Preparing for risk through resilience
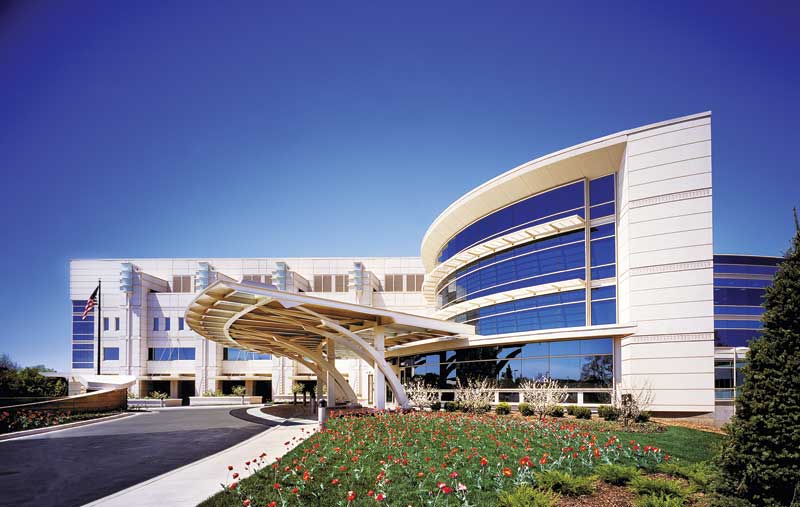
On January 21, 2015, some 240 units of the Avalon at Edgewater apartment complex were destroyed by what was originally reported as “a minor fire.” According to fire officials, the inferno spread quickly within the wholly code-compliant wood-frame construction—in spite of the fully functioning sprinkler system.
The Edgewater apartments had an active fire suppression system installed to NFPA 13R, Standard for the Installation of Sprinkler Systems, which does not require sprinklers be present in attics and concealed combustible spaces in residential structures up to four stories or 18.3 m (60 ft) high. Once the fire spread to these spaces, it became so intense it took roughly 500 community firefighters from 35 municipalities to douse the flames. (For more, check out the New York Times article, “As Construction Booms, Edgewater Fire Provides a Sobering Moment,” by Kate Zernike and John Surico, in the January 22, 2015 edition).
What makes this disaster such a telling example of the dangers of building with combustible materials is the fact it was the second time a major blaze occurred at the same site. Fifteen years earlier, the same type of light wood frame construction resulted in the entire apartment complex burning to the ground during the construction phase. The circumstance the complex was under construction with yet-to-be-activated fire suppression systems was seen as a major factor why, according to a witness, the blaze took “no more than 10 minutes” to spread from one corner of the site to completely engulf the entire 400+ unit complex. (Another New York Times article, “Fire in New Jersey Engulfs Apartments Near Hudson River,” by Andy Newman and Robert Hanley,” had covered this on August 31, 2000).The inferno threw flames hundreds of feet into the air and threatened to spread to a major fuel depot—it took 200 firefighters to subdue the flames the first time it burned.
Building assemblies for walls, partitions, roofs, floors, and ceilings are given fire ratings typically described in terms of being rated as ‘1,’ ‘2,’ or more hours. Building codes then require assemblies meet different fire ratings based on how critical they are to the structural integrity of the building and their exposure to fire risk. This is why wall assemblies around the building emergency exit stairs, for example, are required to have a relatively high fire rating, while internal partitions within an office space have no fire rating requirements.
Concrete and masonry materials combine noncombustible cement, water, sand, and aggregates and or materials such as stone, clay, and shale. They do not burn and their fire resistance has been long established. Specifiers consult American Concrete Institute (ACI) 216 /The Masonry Society (TMS) 0216, Code Requirements for Determining Fire Resistance of Concrete and Masonry Construction Assemblies, to design masonry and concrete elements. This standard gives tables showing most types of masonry materials and the required thickness to meet the desired fire ratings. It also supplies standard formulas for calculating fire ratings for concrete and masonry assemblies not specifically covered by the tables—one universal document for concrete or masonry assemblies. Individuals experienced in using the tables often develop go-to specifications based on the concrete and masonry assemblies most prevalent in their area.
