When Wetter May Be Wiser: Designing for resilience in areas subject to flooding
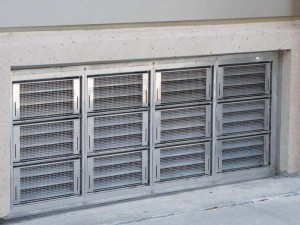
Dry floodproofing
Among considerations in deciding between dry and wet floodproofing is the limitation of how much additional hydrostatic pressure will be exerted against the structure’s walls, being the load of floodwaters as mentioned in IBC. Dry floodproofing is limited by what the structure can bear; formulas are supplied by FEMA in Technical Bulletin 3 for lateral hydrostatic forces, buoyancy, hydrodynamic forces, and debris impact.
Dry floodproofing requires extensive emergency operation planning, some of which is related to site selection. Areas subject to rapidly rising high velocity floodwaters do not allow adequate evacuation warning time. As some dry floodproofing approaches include placing solid barriers over doors and windows, advance disaster planning is crucial to ensure all individuals are out before sealing and locking those barriers. Flooding may obstruct access to implement active dry floodproofing measures requiring manpower to install, while putting those individuals at risk.
Engineering considerations for dry floodproofing include a regular inspection and maintenance plan to ensure all components operate properly under all conditions, including power failure. At least annually, one should inspect and test mechanical equipment, generators, and flood shields (including gaskets), and inspect and repair foundation walls (ensuring no cracks), levees, and berms.
Along with U.S. Army Corps of Engineers (USACE) EP 1165-2-314, Floodproofing Regulations, Section 1.1 of ASCE 24 addresses dry floodproofing as a method to render a structure “substantially impermeable,” resulting in:
a space free of through cracks, openings, or other channels that permit unobstructed passage of water and seepage during flooding, and which resulting in a maximum accumulation of 4 in. [i.e. 102 mm] of water depth in such space during a period of 24 hours.
This obviously requires substantial attention to choice of materials, construction technique, and testing to meet the stated standard. A floodproofing certificate for non-residential structures (Office of Management and Budget [OMB] No. 1660-0008) must be signed and sealed by a properly licensed design professional certifying to having developed and/or reviewed the floodproofing design plans and specifications (not the as-built conditions), and that they comply with accepted standards of practice for dry floodproofing.
For flood insurance premiums to reflect the additional protection and lower risk, dry floodproofing must extend 0.3 m (1 ft) above BFE (that is, one foot of freeboard). However, the resultant hydrostatic pressure from more than 0.9 m (3 ft) of dry floodproofing is likely to overwhelm most structures’ ability to withstand such forces without extreme design and engineering measures. Dry floodproofing exceeding 0.9 m in height therefore represents an increased risk of flood damages that may result in higher flood insurance rates.
While they help with water seepage, sump pumps cannot be relied upon as a means of dry floodproofing, although they are required to help drain a flooded structure. Sites that flood frequently also may be inappropriate candidates for dry floodproofing, due to cumulative wear and tear on external building components.
Wet floodproofing
Wet floodproofing, also known as flood-venting, requires automatic entry and exit of floodwaters during one-percent annual chance flood events. This technique may be employed without a variance in fully enclosed areas below a structure’s lowest floor when those enclosed areas are used solely for parking, building access, or limited storage. Such construction must employ flood-resistant materials, as must any facilities in these locations. For the best protection and lower insurance rating, mechanical and electrical systems, heating and ventilation equipment, and liquid storage containers should be located above BFE, which can entail placement on platforms or suspension from the enclosed area’s ceiling.
In contrast to dry floodproofing, wet floodproofing is considered a passive approach because it involves no human intervention to be activated—flood vents must open automatically to relieve hydrostatic pressure on the walls of the enclosure as flooding occurs. While safety and evacuation planning are still necessary, no one must stay behind to ensure building protection.
William L. Coulbourne, PE, M.ASCE, (Coulbourne Consulting) is one of the primary authors of FEMA 55, Coastal Construction Manual, and a member of various ASCE standards committees. He indicates there may be a cost benefit to engineered wet floodproofing instead of dry floodproofing to accommodate the physical forces of water. His evaluation of two wet- and two dry-floodproofed scenarios indicates costs of thickening and reinforcing walls and foundations in addition to anchors, waterproofing materials, and other dry proofing methods could in some situations exceed twice the cost of installing manufactured engineered flood vents that allow automatic equalization of exterior and interior hydrostatic pressures on building walls. While there is additional cost in post-event cleanup, there is also increased likelihood of structural integrity being maintained through the flood.
Development always has some impact on the floodplain—increased flood depths, velocities and flows, and horizontal extent. While not eliminating it, wet floodproofing creates less hydraulic disturbance than dry floodproofing. Water entering a structure reduces some obstruction to flow, minimizing some of the structure’s impact on the floodplain. This good-neighbor policy manifests some of the “No Adverse Impact” principles promoted by the Association of State Flood Plain Managers (ASFPM). As we continue to build out our environment, stewardship and sustainability demand we view the cumulative effects on the watershed as a whole rather than focus only on the site where we are working.
Proper implementation of wet floodproofing
44 CFR 60.3(c)(3) requires enclosures below BFE in A-type zones must either be dry floodproofed or designed to allow for the equalization of hydrostatic pressures during a flood event—wet floodproofing. 44 CFR 60.3(c)(5) defines appropriate implementation of this wet floodproofing, and mandates specifications for building areas subject to flooding located below the lowest floor of a structure (other than basements) that are used only for vehicular parking, building access, or storage. The minimum design criteria for this category of new and substantial improvements are:
A minimum of two openings having a total net area of not less than one square inch for every square foot of enclosed area subject to flooding is provided. The bottom of all openings shall be no higher than one foot above grade. Openings may be equipped with screens, louvers, valves, or other coverings or devices provided that they permit the automatic entry and exit of floodwaters. [emphasis added]
Basements (i.e. areas below grade on all sides) are permitted in non-residential structures in the SFHA only when designed and certified to be dry floodproofed; in other words, wet floodproofing is inappropriate for these areas. Crawlspaces that are subgrade on all sides are insured as basements (higher rates), but regulated as crawlspaces (For more information, see FEMA Technical Bulletin 11, Crawlspace Construction for Buildings Located in Special Flood Hazard Areas).
Section 6.3 of ASCE 24 elaborates on 44 CFR 60.3(c)(5), while reiterating the purpose of wet floodproofing is to minimize damage to the structure. Section 6.3 limits use of this technique to:
- enclosures used solely for parking of vehicles (below elevated buildings), storage (low value items), or building access (stairwells, elevators);
- structures that are functionally dependent on proximity to water (such as marinas); and
- certain agricultural, temporary, or minor storage facilities that “represent a low hazard to human life in the event of failure.”