Installing thermoplastic or rubber waterstops
During installation, one must avoid contaminating the waterstop surface with dirt, oil, or release agents. Surface contamination can interfere with direct contact of concrete with the waterstop, affecting its performance. Concrete must be carefully placed without displacing the waterstop from its position. The waterstop must be held in place properly during the first half of the concrete placement, with one half of the width embedded in the concrete. This must be carefully monitored for quality control to ensure the waterstop remains positioned during both halves of the concrete placement and consolidation. Far too often, the PVC waterstop ends up shifted, folded over, or the center misaligned with the joint, preventing it from functioning properly.
Additionally, with horizontal-run installations, any concrete that has extruded out into the flange must be removed. Finally, there is inspection for any damage that must be prepared—workers installing the reinforcing bars often burn, puncture, or cut the waterstop.
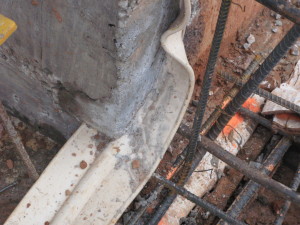
Base-seal profiles are suitable for construction, contraction, and expansion joints. Base-seal should not be used to make interior wall transitions as the embedment ribs are only on one side and therefore cannot function correctly.
Base-seal waterstops are installed before placement of the concrete and placed either on compacted grade, mud slabs, or vertical formwork. Base-seal waterstops are positioned such that only the ribbed side of the waterstop engages the concrete. Since the base-seal waterstop is not embedded in the concrete, a solid substrate is required for initial support as well as for proper in service performance. Lack of support can lead to edge curling of the waterstop when exposed to high hydrostatic pressure.
Care should be taken in the placement of concrete to prevent movement or displacement of the waterstop. Center-bulb tear-web varieties of base-seal can accommodate joint movements. For high hydrostatic head pressures, manufacturers recommend ribbed center-bulb embedded in the concrete instead of base-seal products.
Finally, one must always wear protective gear including, but not limited to, temperature-resistant gloves, safety eyewear, protective shoes, and a respirator in confined spaces. Welding should be done in a well-ventilated area.
Stacy Byrd, GRP, LEED AP, is the national products manager at CETCO, a manufacturer of waterproofing, green roof systems, composite drainage, and waterstops. He has a quarter-century of technical waterproofing design application and practical field experience with below-grade foundations, plaza-decks, tunnels, and vegetated roofs on commercial, institutional, civic, and government projects. Byrd is an active member with ASTM International Committee D08 on Roofing and Waterproofing and a Green Roof Professional (GRP). He can be reached at stacy.byrd@cetco.com.