Managing moisture without sacrificing breathability
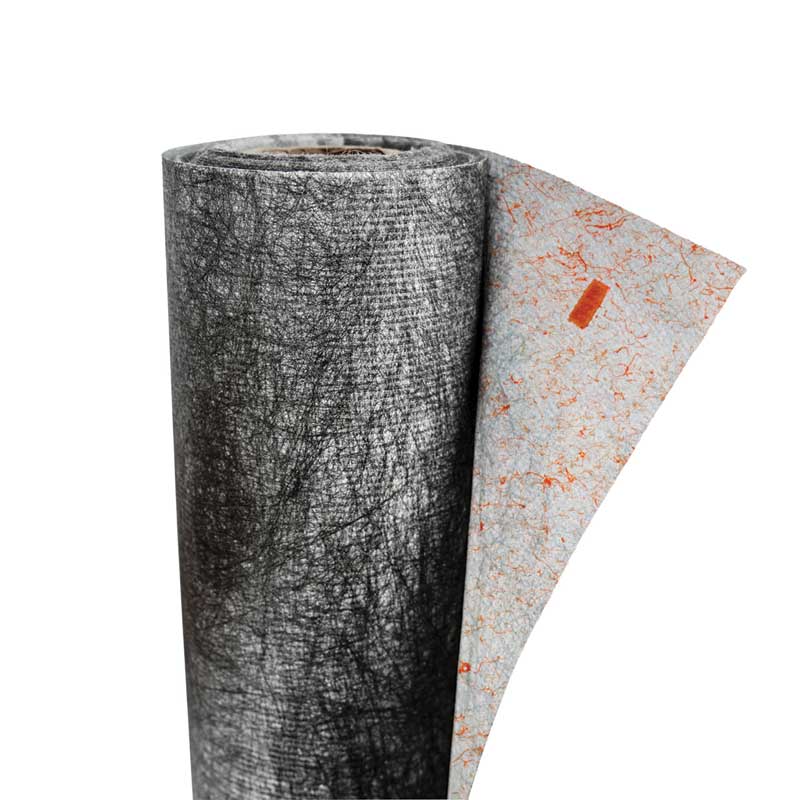
Other variables
Outside of the aforementioned evaluation criteria, specifiers must consider a number of other variables when selecting a WRB.
Cladding
In addition to the challenges associated with reservoir claddings, other types of cladding require careful consideration when it comes to managing moisture. For example, tightly fastened cladding such as cedar siding or fiber cement board might allow water trapped between the siding and a smooth building wrap to pool and could make its way through the wrap and into the framing. These are cases where a drainable building wrap would provide the needed capillary break to allow water to drain out of the assembly.
Surfactant resistance
The water resistance of a building wrap can be degraded by chemicals known as surfactants (or surface active agents), often found in cladding materials such as cedar and stucco and also in solutions used to power wash siding. These chemicals reduce the surface tension of water, easing its ability to pass through microscopic openings in the membrane. Some building wraps offer added protection against the harmful effects of these chemicals, which might be an important consideration for assemblies constructed using these materials.
Geography and climate
As stated, IBC now mandates an exterior wall assembly incorporate “a means for draining water that enters the assembly to the exterior.” However, a growing number of states have added even more prescriptive measures to their codes. Oregon, for example, now requires “…the [building] envelope shall consist of an exterior veneer, a water-resistive barrier (housewrap, building paper, etc.) and a minimum 1⁄8-in. [3-mm] space between the WRB and the exterior veneer.”
As a rule of thumb, the Building Enclosure Moisture Management Institute (BEMMI) recommends any area receiving more than 508 mm (20 in.) of annual rainfall should incorporate enhanced drainage techniques in the wall system, especially if using an absorptive cladding material. Areas receiving 1016 mm (40 in.) or more should utilize rainscreen design regardless of cladding material. The orientation of the wall, amount of overhang, altitude, and even nearby trees can have an impact on how much water intrusion can be expected and how likely it is to dry.
Taking a system approach
A WRB material alone—no matter how advanced it is—cannot be counted on to protect a structure from unwanted air and moisture movement without taking the whole assembly into consideration. It is important to specify compatible materials to ensure all components work together.
For example, sealants with high solvent or plasticizer content can damage bitumen flashing products causing functional and aesthetic issues. When seams and tears are not properly taped, they allow windblown rain to infiltrate the assembly. Failure to use galvanized roofing nails or plastic cap nails to attach the WRB to the sheathing and framing can also compromise performance.
To counter this problem, some manufacturers have developed a system approach including compatible tapes for seaming and adhesive flashings for openings. When installed together, these systems are often assured through extended warranties from the manufacturer. When in doubt, always check the manufacturer’s website for additional guidance.
Changing building codes and greater adoption of certain cladding materials have caused specifiers to take a closer look at how moisture is managed in the wall assembly. Advances in building wrap products have added a powerful tool to help achieve these goals. The smart way forward is to avoid waterproofing the wall to the detriment of breathability, but to rather take a holistic approach to designing a wall system providing adequate protection against water but also able to dry out when it inevitably gets wet.
Bijan Mansouri is the technical manager at Typar Construction Products. He has been with Berry Plastics for 25 years, working in different technical capacities. Mansouri is responsible for building code requirements, design and development of new construction products, and education on proper practice and installation of building envelope. He received his bachelor’s and master’s degrees in mechanical/aerospace engineering, and is a member of the Air Barrier Association of America (ABAA) and ASTM. He can be reached at bijanmansouri@berryglobal.com.