Caveat emptor
FAILURES
Deborah Slaton, David S. Patterson, AIA, and Kenneth M. Itle
Condition assessments are conducted to evaluate existing conditions, identify distress, determine appropriate repairs, and assist property owners in understanding possible future repair and maintenance costs. In this case, a pre-purchase inspection was conducted for a new owner in the process of buying a 1920s apartment building constructed with brick masonry loadbearing exterior walls and cast stone ornament. The scope of the inspection was limited to visual review of the building exterior from grade and rooftop access. The new owner understood the building was in need of rehabilitation to address deferred maintenance, and wanted to determine the likely scope of repairs.
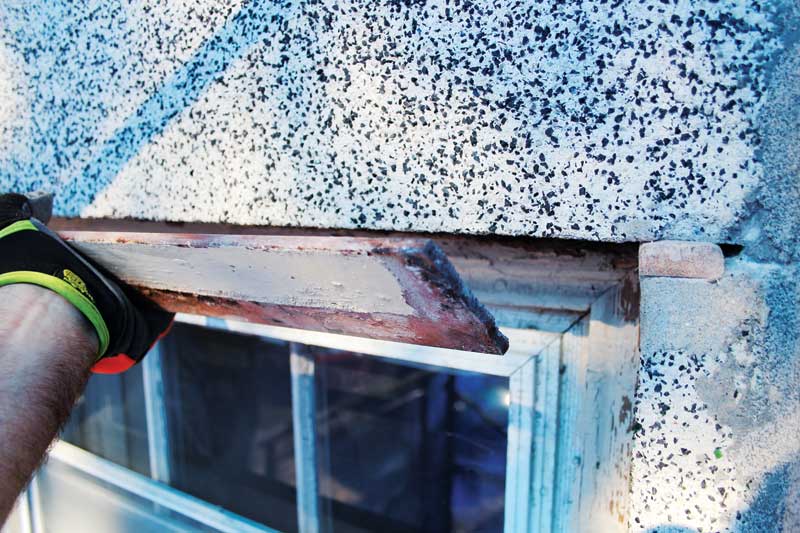
Photos courtesy WJE Associates
Based on experience with similar buildings, particular attention was paid to the steel lintels at window openings. As viewed from grade, the lintels appeared to have minor surface corrosion, but generally appeared to be intact; adjacent masonry did not exhibit noticeable distress. Some deterioration of cast stone and erosion of mortar joints was identified, so the scope for the facade repair program was determined to consist primarily of replacement of individual cast stone masonry units and joint repointing. At isolated locations where damaged cast stone units occurred above window openings, new flashing was to be installed to further protect the existing steel lintels. After the purchase was finalized, the new owner proceeded with the selective masonry repairs.
When repair construction began, the contractor immediately realized the apparent exposed portion of each window lintel was in fact not an intact steel angle, as anticipated. Instead, the exposed steel was revealed to be a narrow, non-original steel bar that had been placed into the bed joint above each window opening. The steel bars, apparently installed as a repair attempt in the past, concealed the original steel lintels, which remained in place, but were severely corroded with significant section loss. The steel bars did not provide sufficient structural support for the masonry above, and concealed the actual structural distress at the original lintels.
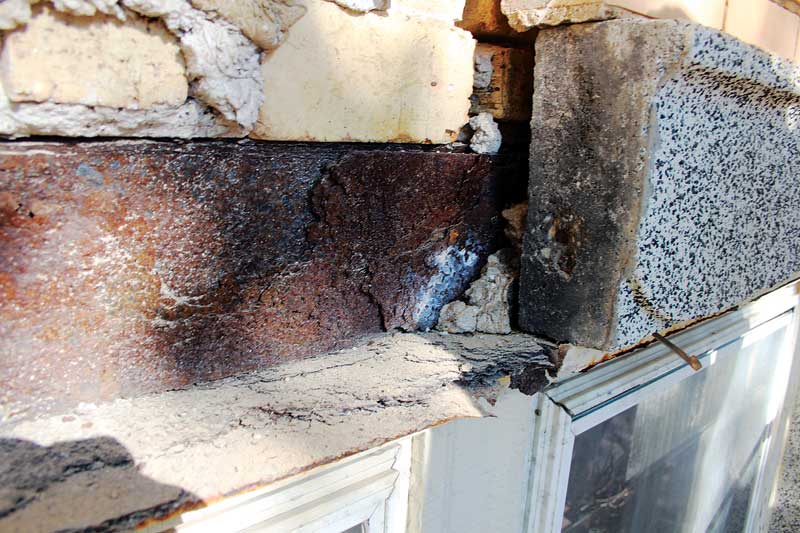
Thus, instead of localized repairs, the project scope expanded to include removal of the steel bars and full replacement of the lintels at all window locations. The new steel lintels were hot-dipped galvanized and further protected by the new flashing system. Fortunately, the contractor was able to remove, salvage, and reinstall all intact cast stone units, so the project scope for cast stone replacement did not increase.
This example offers several lessons from which the observer can learn:
- Things are not always as they appear.
- Do not assume previous interventions on an older building were well-designed and properly executed.
- Close-up inspection (and inspection openings) can yield very important information.
- The cost of further inspection would have alerted the new owner to the potential additional cost of repairs. Caveat emptor—let the buyer beware!
The opinions expressed in Failures are based on the authors’ experiences and do not necessarily reflect those of The Construction Specifier or CSI.
Deborah Slaton is an architectural conservator and principal with Wiss, Janney, Elstner Associates (WJE) in Northbrook, Illinois, specializing in historic preservation and materials conservation. She can be reached at dslaton@wje.com.
David S. Patterson, AIA, is an architect and senior principal with the Princeton, New Jersey, office of WJE, specializing in investigation and repair of the building envelope. He can be e-mailed at dpatterson@wje.com.
Kenneth M. Itle is an architect and associate principal with the WJE Northbrook office, specializing in historic preservation and investigation and repair of the building envelope. He can be reached at kitle@wje.com.