Critical threshold for concrete moisture content
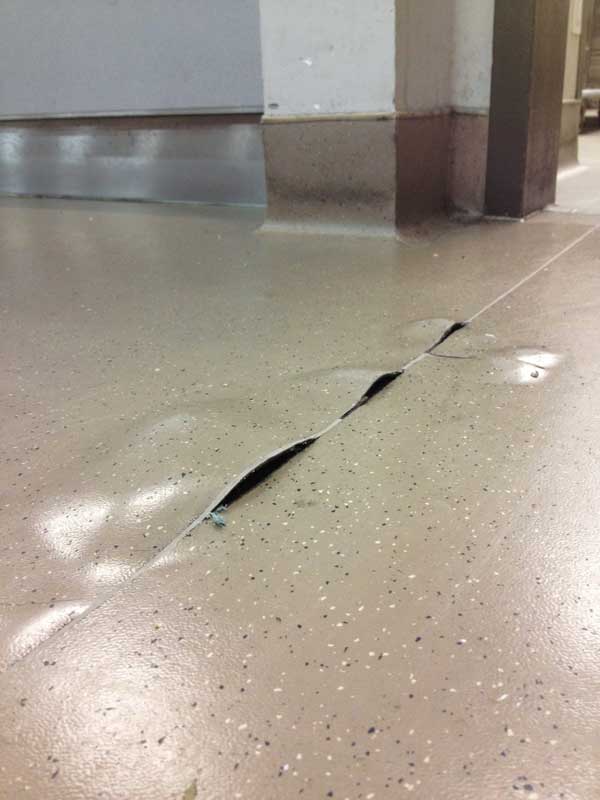
Photo courtesy Chris Maskell (National Floor Covering Association)
Moisture-sensitive adhesive failures
In previous years, solvent-based adhesives were impervious to moisture, but these products are now banned by the Clean Air Act because they contain volatile organic compounds (VOCs) that contribute to ground-level ozone or smog. Solvent-based adhesives have been replaced by water-based products that degrade in the presence of moisture from the slab. Therefore, it can be challenging to get the concrete sufficiently dry to apply the floorcovering.
Moisture-sensitive adhesives fail when surplus moisture trapped in the pores of the concrete is released over time and rises to the adhesive bond layer degrading the adhesive. To protect themselves, adhesive manufacturers now require concrete be dried to a low central core RH before water-based adhesives are applied or the warranty is voided. When there is no vapor barrier (or one has been improperly placed), groundwater from under the slab brought to the surface by capillary action keeps the slab moist indefiniteley. (For more about capillary action in concrete, see National Ready Mixed Concrete Association [NRMCA] CIP-28, Concrete Slab Moisture. Visit www.nrmca.org/aboutconcrete/cips/28p.pdf.)
Curing concrete and the drying period
Concrete does not harden by drying, but rather the cement in concrete needs moisture to hydrate and become hard. As there is limited surplus water to lose to evaporation in dryer mixtures, with low w/c ratios (i.e. 0.45 w/c ratio and below), curing must begin as soon as the concrete is hard enough to resist damaging the surface. (See page 4 in the PCA Design and Control of Concrete Mixtures.)
Curing keeps critical water from evaporating before the hydration of the cement is complete. However, after seven days, the curing products must be removed so evaporation of surplus water can begin. Extended curing times (beyond 10 days) unnecessarily delay the start of the drying of concrete. (For more, see page 26 of the American Concrete Institute’s (ACI’s) Guide for Concrete Slabs that Receive Moisture-sensitive Flooring Materials, reported by ACI Committee 302.0.)
Polyethylene film works well for curing slabs that will receive moisture-sensitive adhesives because evaporation begins as soon as it is removed. Water curing, and burlap water curing, adds new moisture into the slab extending the wait-time or drying period. Finally, it is difficult to predict when membrane-forming curing compounds will dissipate from the surface (short of sand-blasting them off) because of a lack of direct sunlight. (For more, see page 22 of the American Concrete Institute’s (ACI’s) Guide for Concrete Slabs that Receive Moisture-sensitive Flooring Materials, reported by ACI Committee 302.)

Photo courtesy Paul Potts
Long-term shrinkage cracking
Above a critical threshold, water is the enemy of good concrete proportioning. For this article’s purposes, that threshold is a w/c ratio of 0.45. Water above this ratio incrementally leads to more long-term shrinkage cracking and curling, and delays floorcovering installation.
Long-term (as opposed to plastic) shrinkage cracking occurs when the loss of excess water causes the slab to shrink, but it is prevented from contracting uniformly by friction with the subgrade or mechanical penetrations. By way of illustration, if a 30 x 30-m (100 x 100-ft), 100-mm (4-in.) thick concrete slab was poured on a perfectly flat, slippery surface where the concrete could shrink uniformly, no shrink cracking would occur. (This comes from PCA’s Design and Control of Concrete Mixtures, Chapter 13, “Volume Changes of Concrete,” on page 151.)
Long-term shrinkage cracks will telegraph through bonded floorcoverings (e.g. thin-set cementitious or epoxy terrazzo). Concrete with 0.45 w/c ratio produces strong (i.e. 34.5 MPa [5000 psi]), compressive-strength concrete with minimal long-term shrinkage cracking. Mixtures with higher water-cement ratios above 0.50 have much more water and, thus, greater shrinkage potential. Lab work done by the Massachusetts Institute of Technology (MIT) shows for each one percent decrease of mixing water, concrete shrinkage decreases by two percent. (For more, visit www.engr.psu.edu/ce/courses/ce584/concrete/library/cracking/dryshrinkage/dryingshrinkage.)
Minimizing cement paste to reduce total water
Coarse aggregates for concrete are irregular in shape, causing gaps between the individual stones of the same size even when compacted tightly together. In concrete terminology, these gaps are void spaces that must be filled with cement paste to make high quality concrete. Reducing the void space reduces the cement and water (cement paste) requirement—a basic goal of designing concrete for floors. (See PCA Design and Control of Concrete Mixtures, page 33.)
The void space can be reduced when larger maximum size aggregates are used, and two or more aggregate sizes are combined. Larger allowable maximum size graded aggregates ranging between 9.5 and 38 mm (3/8 and 1 ½ in.) have less void space than smaller maximum size aggregate ranging between 9.5 and 19 mm (3/8 and 3/4 in.), for example. The larger the maximum size stone allowed in a graded mixture, the less paste required. (See PCA Design and Control of Concrete Mixtures, page 31 and 32.) However, the size of the largest aggregate must be consistent with physical restraints of formwork and other building elements.