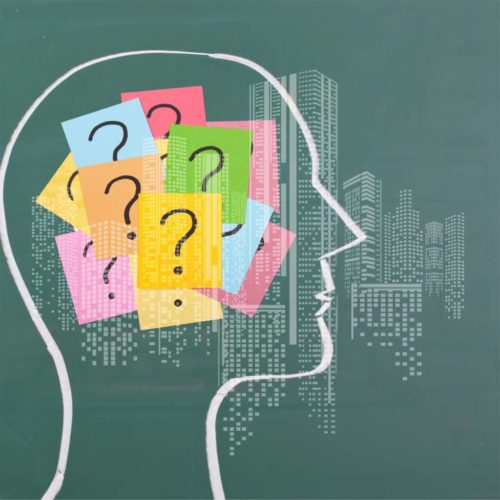
Image courtesy Liberty Building Forensics Group
by George DuBose, CGC, Steven Gleason, PE, and Nate Sanders, CIH, LEED AP
Unfortunately, it appears to be déjà vu all over again when it comes to water-related building failures. As new buildings are being constructed, the same design and construction deficiencies of the past are being repeated, leading to potentially catastrophic mold and moisture problems.
With preventative solutions having been published for many years, it may seem strange the industry makes the same basic mistakes time after time. Part of the problem rests in the fact that during the Great Recession, a good number of the largest design/construction firms lost many key employees. As a result, the institutional knowledge that had formerly kept construction projects out of trouble disappeared along with these key thought-leaders.
Since many firms can no longer rely on legacy partners to deliver this information to the next generation, they must quickly find good alternatives, both for the sake of their projects and for the very viability of their own future. As an industry, we know we can prevent buildings from failing because we are able to fix them once they do fail.
One of the best and quickest fixes, regarding preventative measures, is the implementation of a third-party peer review that ensures design/construction firms get the right information to the right people at the right time, allowing them to address any potential issues from the earliest phases of a new building project.
A firm should establish and distribute specific written design and construction guidelines at the project’s inception, and then use periodic peer reviews throughout the design/construction process to compare progress against the original guidelines. When implemented, these steps become the foundation of a practical model for improving the performance of both new and renovated buildings.
The premise behind this model is crucial decisions must be made at each stage of a project’s life—design, construction, and operation—to avoid problems and control costs. When such choices are properly applied, the incidence of building problems substantially decreases and the initial construction cost or schedule is not affected. These achievements are possible by eliminating many redundant and unnecessary building system components or procedures that often add nothing valuable to the ultimate performance of a building.
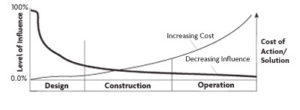
Image adapted from American Society of Civil Engineers (ASCE) 1988
A modular example
The emergence of modular assemblies as an option for new construction is becoming mainstream. However, this industry has had its share of mold and moisture problems, especially in warm and humid climates like the Southeast United States. Both wood-frame and steel-frame modular construction have experienced problems with condensation in crawlspaces, marriage walls, and ceiling-to-floor cavities, resulting in deterioration of the wood and wallboards, corrosion of metal floor pans, and proliferation of mold.
The greatest risk of modular construction failures has occurred when it is used for hotels, student housing, senior living, or soldier housing—generally, facilities that are domicidal or multifamily in nature. The reason for this risk probability is due to inherent similarities in requirements for the living units of these types of facilities, such as an individual cooling/heating unit, bathroom exhaust, and some sort of central HVAC makeup air system. Additionally, the abundance of modular boxes in these kinds of buildings increases the number of marriage wall interior cavities and ceiling-to-floor cavities that otherwise might not be required in other types of modular construction.
In a hypothetical case-study example, a modular construction unit had inherent interior hidden spaces that made it difficult to control the infiltration of outdoor air. (In wood-frame modular construction, this is typically the cavity between modular boxes, while in steel-frame systems, it is usually the spaces between modules.) These interior cavities provided a pathway for airflow to not only readily enter the building but also to travel long distances throughout the building, washing interior surfaces. This caused direct condensation and/or raised surface conditions that led to physical damage and mold growth on wood framing and interior drywall.
Each modular box, as it came from the manufacturer, had been designed and constructed in a vacuum of the requirements for the overall performance of the building. This was especially true in the HVAC system design and construction for building pressurization.
In modular box design coming straight from the factory, both the cooling/heating unit and the bathroom exhaust generally depend on the separate common area HVAC system for make-up air. This factor is often overlooked in the design and construction of modular facilities. In fact, the pressurization of the overall building is dependent on the pressure characteristic of each interior space, whether it is occupied by people or the area between two modular boxes. Similarly, the air leakage characteristics of modular construction buildings depends on not only the leakage rate of the modular box itself, but also on the leakiness between and around the compartments making up the building (both occupied spaces as well as the wall cavities between modular boxes).
In this example, the modular design and construction used pilings as its foundation. The resultant crawlspace adversely impacted the ability to control condensation and outdoor airflow in and throughout the building.
The modular design and construction process had a ‘modular box versus base building’ conflict inherently built into how it was delivered. Modular boxes are designed and manufactured by a separate entity from the one designing and constructing the base building. Veritably, the crawlspace, roof, attic, exterior cladding, and HVAC system are more often than not designed by one entity and constructed by another.
Inspections for code compliance can be different for the modular construction versus the base building construction. This often varies depending on the jurisdiction in which modular construction is either manufactured or constructed. In Florida, for example, modular construction is governed by the Department of Community Affairs (DCA). This includes inspection of each modular box before it leaves the manufacturing facility. The base building, on the other hand, is inspected by the local code official. This individual does not inspect the modular box since it has already received the DCA inspection and certification. While both governmental agencies rely on the same building codes, the silo inspection process competes with a more holistic process that has the overall building performance as the overarching goal.