Specifying and installing flashing around exterior wall openings
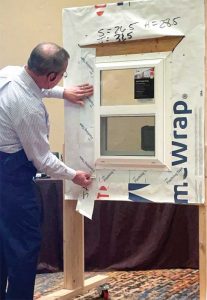
Throughout the testing process, any objectionable appearance such as wrinkling, distortion, blistering, delamination, expansion, shrinkage, or warpage of the self-adhering flashing facing material or adhesive layer must be noted.
Installation considerations
To ensure the flashing will perform as intended, it must be installed correctly. Proper installation is critical for performance and the flashing manufacturer’s installation guidelines should be carefully followed.
First, the flashing should be suitable for the regional climate, installation conditions, and expected long-term environmental exposure. Flashing installation should always follow the standard sequencing of components (commonly referred to as “shiplap” or “weatherboard fashion”) as addressed in ASTM E2112-23, Standard Practice for Installation of Exterior Windows, Doors and Skylights.
The flashing should extend a minimum of 50.8 mm (2 in.) beyond the critical interface and the minimum flashing width should be 76.2 mm (3 in.). This is based on using a window with an integral mounting flange as the baseline example incorporating a 25.4 mm (1 in.) mounting flange with a 50.8 mm (2 in.) minimum adhesion onto the wall substrate. In all cases, care must be taken to allow enough width for good adhesion and potential field installation errors.
To ensure adequate performance, the use of a clean, dry substrate surface is highly recommended. If the flashing comes in contact with different building surfaces (sheathing, WRB, concrete block, etc.), care must be taken to ensure full adhesion to all surfaces.
Installers should anticipate that temperature, moisture content, and surface cleanliness will impact adhesion. Further, certain types of sheathing materials present special challenges; therefore, the flashing manufacturer should be consulted for recommendations on adhering to specific substrates.
The following are important considerations for common sheathing/substrate types:
- OSB possesses a highly variable surface that is often not well bonded and, therefore, provides an inconsistent surface for adhesion. A primer is often needed to ensure adequate adhesion to OSB.
- Fiberglass-coated gypsum board contains a loosely bonded fiberglass mesh laminated to gypsum board. Due to delamination of the fibers, self-adhering flashing typically does not achieve adequate adhesion unless the mesh is adhesively bonded using a primer.
- Concrete block surfaces are irregular, coarse, porous, and often contain debris. Also, waterproofing coatings applied to the block can interfere with adhesion. Consequently, a primer is recommended unless otherwise specified.
- Metal substrates should be clean and dry with residual oily coatings removed to promote proper adhesion.