Dispelling common myths associated with poured gypsum floors
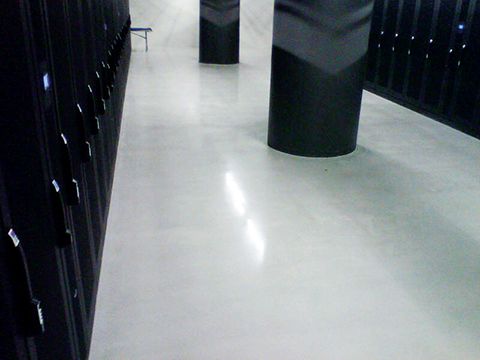
Aggregates
The introduction of an aggregate such as sand to the hemihydrate slurry will reduce the strength of the hardened mass because it spreads the new hydrated gypsum crystals apart. Sand also prevents the new hydrated gypsum crystals from growing into each other. Further, the sand does not chemically bond to the newly formed crystals; instead, the sand becomes trapped and locked within the crystal matrix.
Since sand is added to most gypsum cements, special attention must be paid to the quantity and type of sand that will help the slab meet the designed specification. One way to maximize how sand integrates with the slurry is to make sure the particles range in size and shape. Sand that is too angular and flat is not as good as sand that has a rounded shape. Sands that have a more rounded shape tend to ‘roll’ more than flat-shaped sand. This is important when trying to control the flow and leveling characteristics of the slurry.
Ultimately, given the rules previously described, one can deduce that excess water and the resultant negative effects of crystal growth will result in ‘soft’ or ‘chalky’ gypsum concrete floors.
In the last 15 years, advancements in formulations and more stringent installation procedures have improved the quality of gypsum-based levelers to the point where installed characteristics can exceed those of traditional PC and HAC products. Gypsum levelers in today’s market can be mixed to meet or exceed industry standards as being a suitable substrate for all types of floor coverings. Current technology can create hydrated products achieving compressive strengths that approach 137,800 kPa (20,000 psi), compared to approximately 34,450 to 41,340 kPa (5000 to 6000 psi) of normal PC and HAC products. This strength can be attained in as little as a few hours or days, not several weeks.
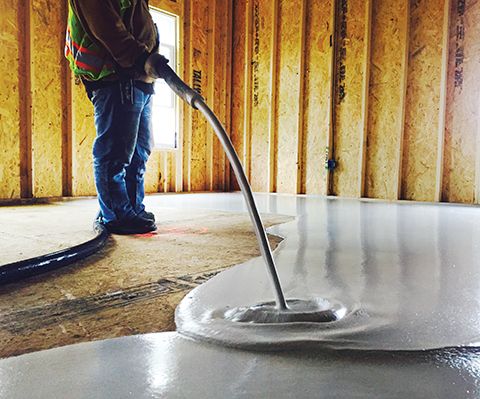
Myth number two
Gypsum-based underlayment will ‘melt’ when exposed to water.
Truth
Gypsum is soluble in water at a rate of 2 g/L (1 oz/3.64 gal) of water. This means a solution rate of 2 g/L of water, 0.45 kg (1 lb) of gypsum would require the equivalent to about 227 L (60 gal) of water.
For example, if 227 L of water were poured onto a floor that was being supported by a gypsum underlayment—such as in a bathroom or kitchen—in no way would 0.45 kg of gypsum just ‘melt’ away, especially considering the floorcovering would prevent most of the water from coming into contact with the gypsum underlayment.
If the floorcovering had not been applied, the majority of the water would probably be absorbed by the gypsum underlayment. Even if the water is completely soaked into the gypsum underlayment, erosion will not occur because the water solution will be saturated at a rate of 2 g/1 L and will just sit in the mass. Assuming the water source is eliminated, the underlayment will dry. The water will evaporate, leaving the gypsum which had been in solution to reside within the interstitial spaces of the crystal structure of the mass.
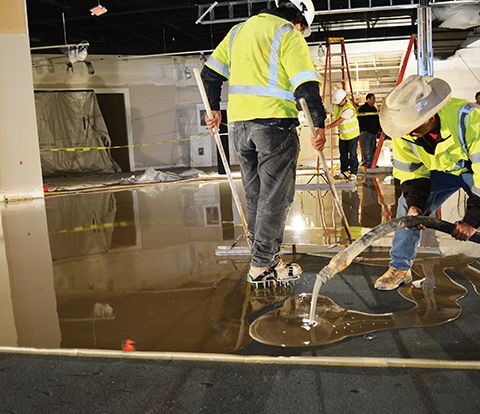
Myth number three
Gypsum concrete is not a hydraulic cement.
Truth
ASTM C219-07, Standard Terminology Relating to Hydraulic Cement defines hydraulic cement as:
a cement that sets in water and is capable of doing so underwater.
Gypsum completely fulfills this definition, and it is proper to call gypsum-based self-levelers a ‘gypsum cement’ (as it comes from the bag) and a ‘gypsum concrete’ (after it is sets up as a floor underlayment).
Features and benefits of poured gypsum floors
For most applications, gypsum levelers do not require shot blasting or scarification of the substrate or existing floor covering prior to application because gypsum concrete expands slightly during the hydration process. This is very different than the shrinking normally associated with traditional concrete as it cures. Some gypsum cements can even be stained and polished to provide a decorative wear surface.
Poured gypsum floors achieve high compressive strengths in hours versus a typical 28-day cure cycle for traditional cements. In wood-framed construction, gypsum can be poured directly on the wood without wire lath reinforcement at 19 mm (3⁄4 in.) minimum thickness to achieve a one-hour fire rating. PC requires a minimum thickness of 38 mm (11⁄2 in.) to achieve a one-hour rating. Over hollow-core concrete planks, gypsum underlayments can achieve up to four-hour fire ratings at half the thickness of Portland-based concrete. Gypsum levelers, when used in combination with sound mats, provide a sound transmissions class (STC) and impact insulation class (IIC) that will exceed the requirements of Section 1207 of the International Building Code (IBC). Gypsum levelers can also be poured up to 76 mm (3 in.) in a single lift as opposed to approximately 25 mm (1 in.) for traditional cement levelers.
Conclusion
Gypsum concrete is a favorable material to use as an underlayment for a variety of reasons. It requires less preparation, has excellent flow properties, can be poured deeper, and offers potential for better crack resistance. Some products manufactured with FGD gypsum can reach 90 percent recycled content and achieve higher compressive strengths than other materials. In most cases, a gypsum underlayment can meet or exceed the characteristics of a PC- or HAC-poured floor at a fraction of the installed cost.
Brett Fleury is a product marketing manager for performance flooring at USG. Out of his 17 years with USG, 10 were spent gaining sales experience in tile and flooring industry as part of the substrates and specialties division. Prior to joining the tile and flooring team, Fleury worked closely with architects, owners, and designers as a technical sales representative for USG’s ceilings and building systems divisions. He is also certified as a construction document technician by CSI. Fleury can be reached at bfleury@usg.com.