Critical threshold for concrete moisture content
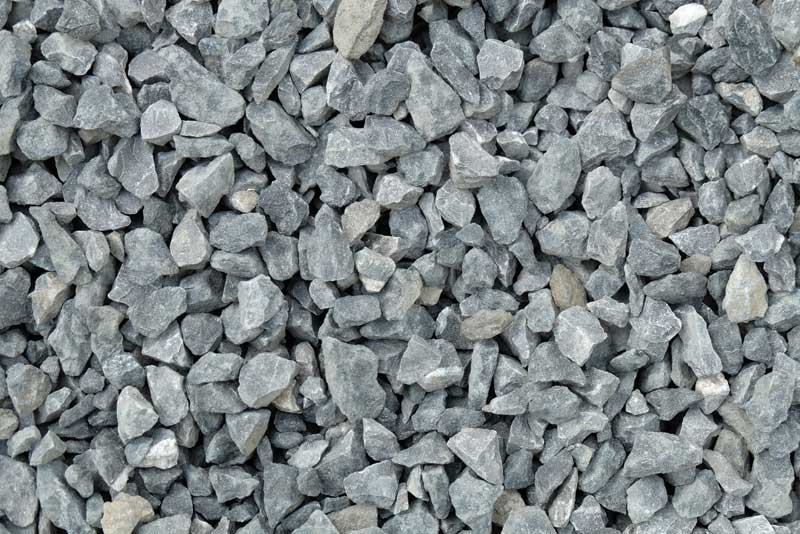
Photo © BigStock.com
Size and quantity of aggregates and paste content
Aggregates, the least expensive material in concrete (other than water), make up 60 to 75 percent of the total volume of wet concrete—they contribute significantly to the economy of concrete as a building material. The volume relationship between aggregates and cement paste is such that increasing the quantity of aggregate decreases the quantity of cement paste needed to make a cubic meter of concrete.
Additionally, aggregates in concrete must float in a matrix of paste and be completely coated with cement paste. Larger maximum-size coarse aggregates have less surface area than an assortment of smaller coarse aggregates; the larger aggregate requires less cement paste to coat all the surfaces, reducing the paste and thus the total water requirement of the mixture. (See PCA Design and Control of Concrete Mixtures, page 35.)
Therefore, greater quantities of graded coarse aggregates and larger allowable maximum size coarse aggregates reduce the paste requirement for a concrete mixture, reducing the shrinkage potential. (See PCA’s Concrete Floors on Ground, page 22.) For these reasons, careful prescription of the maximum size and grading of coarse aggregates has a significant impact on the total water content in concrete.
There are more benefits to greater quantities of course aggregate. Aggregates have a lower shrinkage potential than cement paste; as the quantity of coarse aggregate is increased in the mixture, the shrinkage potential of the slab is reduced. Additionally, large coarse aggregate exerts an internal drag on the shrinkage movement of concrete, counteracting the shrinkage potential. (See PCA’s Concrete Floors on Ground, page 22; the size and amount of coarse aggregate can be found in Chapter 4 [page 21].)
Aggregate components smaller than 6.4 mm (¼ in.) but not less than 0.076 mm (0.003 in.), retained on No. 200 sieve, are considered ‘fine.’ They represent 35 to 45 percent by mass or volume of the total aggregate content. (See Chapter 5 “Aggregates” [page 80] of PCA’s Design and Control of Concrete Mixtures.) Fine aggregate functions mostly as filler to reduce the required cement paste by filling the void spaces between coarse aggregate.
Where are contractions joints necessary?
Hand-tooled or saw-cut contraction joints in concrete floors are for aesthetic purposes. They guide concrete to shrink crack in uniform patterns more pleasing to the eye, instead of unpredictable random cracks. From another perspective, tooled contraction joints are the source of most curling in concrete slabs. The question then becomes, do you always need contraction jointing? The answer is no.
Concrete is perfectly flat when random cracking is allowed instead of tooling contraction joints. For this reason, it may be beneficial to omit contraction jointing altogether under carpeting, linoleum, and floating wood gymnasium floors. Concrete allowed to randomly crack must be made from a low-shrinkage mix design and incorporate welded wire reinforcement to keep the joints tightly together. While synthetic fiber mesh is not a substitute for welded wire reinforcement in this application, steel fibers in the right proportions will work.
A few extra tips
Concrete for anchored wood gymnasium floors should not exceed 27.6 MPa (4000 psi) as power-actuated anchors will not penetrate higher-strength concrete. (The anchor will just knock a spall out of the surface of the concrete.)
Inspectors and construction administrators should be aware of the difficulty in removing rinse-water from the mixer drum that has been left over from a previous truckload (if it is ignored when refilling the truck, it becomes unaccounted for mix water). The inspector should review this issue with the batch plant operator to come to an understanding of how leftover water from the last load will be accounted for in the fresh load.
Conclusion
There is a critical threshold for water in concrete—there must be enough water to hydrate the cement, but not so much as to worsen shrinkage cracking and curling, or exacerbate delays in the application of moisture-sensitive floorcoverings. A certain amount of excess water is needed to aid in placement and completely hydrate the cement allowing for water lost to evaporating before curing is started. Nevertheless, placement cannot become the driving force in determining the amount of excess water when moisture-sensitive adhesives are the concern. Workers must not be allowed to hinder the long-term schedule by adding water at the site. The designer must anticipate this problem and add a minimum requirement for midrange water-reducer to the specification.
The surest way to stay safely within these parameters is to specify a low water-cement ratio for the concrete and supplement the benefits of a low w/c ratio with careful selection of size and quantities of a graded aggregate. However, one must be indful a low w/c ratio mix design requires a timely application of curing materials.
Paul Potts is a technical writer, owner’s representative, and construction administrator. He has worked in the construction industry as an independent contractor and administrator for architects, engineers, and owners in Michigan. Potts can be contacted via e-mail at paulpotts1@comcast.net.