Understanding the emerging acidic condensate issue
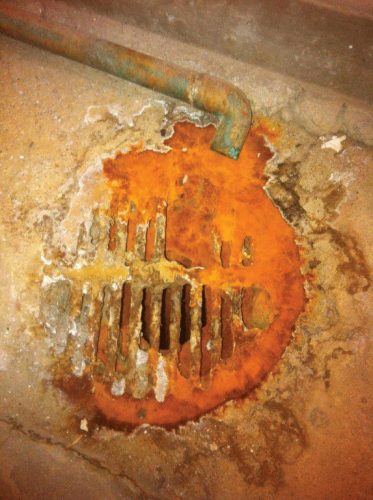
Today’s high-efficiency, gas-fired heating appliances (e.g. boilers, furnaces, and water heaters) offer a variety of critical benefits, from reducing a building’s energy consumption to minimizing its environmental footprint. These types of condensing appliances are well-suited for most new construction and retrofit installations.
Key factors driving the adoption of high-efficiency appliances include new regulatory mandates. In late 2023, the Department of Energy (DOE) established a standard for residential gas furnace efficiency, set to take effect in late 2028. This rule mandates that non-weatherized gas furnaces and those in mobile homes achieve an annual fuel utilization efficiency of at least 95 percent. To comply, gas furnaces will need to utilize condensing technology, which uses a secondary heat exchanger to recover combustion gases and capture more heat. The DOE states this standard is “readily achievable by modern condensing furnaces.”
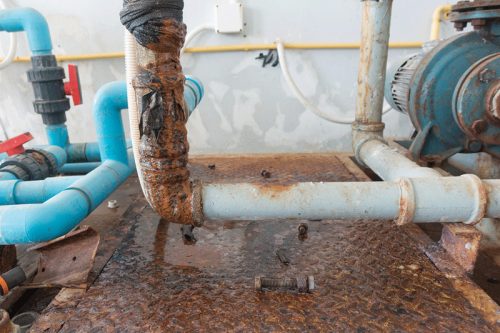
Despite their reputation as a game-changing innovation, high-efficiency, gas-fired heating appliances produce acidic condensate (pH 2.9-4.0). If discharged without being properly treated, this acidic residue can corrode plumbing, concrete foundations, floor drains, septic systems, and other wastewater infrastructure. It can also potentially contaminate groundwater and the environment.
A typical residential, high-efficiency gas-fired heating appliance produces about 7.6 L (2 gal) of acidic condensate per hour, leading to an estimated 39.6 billion L (9 billion gal) annually across the U.S. This poses significant risks to properties and the environment. The solution is straightforward: install condensate neutralizers with every high-efficiency gas-fired heating appliance.
Condensate neutralizers are specialized filtration devices that connect to appliances and contain a neutralizing media like magnesium hydroxide to treat acidic condensate. The acidic condensate drains from the appliance and is piped to the gravity-fed neutralizer, where it interacts with the media, raising the pH between five and 9.5. This process neutralizes the condensate, rendering it safe to be discharged into the building’s plumbing and wastewater system. These devices are essential for preventing damage from acidic condensate.
A properly installed condensate neutralizer can effectively function in high-efficiency systems for years if routinely inspected and its neutralizing media regularly replaced. Maintenance is crucial; neglecting it is akin to not having a neutralizer at all. Factors like condensate acidity and volume affect media longevity. Service technicians should regularly test the pH of the treated condensate to ensure adequate treatment. The service technician should replace the media if the pH drops below five (or the minimum level per the local authority). Generally, the media should be replaced at least every 12 months. Incorporating this service into a preventative maintenance program for gas-fired, high-efficiency appliances is recommended.
Ultimately, condensate neutralizers are a must-have accessory for every condensing installation in a building or home to ensure the gas-fired heating appliance operates safely, achieves code compliance, and fulfills its environmental promise.
Author
Kyle Emmons is the president of JJM Alkaline Technologies, which designs and manufactures condensate neutralizers for the heating and plumbing industries. He focuses on sales, marketing, and product development. Emmons holds a bachelor of business administration in finance from Texas Christian University and an MBA from the Kellogg School of Management at Northwestern University.
The opinions expressed in Failures are based on the authors’ experiences and do not necessarily reflect that of The Construction Specifier or CSI.