Designing balcony railings for windy vibrations
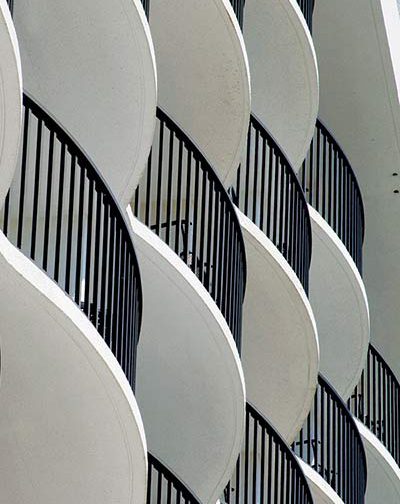
by Mahmod Samman, PhD, PE, FASME
Balcony railings come in different shapes, materials, and styles. When railings are installed in high-wind areas, design teams must verify the adequacy of their dynamic characteristics in order to ensure occupant safety and comfort.
One of the most common railing designs is an aluminum frame with vertical pickets (Figure 1). The popularity of this material is attributed to a combination of factors such as:
- aesthetics;
- view;
- strength;
- durability;
- lightness;
- rust-resistance; and
- relatively low material and installation costs.
From a structural standpoint, balcony railings are primarily designed to withstand mechanical loads imposed by occupants. Since this design criterion can be easily met using a metal like aluminum, the need to produce less-expensive options resulted in products designed to minimize weight.
In many applications, new lighter-weight aluminum railings still work because they satisfy structural requirements and applicable safety standards. However, in high-rise buildings, especially in coastal areas, these products can suffer from a serious, previously unknown, functional failure. The lighter structural members can become flexible enough to experience resonance under wind excitations. When this happens, the resulting noise and vibrations can make these costal properties virtually uninhabitable. Additionally, the dynamics of resonance can cause fatigue damage in these structural members that can lead to structural failure of connecting welds.
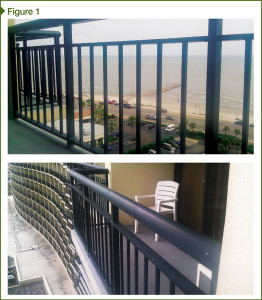
Images courtesy Mahmod Samman
Structural considerations
As shown in Figure 2, aluminum balcony railings are usually composed of vertical columns anchored to the floor, two or three horizontal beams running between the columns, and vertical pickets between the beams. These members are usually joined using welded connections (Figure 3).
Like all structures, the response of balcony railings to dynamic excitation is defined by natural frequencies and mode shapes. Natural frequencies (i.e. number of oscillations per second) are dynamic weak spots at which structures lose most of their strength. If a structure is excited at any of these frequencies, it vibrates excessively. The mode shape associated with each frequency is the shape of oscillation the structure exhibits. Lower frequencies are easier to excite because they require less energy. The lowest frequency is usually referred to as the ‘fundamental frequency’ because it is the easiest and most likely to excite and observe in everyday structures.
The frequencies and mode shapes of any structure are a function of mass, stiffness, and to a lesser degree, damping. Natural frequencies increase as mass decreases and stiffness increases. If increasing the stiffness is accomplished by adding mass, the net impact cannot be predicted without an engineering analysis. In most cases, however, proper stiffening of structures causes a net increase in natural frequencies, making the structure more difficult to excite into resonance.
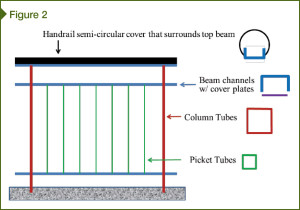
The dynamics of balcony railings
The stiffness of aluminum balcony railings is a function of several factors, including:
- material strength;
- cross-sections;
- span lengths; and
- the type of connections joining the structural members.
The effort to lower the cost of aluminum railings resulted in designs consisting of longer members, smaller cross-sections, thinner walls, and weaker-welded connections—all of which make these railings more flexible and susceptible to dynamic resonance at lower natural frequencies.
When railings are exposed to high-speed winds in high-rise buildings and coastal areas, air flow can produce sufficient dynamic excitation to set these railings into resonance. The mechanism producing this dynamic excitation is vortex shedding.
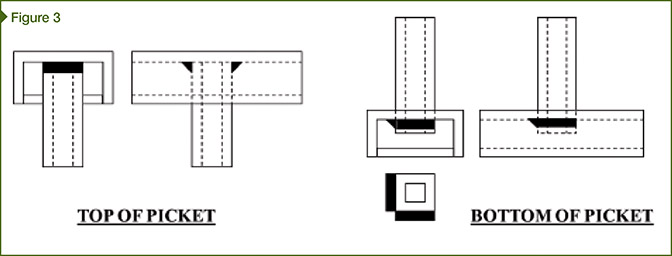
Vortex shedding is the unsteady oscillating fluid flow that occurs when the flow of a fluid (i.e. air or water) is disrupted by an elongated object. For this phenomenon to occur, fluid needs to flow at a certain velocity range that depends on the size and shape of the disrupting object. Due to this unsteady flow, vortices are created at both sides of the back of the object with the stronger vortex alternating from side to side.