Installing thermoplastic or rubber waterstops
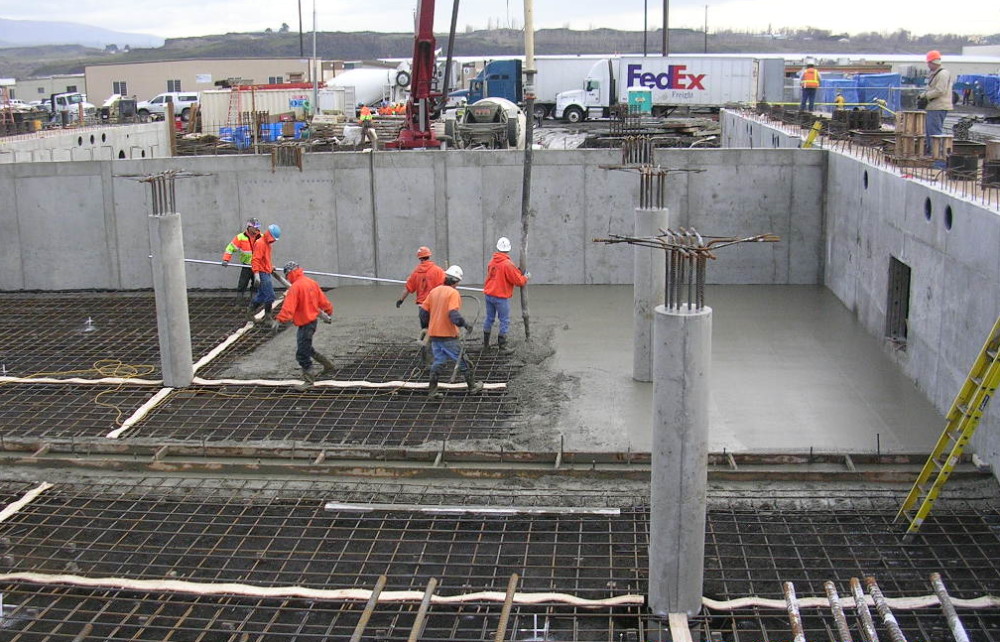
By Stacy Byrd, GRP, LEED AP
In the July 2015 edition of The Construction Specifier, this author examines various aspects of waterstops. In this web feature, issues concerning the installation of dumbbell and ribbed center-bulb models are explored.
Installation plays a critical part in the performance and effectiveness of a waterstop system—most failures occur because proper steps are not taken. The waterstop should be installed in a layout that forms a continuous watertight diaphragm. Dumbbell and ribbed center-bulb waterstops should be positioned with the longitudinal centerline of the waterstop coincides with the center of the joint. Prior to the first concrete pour, hog rings or grommets are applied to the outermost edges of the waterstop profile (usually at 305-mm [12-in.] intervals) to provide the installer with a convenient means of securing the waterstop to adjacent steel rebars. Tie wire is inserted through the hog rings to attach the waterstop and maintain proper positioning.
Several manufacturers provide guidance to position the waterstop so concrete coverage is not less than half its width. Clearance should be allowed between the waterstop and reinforcing steel of a minimum two times the largest aggregate size to prevent poor consolidation of concrete caused by aggregate bridging. Also, one must adhere to the manufacturer’s guidelines for depth of embedment in the concrete for various head pressures. General rule of thumb—for higher hydrostatic pressures, the waterstop is installed with greater concrete coverage.
Waterstops need splicing at intersections, changes of direction, or to form longer lengths. To form a continuous diaphragm, ends should be cut square before welding together adjacent rolls. Welds should be made by trained personnel using approved equipment and procedures. Uncoil waterstop rolls and lay flat for 24 hours before installation for ease of handling and fabrication.
Heat is applied using a thermostatically controlled electric splicing iron with Teflon-film cover to avoid adhering the waterstop material. After preheating the iron to the temperature recommended for the type of thermoplastic material, the waterstop ends are pressed against the hot iron until the material becomes slightly molten. The splicing iron is removed, and then the molten ends are immediately pressed together and held like this until cool (less than one minute). This heat-splicing method should only be employed with waterstops made of thermoplastic materials. Conventional rubber waterstops are typically cold-spliced using special adhesives.
In vertical joints, split-forming is used to hold the waterstop in position. However, special split-leg profiles can be attached to conventional concrete forms with nails. For all installations, one must ensure the center of the profile is aligned with the center of the joint.
Investigations have shown the majority of waterstop failures are caused by poor welds or that no welding was performed. Splices should be inspected to confirm they are welded through the entire profile thickness and not simply on the surface of one side (i.e. edge welding). One must also look for any charred, burnt, or otherwise-contaminated welds. Further, continuity of the center bulbs and ribs must be maintained as continuous throughout the weld. Edge welding waterstop seriously compromises the integrity of any product. Even limited movement of concrete can rupture edge welded splices because the thin-edge weld lacks proper tensile strength and elongation relative to the parent material.
Experience has shown field-welded mitered fittings are difficult to splice correctly. For this reason, it is recommended directional change fittings (e.g. Ls, Ts, and crosses) be prefabricated by the manufacturer, leaving only simple butt-splicing to be performed in the field. For example, a standard flat cross fitting has 12 cuts and seven welds. By using prefabricated fittings, all the cuts and three of the welds are eliminated from fieldwork.
The most leak-prone area is the directional change fittings. Prefabricated fittings can eliminate or greatly reduce this problem as the waterstop manufacturer has the specialized equipment and templates unavailable to the contractor in the field. Ls, Ts, and crosses are available in both vertical and flat styles.