The need for coordination in residential high-rise construction
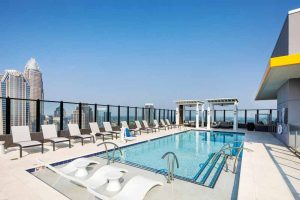
This is where collaboration, coordination, and creativity showed themselves in full strength. The team needed to use as much of the roof area as possible without compromising the rooftop pool deck, other outdoor amenities, and the iconic views this building offered. The challenges were not only the line set length of 33 stories, but also a lack of roof space that could accommodate condensing units for the upper half of the building.
Fitting the mechanical equipment
A structure of this height typically means a small footprint, high unit count, and limited space for mechanical units. There are many cases where an intermediate floor would be allocated solely for condensing units, as that would provide the additional square footage, easy maintenance access, and reach the portion of the building location the roof cannot accommodate. The downside is the potential for wasted net square footage that could provide future income.
Fortunately, in this project, the design team was able to take advantage of an adjacent eight-story pre-cast garage that services both the 33-story tower and the adjacent mid-rise building. An additional level was added to the garage to house most of the heat pumps and two large emergency generators. This added enough space for the condensers, but left the issue of line set length. In the end, for all the mechanical equipment to fit within the space available, and provide the necessary reach, variable refrigerant volumes (VRVs)—which are multi-split air conditioner system for commercial buildings—had to be installed in tandem with the split system heat pumps.
Structural engineering for a high-rise
Designing dwelling units is one of the early stages of design, which can have later ramifications, if done in a vacuum. During schematic design, the goal is to design and develop units that provide residents with an efficient, functional space, which they can also rent within the current market price. At this stage, the focus is not typically on structural elements.
Structural engineering is not yet engaged with the drawings and would usually around the design. This is fine for a wood-framed building, where the structural walls create the spaces within the units, but in a high-rise, the structural engineer needs to be involved early. The structural engineer needs to review, analyze, and confirm the column placement, and provide feedback on the sizes and general column grid. Columns within a concrete tower will heavily affect the layout of a residential dwelling unit, and not coordinating their locations simultaneously with the space planning of the units can be a hurdle.
Column coordination in The Vermeer
The Vermeer is a great example of the cascading effect of column coordination throughout a building. This particular project houses multiple uses within, multiple levels within each use, and every use has a different requirement when it comes to the spacing of columns.
The residential units need the columns to occur at the demising walls. Retail is best suited by columns in a perfectly square grid, spaced as far apart as possible, without touching the exterior storefront. The parking is best served by a perfect grid as well, but that grid is going to be different than retail’s ideal grid and, as an added complication, the site is not perfectly square. When these conditions in mind, sloping that one column near the closet entry door in unit plan A is no longer the biggest challenge.