Critical threshold for concrete moisture content
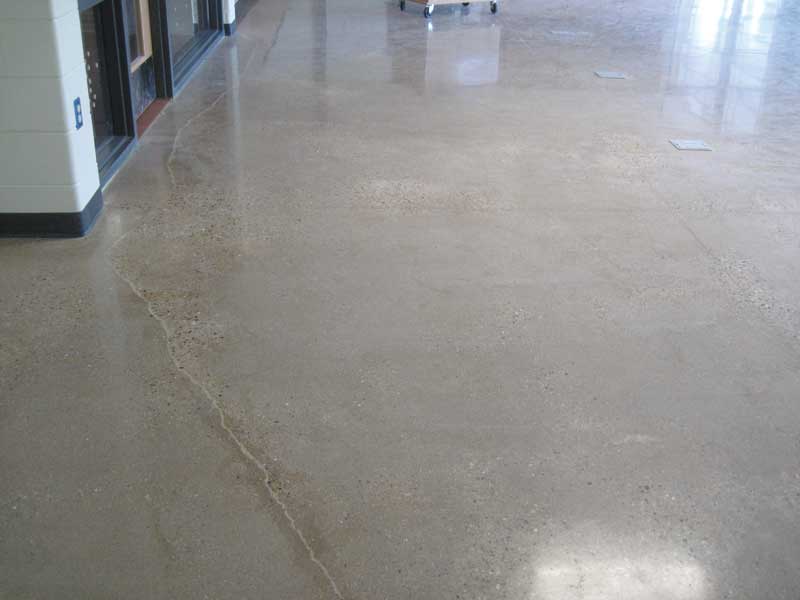
Photos courtesy Paul Potts
Water-cement ratio
A mix designed with a low w/c ratio results in a flatter concrete surface with less curling and long-term shrinkage cracking. It also reduces the months that are required to get the relative humidity (RH) of the slab to a point where it is safe to apply moisture-sensitive floorcoverings. (For more, see page 26 of the American Concrete Institute’s (ACI’s) Guide for Concrete Slabs that Receive Moisture-sensitive Flooring Materials, reported by ACI Committee 302.)
The most direct way to reduce moisture content in concrete is by specifying a low w/c ratio mix design. The compressive strength of concrete is directly related to the w/c ratio—as the strength goes down, water-cement ratio goes up. This puts more water in the concrete. (This comes from page 77 in the PCA Design and Control of Concrete Mixtures.)
Many structural engineers are comfortable with 24-MPa slab-on-grade concrete for commercial buildings. True, this level of compressive strength is adequate for applied loads in such buildings (and is very workable), but it will have a w/c ratio of 0.60, which has too much surplus water. The extra water increases the shrinkage potential of concrete, making it prone to cracking and curling; the added moisture takes extra months in order to evaporate to a level acceptable to apply moisture-sensitive floorcovering adhesives.
Critical water threshold for hydration
There needs to be a critical balance in the proportioning of water to cement for the optimal performance of concrete—neither too little water nor too much. There must be enough water to keep up with the moisture lost to evaporation before curing materials are applied and still completely hydrate the cement. However, there must not be so much as to leave a large surplus behind that will evaporate, causing the slab to contract excessively, thereby increasing shrinkage cracking and curling or increasing the wait-time for concrete to be ready for moisture-sensitive adhesives.
According to one industry article:
To achieve complete hydration, all the pores within the system must be filled with water throughout the hydration reaction. If a w/c ratio of 0.36 were used, the pores would not remain full during the entire reaction; thus, to achieve 100 percent hydration, a minimum w/c ratio of 0.42 is required. (Visit precast.org/2010/05/water-to-cement-ratio-and-aggregate-moisture-corrections.)
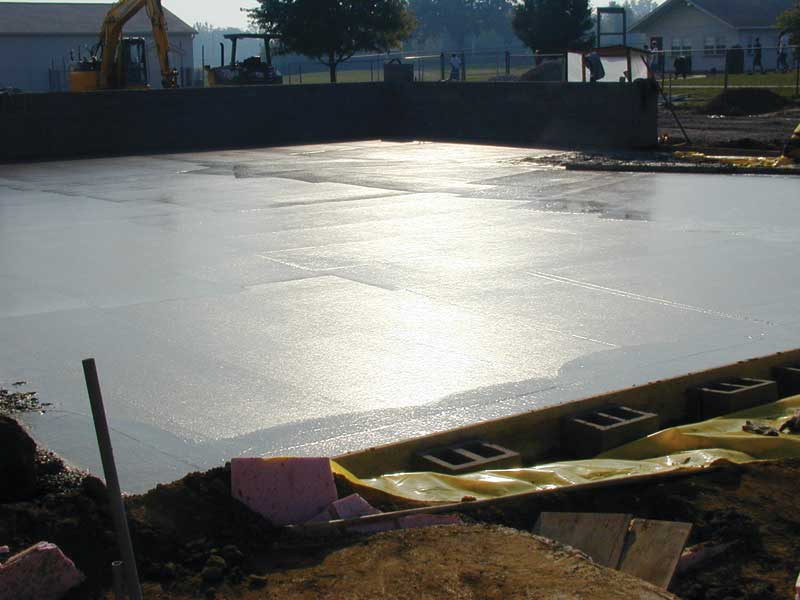
Concrete mixtures require a minimum 0.36 w/c ratio to completely hydrate the cement, but extra water above 0.36 is needed to improve workability and make up for the water lost to bleed water and evaporation. Experts differ on the specific critical threshold, but most conclude it is around 0.42 w/c ratio. The optimal maximum water-cement ratio for floors-on-grade in commercial buildings is 0.45 w/c ratio. This mix design results in stiffer, harder-to-place concrete that needs a medium range water reducer to aid with placement. (Optimal maximum w/c ratio for commercial buildings is 0.45. For more, see Ken Hover’s Summer 2002 article, “Tech Stuff: Curing and Hydration,” in Concrete News.)
Surplus water
Surplus water in concrete, over and above what is consumed by hydration with cement, is locked in the gel and capillary pore structure. It takes months to evaporate to a level acceptable to apply moisture-sensitive floorcoverings. Surplus water is necessary to an extent to improve workability, but when added in excessive amounts, simply to ease placement, it is a detriment to the desirable qualities of concrete. (See Researchgate Publication 229748, Chapter 6.11, “Cements as Porous Materials,” by Jeffrey Thomas and Jeffrey Chen [Northwestern University’s Departments of Materials Science and Engineering, and Civil Engineering].)
Negative consequences of surplus mix water may include:
- its eventual evaporation causes the slab to contract excessively, worsening long-term shrink cracking;
- loss of surplus water at joints and edges of the slab, and poor aggregate selection, worsens curling; and
- surplus water locked in the pores of the concrete evaporates only slowly over time, maintaining an elevated core RH that delays the installation of moisture-sensitive floorcoverings.