Condensation: The misunderstood problem
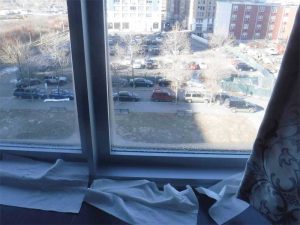
Several occupants, having performed some limited review of the offering plan and the internet (and with little background in architecture or engineering), concluded the aluminum windows and doors were not thermally broken as noted in the offering plan, and assumed they would have a strong case against the building’s developer as a result. The authors’ firm performed a review of the available project documents (both architectural and mechanical drawings) as well as the offering plan, followed by an initial review of the building. Data logging devices were installed to record temperature and RH conditions within several units (almost all units at the building had reported some condensation) as well the ambient exterior conditions.
A review of the basic design parameters for the building showed the building enclosure and mechanical systems were in accordance with the relevant code requirements. A review of the window shop drawings combined with observations in the field confirmed the installed windows were thermally broken, with performance exceeding the code minimums for both U-factor and solar heat gain coefficient (SHGC). Based on these initial findings, combined with spot-measurements of high RH in several units, the investigators focused on the performance of the installed mechanical systems.
The mechanical system design utilized the ‘corridor ventilation’ strategy. This approach is primarily used due to its low installation cost since ductwork is only required for the corridors, not to each individual unit. Fresh air for the individual units is provided to the common corridors, where it is assumed to flow into the units at undercuts in the entry doors (driven by a pressure differential in the units that was created by exhaust fans). As opposed to a more controlled approach delivering a set quantity of air directly to the units (but requires more equipment and ductwork, or more façade openings), corridor ventilation cannot guarantee enough air reaches each unit, being subject to imbalances in exhaust flows between units as well as conditions at the unit entry doors, both of which are not directly addressed in the mechanical or building code. The two major impediments to the functioning of this strategy in the subject building were a lack of undercut on the entry door (which was sealed with a sweep gasket) and the use of intermittent bathroom exhaust, that was controlled by a switch and occupancy sensor in each bathroom. This meant fresh air from the corridor had a reduced pathway and intermittent driving force to enter each unit, thereby resulting in poor ventilation/air exchange within units.
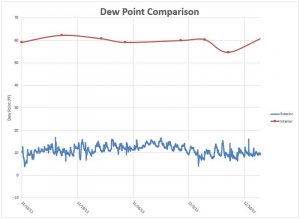
The combination of an airtight exterior enclosure and inadequate ventilation resulted in extremely high RH within the space at a time (winter) when a typical mechanically ventilated building would be the driest. The authors had compared the measured interior dewpoint to exterior weather data for the project location. Comparing interior measurements to the exterior environment (Figure 7), the authors found interior dewpoints were high, far in excess of the exterior, with interior RH levels well over 60 percent. In a mechanically ventilated building, these same conditions would closely match or at least follow the same general trend. The disparity between interior and exterior conditions is indicative of occupant-generated moisture (cooking, showering, respiration, etc.) building up in the interior space, whereas it would be quickly removed/diluted with outside air in a properly ventilated space. A test of this hypothesis was performed by simply opening a window—within 10 minutes, the interior RH level had dropped by approximately 15 percent.
In evaluating potential remedial options, it was discovered the local fire code limited the size of the undercuts at unit entry doors. The reason for this was the entry doors to the units required a certain fire rating in conjunction with limiting the passage of smoke. In similar projects, this requirement often precludes the use of corridor ventilation as a viable strategy. This left the building occupants with a difficult situation—legal action against the developer would be difficult since ‘on paper’ both the architect and the mechanical engineer met the basic standard-of-care requirements in the respective codes. Options presented included localized ventilation (window trickle vents or dedicated through-wall heat recovery ventilators), new supply air ductwork between the corridors and the units, and the introduction of constant-run exhaust fans for the bathrooms to promote more airflow into the units. Larger undercuts at the entry doors were not an option given the fire code requirements, which could not be overcome without adding features to the fire alarm and mechanical systems. All options would require moderate-to-significant expense and, in some cases, modification of the exterior appearance of the building. Unfortunately, as is often the case with these projects, the authors developed multiple technically viable solutions, but given the complexities of the building and ownership, as well as the high cost of remedial repairs, the problems remained unresolved at the time of writing this article.
Conclusion
While condensation is by no means a new problem, many aspects of the design and construction of modern buildings, as well as people’s general expectations, have brought the issue to the forefront in recent years. Design professionals must be careful to understand the interior environment, select building enclosure systems with the appropriate thermal performance, and integrate them into the facility in a manner to reduce or eliminate thermal bridging. While it is possible to identify and remediate these issues, as the case studies above show these ‘fixes’ can be expensive and often involve legal action. In almost all cases, these efforts will cost more and take more time than properly designing the systems at the outset.