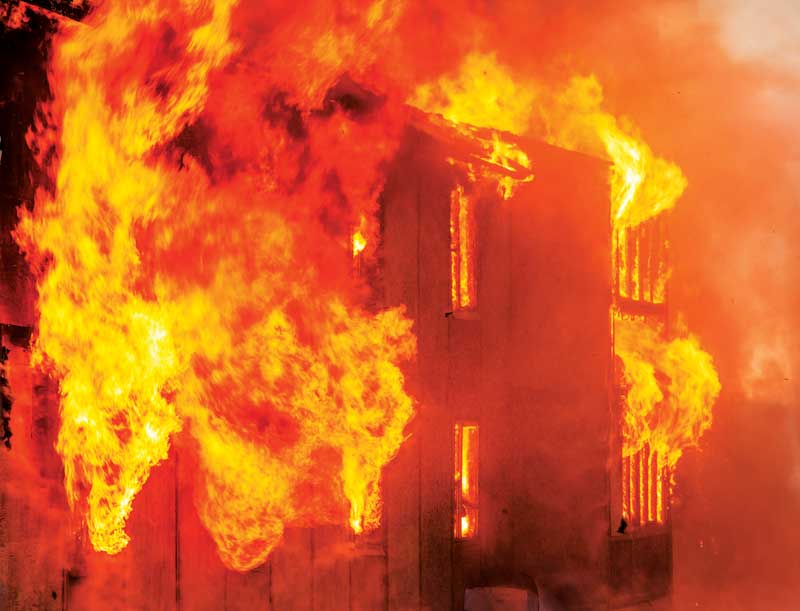
Photo © BigstockPhoto
Fire ratings for assemblies made of other types of building materials are established by testing the finished assembly based on ASTM E119, Standard Test Methods for Fire Tests of Building Construction and Materials. Usually paid for by the material manufacturer, this testing is done on fully constructed assemblies by third parties such as UL. In this way, assemblies—even those made up of components that would otherwise readily combust—can receive a certification such as a UL Classification number as meeting a certain fire rating.
However, there can be trouble when:
- installers fail to properly construct the assembly;
- it is exposed to heat or flame prior to being completed; or
- a component of the assembly is altered or damaged.
While it is tempting to avoid having to discern the tables in ACI 216/TMS 0216, it is important to keep in mind some assemblies certified to a minimum fire rating can still fail.
Insurance companies recognize the risk of comparative materials and reward more resilient building types. They limit their liability by covering less and, in some areas, charging seven to 11 times more for the fire portion of insurance in wood frame versus fire-resistant materials, including concrete. (See “Study of Insurance Costs for Mid-rise Wood Frame and Concrete for Residential Buildings,” a January 2016 report by Vancouver-based Globe Advisors).
Mitigating moisture
Fire risk is a substantial part of the exposure for which insurance companies compensate, but increased risk of water damage and moisture claims is also a big factor when offering coverage and setting premiums. Insurance rates are higher for owners building with materials susceptible to water damage. Whether from flood, leaks, or simply from being exposed to the environment during construction, water and moisture problems can lay hidden for years, resulting in trouble long after builder warranties and construction insurance policies expire. This can leave building owners or condominium associations liable for reparation costs.
Mold growth within walls, ceilings, and substrates is an all-too-common occurrence, resulting in costly mitigation. The consequence of vulnerable materials being exposed to moisture can be even more catastrophic. A tragic example occurred in June 2015 when a balcony collapsed in Berkeley, California, resulting in 13 college students plunging four floors to the street below—six perished. Investigators of the incident found the cause of the failure to be decayed wooden laminated veneer lumber (LVL) beams. The report, prepared by the City’s Planning and Development Department’s Building and Safety Division, said the balcony failed due to severely dry rotted deck joists that had been in service for less than nine years.