Rethinking rebar: Reinforcement goes green

Composite reinforcement
Composite rebar is not necessarily new, but it may not be as widely utilized as it should be. Unlike its steel cousin, composite rebar generally does not have any natural weakness to corrosion, which reduces the risk to the concrete around it. Composite reinforcement is also non-conductive, and in many instances, it has greater tensile strength compared to many types of steel rebar. Additionally, since composite reinforcement is lighter than steel, there are more benefits to the economic and carbon costs of its transportation.
There are two common types of composite rebar: glass fiber reinforced polymer (GFRP) rebar and basalt fiber reinforced polymer (BFRP) rebar. Fiberglass rebar is produced from glass fibers in a polymeric matrix. The polymer makes load transfer to the glass fibers possible, while the fibers themselves carry the load. ASTM D7957, Standard Specification for Solid Round Glass Fiber Reinforced Polymer Bars for Concrete Reinforcement, provides guidance for GFRP in structural applications. The Canada Standards Association (CSA) also provides specifics on building with composite rebar in CAN/CSA-S806-12 (R2017), Design and Construction of Building Components with Fibre-Reinforced Polymers. GFRP composite rebar is generally considered to be more carbon intensive than BFRP, 100 percent EAF recycled rebar, but less carbon intensive than stainless steel rebar, galvanized rebar, or standard BOF rebar. Basalt fiber reinforced polymer, sometimes known as “basalt rock rebar,” has higher tensile strength compared to steel and, like fiberglass, is non-corrosive. Basalt rebar also shares concrete’s same thermal coefficient of expansion and can be up to 89 percent lighter than steel, making its related carbon expenditures in transportation the lightest yet.
Research suggests the emissions from manufacturing BFRP rebar are 74 percent less than typical steel and 22 percent less than 100 percent recycled content EAF steel. Not only are composites lighter, and in some ways stronger than steel, but they also make sense in scenarios where water exposure is a risk to the long-term health of the concrete system.
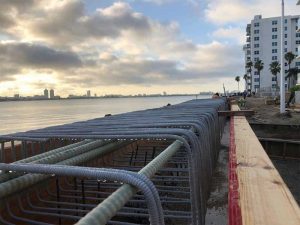
One example would be using composite reinforcement in a concrete slab which will also have a hydronic heating system. Hydronic systems embed tubes into concrete, which will carry heated water to warm the slab. However, if there is a leak and the hydroponic tubing is tied to metal reinforcement, there is certainly a risk of corrosion. Basalt and fiberglass reinforcements do not corrode. While this does not necessarily prevent a leak from happening within the slab, it will reduce the possible damage the leak will have on the entire slab. Basalt and glass fiber rebar installation guidelines for composite reinforcement of concrete are defined in ACI 440.6-08, Specification for Carbon and Glass Fiber-Reinforced Polymer Bar Materials for Concrete Reinforcement.
As previously noted, steel and composite rebar do not have identical mechanical characteristics. While composite rebar may have greater tensile strength, it can also have a lower modulus of elasticity than steel rebar. This can limit its application in certain scenarios. It is therefore important to check with the project team’s engineers to ascertain best uses, as well as serviceability limit state (SLS) and any municipal design codes related to sustained loads.
European rebar, produced with large amounts of manganese, has tremendous flexibility and is easy to work with. But, this same workability also makes it unsuitable for bearing heavier loads, extreme thermal change, or the effects of seismic shock. However, it can be less expensive than traditional rebar and have a smaller carbon footprint, making it potentially useful on smaller projects in areas with only subtle temperature swings.