Specifying cold-formed steel to meet project goals
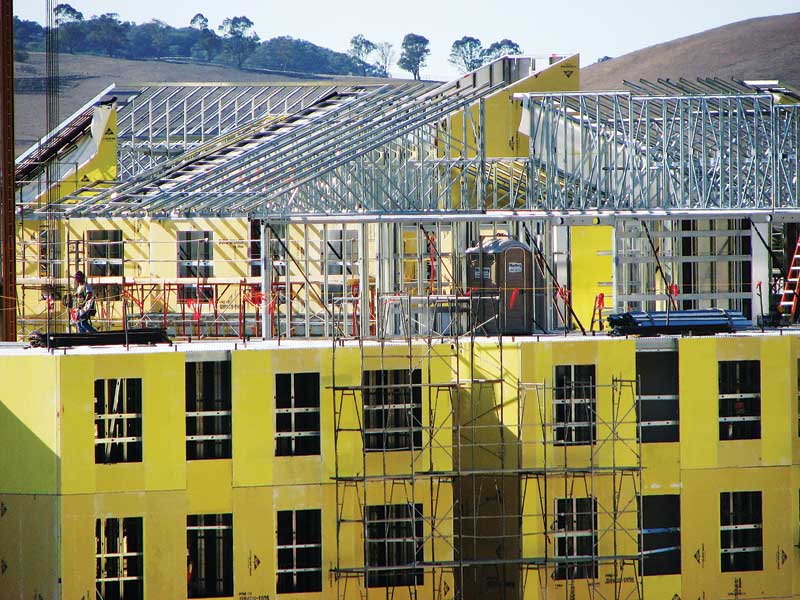
Photos © Don Allen
Building information modeling’s proper implementation
As the construction industry moves toward building information modeling (BIM) for project planning and management, building professionals are looking for products and materials that can be efficiently integrated into BIM. Since cold-formed steel panels and prefabricated components are typically created as computer models before they are manufactured, they make this process easy. Further, the material’s inherent uniformity allows building professionals to understand, with a great deal of accuracy, the attributes of cold-formed steel products and how those products will interact with other building systems.
Many manufacturers have developed BIM libraries incorporating attributes such as yield strength and load capacity into the model. Panel and component manufacturers have developed various framing methodologies that seamlessly dovetail into the building model, allowing layouts that consider the needs of other trades using the same wall, roof, and floor spaces both in the model and in the building. Given the experience level of most CFS component detailers, many systems for wall, roof, and floor assemblies have designed-in areas such as wall chases, large openings in floor joists, and header configurations that allow room for other systems such as HVAC, electrical, plumbing, and sprinklers. This leads to less time spent during the clash-detection phases of building modeling, and more on optimizing the materials and systems.
Specifying for current standards
When using cold-formed steel products, specifiers need to ensure they work within the most up-to-date specifications for all applications. If professionals employ past projects to inform current decisions, they run the risk of including cold-formed steel standards no longer referenced in the latest building codes.
Outdated standards such as ASTM A525, Specification for General Requirements for Steel Sheet, Zinc-coated (Galvanized) by the Hot-dip Process, or ASTM A446, Specification for Steel Sheet, Zinc-coated (Galvanized) by the Hot-dip Process, Structural (Physical) Quality, should be avoided. Instead, specifiers should reference ASTM A1003/A1003M, Standard Specification for Steel Sheet, Carbon, Metallic- and Nonmetallic-coated for Cold-formed Framing Members, and ASTM A653/A653M, Standard Specification for Steel Sheet, Zinc-coated (Galvanized) or Zinc-iron Alloy-coated (Galveannealed) by the Hot-dip Process. Guidance on the proper referencing of these ASTM standards is in Cold-formed Steel Engineers Institute (CFSEI) Technical Notes G800-12 and G801-13.

Durability and sustainability
In structural applications, the minimum galvanized coating required for steel is Z180 (i.e. G60, or 180 g of zinc per m2 of steel [0.6 oz per sf]). In framing applications, industry studies have shown coatings used for steel are predicted to last for more than 100 years. (A report on one such study can be viewed online at www.steelframing.org/PDF/durability/durability2011-singlepgs-final.pdf.) Applications where there are concerns about moisture wetting the wall or floor cavity, or more corrosive environments such as the windward shore in coastal areas, call for heavier coatings such as Z175 (G90 or CP-90). Technical notes on corrosion protection for fasteners and cold-formed steel framing in both coastal and more temperate climates are available from CFSEI. (Technical notes are available free to CFSEI members, or for purchase, at www.cfsei.org.)
As the significant impact that buildings and their construction have on the environment becomes clearer, consumers, businesses, and building owners around the world have mandated more sustainable and efficient products and systems from the construction industry. To meet this demand, the North American steel industry has made significant progress in increasing the efficiency and lessening the environmental impact of steel production over the years. With cold-formed steel, designers can develop more creative buildings while using less material. The increased strength, durability, and resilience of this material give architects and engineers the freedom to create structures that use fewer resources and have less environmental impact while maintaining building integrity. The versatility of CFS systems allows for a wide variety of shapes and configurations, including curved and flowing walls, ceilings, and roofs.
Steel’s complete recyclability also allows steel construction products and systems to be sustainably managed at the end of a building’s life cycle. Steel construction products contain between 25 and 100 percent recycled content, and are fully recyclable at end of life. Where materials such as wood or plastics are often disposed of in landfills or downcycled for fuel or mulch, cold-formed steel in buildings can be collected and recycled as another steel construction product or any of a range of other products. Specifiers should require a minimum recycled content of 25 percent for steel framing products and accessories to help achieve overall building recycled content targets.
Project teams pursuing certification in green building rating systems like the U.S. Green Building Council’s (USGBC’s) Leadership in Energy and Environmental Design (LEED) find additional benefits in using cold-formed steel. In the latest edition, LEED v4, building material credits are available in areas including life cycle assessment (LCA), environmental product declarations (EPDs), and improved product transparency. Steel-intensive building designs can be significant contributors to earning points in these categories because of the availability of data on supply chain, raw materials, and energy use for all steel products. (Industry-wide EPDs are available for cold-formed steel studs, track, and other cold-formed steel products at www.buildusingsteel.org/why-choose-steel/product-transparency.aspx.) Several individual manufacturers have developed product-specific EPDs for improved product transparency.