the wall. If water enters the wall via a roof leak, through the building interior, or by means of capillary migration (rising damp) from the ground, it will be unable to escape if a waterproof coating has been applied. Trapped water can cause extensive damage, particularly if freeze-thaw cycling exceeds the tensile strength of the material and causes the substrate to break apart.
Waterproof coatings are often used in isolated cases for below-grade applications, but it is generally inadvisable to use them above ground for most types of buildings, particularly historic structures.
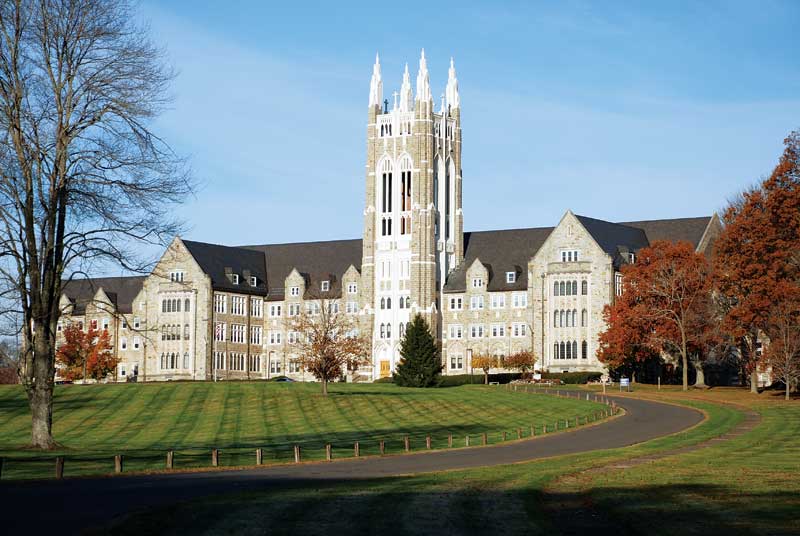
Anti-microbial coatings
Coating products that claim to prevent dirt accumulation or biological growth and so reduce maintenance demands may be effective, but in some cases a coated surface may actually attract more dirt or encourage more biological growth than an uncoated one. Routine cleaning with gentle methods appropriate to the building material can be just as effective, with the added benefit of avoiding the added maintenance and inadvertent ramifications that accompany coatings.
Getting the details right
Each participant in the design, production, and application of a coating has a role in determining the installation’s long-term success. Taking into consideration the type of substrate to receive the coating, the condition of building materials, environmental factors, product performance data, color and gloss, permeability, and other criteria, the design professional selects the coating and specifies any test methods, mockup standards, and application requirements that might be relevant.
The contractor is responsible for submittals to be reviewed by the architect for all products and installation details. The manufacturer, in turn, verifies that the proposed installation meets warranty requirements. Once drawings, specifications, and submittals have been approved, the design professional should conduct site visits in order to evaluate preparation and mockups, address unanticipated field conditions, and verify the application meets the design criteria.
Substrate preparation
The smoothness and soundness of the surface is critical to the long-term durability of a coating. Typically, materials with rough and irregular surfaces are not ideal for direct coating applications. Coatings are not designed to bridge gaps (e.g. bug holes, small fissures, or areas where mortar joints are no longer fully packed); while a coating may appear to cover a crack, once it dries, the crack may telegraph through.
Coatings differ in the degree of substrate unevenness they can tolerate in order to perform as designed. A coating cannot be expected to correct deficiencies such as an unstable or crumbling surface. Removal of unsound material is required. To create a smooth, sound surface for coating application, all friable debris should be removed and surface repairs made prior to applying the coating. This includes removal of existing coatings that would prevent adhesion of the new coating to the surface.
Addition of a parging coat (i.e. a thin layer of cementitious material) to an uneven surface can create a smooth outer layer suitable for receiving coatings. Depending on the composition of the parging coat, a minimum curing time will be required by the manufacturer before a coating may be applied on top. Design professionals and owners should note the curing time for different types of materials, and the effect on project schedule, can vary substantially. Cementitious compounds can take days to cure, whereas polymer-modified mortars can effectively cure and be ready to coat in hours.
Protection of the substrate may be necessary to provide adequate conditions for curing. To facilitate proper adhesion and prevent any water from becoming trapped behind the coating, the moisture content of the substrate must not exceed the maximum allowable level indicated by the coating manufacturer.
The Society for Protective Coatings (SSPC) has prepared standards for surface preparation tailored for metals and concrete, while the National Park Service offers guidelines for historic masonry. Other resources, including the Sealant, Waterproofing, and Restoration Institute (SWRI), Association for Preservation Technology (APT), and ASTM International, provide further information on surface preparation for coating application.