A Blindside Waterproofing Primer: Factors to consider when selecting the correct membrane
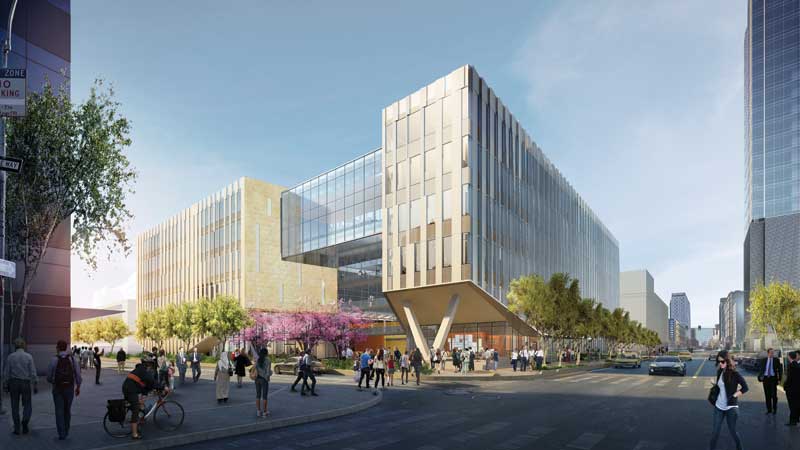
by Wendy Talarico, LEED AP
The primary purpose of below-grade waterproofing is not to keep water out of the basement, although that is an important consideration. Rather, its role is to protect the foundation and the entire building structure from the damaging effects of liquids and vapors.
In his classic book, The Manual of Below-Grade Waterproofing Systems—published by John Wiley & Sons in 1999—Justin Henshell, FAIA, lists criteria for selecting the right waterproofing for the job. These include:
- the nature of the soil;
- hydrostatic pressure;
- the location of the water table;
- substrate stability;
- building occupancy; and
- the construction method to be used.
One more criteria can be added to that list: access. On most new construction projects where there is plenty of land, a site is excavated, the foundation is poured, and traditional waterproofing is applied to the outside of the foundation wall. There is maneuvering room for heavy equipment and space for staging building materials. However, this is not always possible where space is limited or where sites are hemmed in by other buildings, infrastructure, or tight lot lines. The solution in many of these circumstances is blindside waterproofing. (Blindside is a positive-side application—meaning it goes on the outside or the soil side of the foundation wall. Negative side waterproofing is on the inside of the wall).
Blindside, sometimes called pre-applied, is a term used to define the membrane type as well as the installation process. It reverses the typical application—the waterproofing is installed before the foundation is poured. The membrane is applied to the soil support (i.e. shoring, sheet pile, slurry wall, rock, or the structure of the neighboring building) and then concrete or shotcrete is applied against the membrane. In short, the concrete is applied to the waterproofing. Attachment to the soil support system is temporary. The real goal of blindside is to adhere to the concrete.
Various pre-applied applications have been around since the advent of the zero lot line in urban settings. Around 1900, brick and stone foundations were typically waterproofed—usually parged—with bituminous materials. Concrete was a rare material at that time, but had already started to make its way into the foundation wall.
According to Kidder Parker Architects’ and Builders’ Handbook, the first blindside membranes were “multiple layers of burlap or felt swabbed with hot pitch or asphalt…applied over the [drainage] tile and covered with bricks.” Foundation walls were then erected against this system.
As buildings moved toward concrete foundations that incorporated more steel, keeping moisture out became a priority. This is even more important now as foundations go deeper and more purposes are assigned to these below-grade spaces.

Photos courtesy W.R. Meadows
Within the past 50 years, soil retention systems have become more sophisticated, thanks to better:
- technology;
- construction techniques;
- soil nailing and anchoring; and
- excavation supports.
The geotechnical engineer may work hand-in-hand with the structural engineer and the architect to create a foundation as complex as any other building systems.
The most typical use for below grade space is likely the parking garage, though there is no official statistical data on the subject. Hospitality projects, for example, employ underground square footage for exercise rooms, information technology (IT), record storage, conference rooms, and even ‘wine cellar’ restaurants. Medical projects may use this space imaging equipment in order to help shield radiation and minimize vibration.
Another reason some are designing deeper foundations is to increase the allowable glass above. Updates to the International Energy Conservation Code (IECC) are limiting the amount of permissible glass on buildings. The 2015 code calls for a 30 to 40 percent window to wall ratio. The easiest way for a designer to meet this requirement while maximizing the amount of permissible glass, is to follow the American Society of Heating, Refrigeration, and Air Conditioning Engineers (ASHRAE) 90.1, Energy Standard for Buildings Except Low-rise Residential Buildings. This standard allows the architects to factor in all the building wall surface areas, including those located below-grade, when calculating the window-to-wall ratio.