Healthy Concrete Systems: Defending design intent
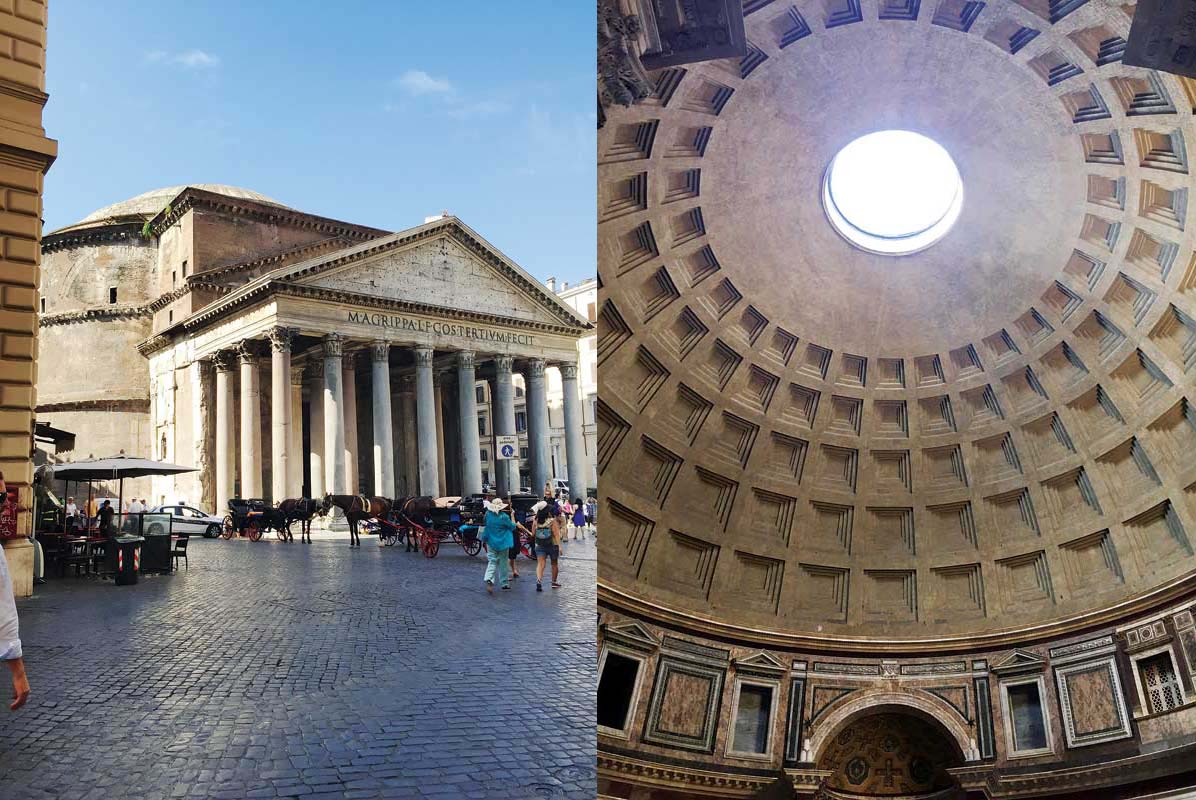
Photos © Tara Imani
Verification and definitions (or lack thereof)
The Ancient Romans figured out how to make concrete resilient and sustainable—the evidence remains standing today (Figure 3). However, specifying the physical properties of exposed concrete flooring seems to remain a nebulous challenge. This is primarily because the industry has not had a clear way of quantifying the exact definition of polished concrete.
According to the International Polished Concrete Institute (IPCI):
Polished concrete is a process which enhances the natural beauty of existing concrete by hardening and applying a sheen to the concrete. There are two primary methods to create this sheen: Topical or Mechanical.
However, this can be vague. Traditionally, it has been entirely up to the contractor to deliver a shiny floor by means of a prescribed process. The question is whether it was what the owner or architect expected. Who is to argue, given a vague specification that prescribes a process rather than a quantifiable and verifiable result?
Ensuring the intent
The goal is a floor that is aesthetically pleasing, durable, easily maintainable, slip-resistant, sustainable, and resilient. Taking the steps explored in the following section, these attributes can be established by way of the specifications and verified in the field.
Aesthetically pleasing
It takes a good slab that has been placed correctly to get controlled results. Flatness is important—one will not be able to get an even and consistent appearance if the slab is wavy and improperly cured. This is particularly true when a ‘cream’ finish with minimal aggregate exposure is desired.
Aggressive grinding, at additional expense, to expose more aggregate can even out the appearance, but does not guarantee the desired look. In fact, it forces the owner to accept another level of aggregate exposure. Sheen is also an aesthetic that can be achieved ranging from a dull/matte finish to a highly polished/mirror-like glossy finish. Of course, the more shiny the finish, the more noticeable the flatness. However, it is important to keep in mind ‘shiny’ is not the definition of polished (or refined) concrete; in many cases, a highly reflective finish is inappropriate. For example, a highly reflective floor in a toilet stall compromises privacy between the toilet compartments.
By specifying the industry standard for floor flatness and floor levelness, ASTM E1155, Standard Test Method for Determining FF Floor Flatness and FL Floor Levelness Numbers, an appropriate degree of flatness may be specified to suit the function and aesthetic of a space. Higher flatness/levelness numbers may only be achieved by skilled, certified installers.
The first method of specifying exposed concrete surfaces was based on ‘grit levels,’ and then measuring the light reflected off the floor. However, this proved too subjective and often unintentionally distorted original design intent. By instead measuring the refinement of the concrete itself using surface texture grades (STG) and roughness averages (Ra), one creates a common language for specifiers, contractors and the entire project team. This surface texture corresponds to the finished sheen of the concrete floor without the disguise of an applied surface sealer. Rather than using older subjective standards, both the design decision-maker and contractor now have a familiar, quantifiable language to not only express design intent, but also ensure it has been met. (Surface roughness is the science of measuring the physical texture of a surface. An STG is a specific measurement of the physical texture describing the roughness characteristics of the surface. The Ra, sometimes called roughness average, is an integral of the absolute value of the roughness profile; it is measured in either microinch (µin) or micrometer (µm). While used for many decades in the steel, glass, and plastic industries, a growing number of specifiers and contractors are using the following Ra measurements to describe physical refinement of concrete surfaces and quantify design intent: Matte (30 µin) Semi-gloss (16 µin) Glossy (6 µin) for the United States, and (0.76 µm) Semi-gloss (0.41 µm) Glossy (0.15 µm) for the rest of the world.)