By Tim Cullen and Tom Bagsarian
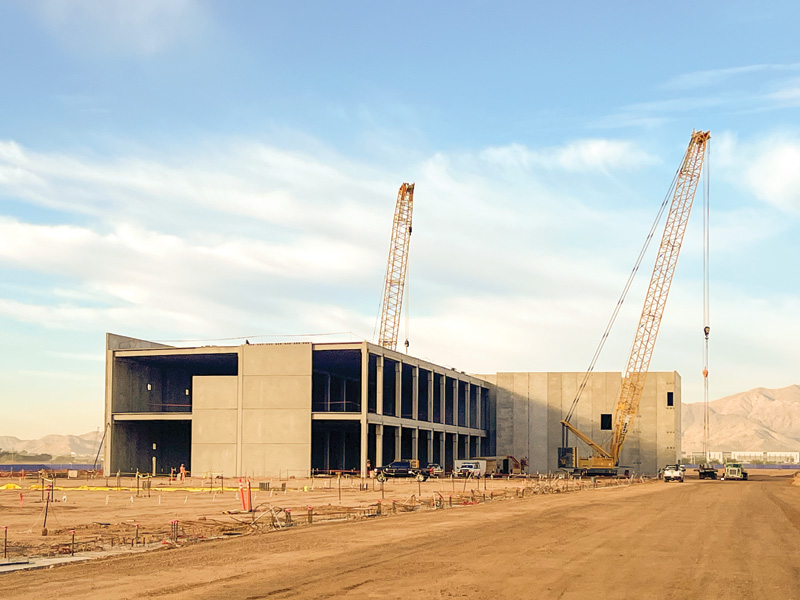
Much attention has turned to data center construction, not only in the United States, but throughout the world, as technology companies strive to find facilities to house the infrastructure needed as artificial intelligence (AI) becomes more prevalent. Precast concrete is a desirable material for these buildings for a variety of reasons, whether used for walls, floors, and roof panels in a total precast structure or as an enclosure system. Regardless of the application, precast offers the same off-site construction benefits.
While data centers are currently being constructed at a fast pace, they are not a new building type. The most basic computer data storage facilities date back to World War II. The computer boom of the 1980s resulted in the need for more storage facilities and the term “data center” first came into use. Then came the dot-com bubble of the late 1990s, followed by the introduction of mobile devices in the 2010s.
However, for the data center market, these developments pale compared to the advent of artificial intelligence (AI), which requires more storage than many ever imagined. Goldman Sach found that one ChatGPT query needs 10 times as much electricity as a Google search.
The question now is how to build these facilities to meet the surging demand for data centers AI has created. A McKinsey & Company report forecasts 10 percent annual data center growth until 2030; some believe this is conservative. A representative for Microsoft said at the National Institute of Building Sciences (NIBS) Building Innovation Conference in May 2024 that his company alone operates 150 data centers worldwide.
“Things are not slowing down,” says Roksana (Roxy) Taghizadeh, associate principal with AG&E, a structural engineering firm based in Dallas, Tex., and the engineer of record for 50 to 80 data centers a year. “There is huge demand for us to churn these out as quickly as possible to meet expedited construction schedules.”
Precast concrete is an ideal material for the construction of buildings that will meet the aggressive schedules important for data center owners.
“Since precast concrete components are manufactured offsite, they can be procured and fabricated prior to the site being disturbed, and the precast can be scheduled to be erected at a specific time once the foundations are in place,” says Corey Greika, vice president/general manager of Coreslab Structures in Indianapolis.
“Once precast concrete erection begins, it is an extremely fast process, especially when you consider that insulated precast concrete wall panels have all the elements of a finished wall system (finished surface, air, and vapor barrier) built in. This predictability and speed are critical to the success of the project from the owners’ perspective.”
Many precast concrete producers have also installed new production lines to increase their capacity and speed to manufacture data center components.
“Precast concrete producers can also use multiple manufacturing facilities to help meet schedules,” Greika adds. “Most data center owners procure their precast concrete well in advance, which helps keep a project on schedule and avoids construction delays.”
Michael Lyons, vice president and mission-critical practice leaker at architecture firm HKS, stresses data center clients should collaborate early with precast concrete producers.
“Early collaboration allows us to integrate precast concrete solutions seamlessly during the design phase, enabling the fabrication of precast concrete panels concurrently with site preparation,” Lyons says. He explains that precast concrete means fewer trades will be at the jobsite, streamlining construction and minimizing delays.
Over the last decade, average rack power densities have nearly quintupled to 10 kW, and self-weight has doubled to about 1,814 kg (4,000 lb). In five years, the average power densities are expected to quintuple again to about 50 kW per rack, with weights potentially doubling.
EnCon Design, LLC, a division of EnCon United Company, has seen suspended loads exponentially doubling and roof live loads tripling from 2010 to 2024. While the exact source of these increased loads is not always directly disclosed, many precast concrete producers committed to this market segment have invested in deep-stem double-tees to accommodate these loads. Nearly standardized, this section is 4-m (12-ft) wide and 12-m (40-ft) deep.
Precast concrete is highly versatile, making it well-suited for various construction applications. Its ability to support long, clear spans is valuable for organizing various rack layouts with minimal disruption. As floor-to-floor heights rise to approximately 9 m (30 ft) to accommodate additional electrical and low-voltage connections, precast concrete proves to be an excellent choice.
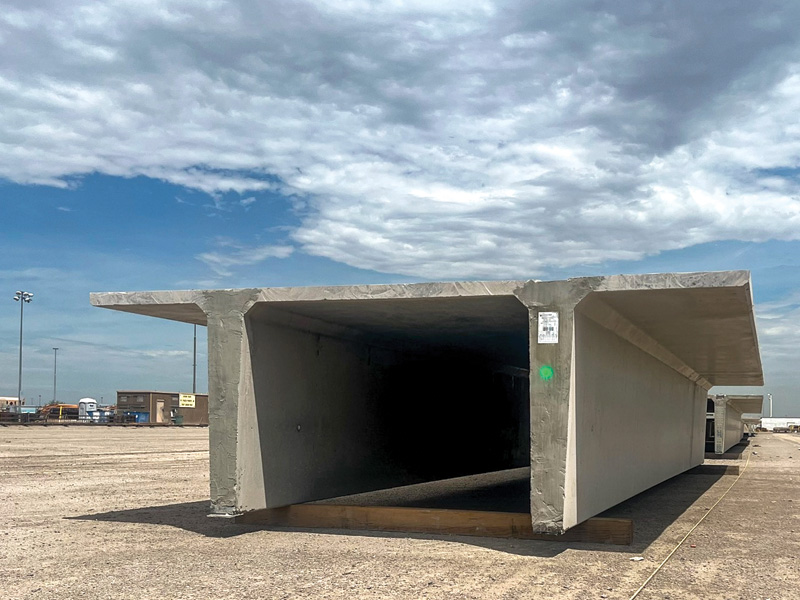
Total precast solution
Jason Lien, executive vice president at EnCon United Company, notes data center designs are moving from sprawling single-story warehouses toward compact multistory buildings. This is likely due to efforts to conserve resources such as fiber optical cable and/or issues with latency between AI servers. At these increased heights, total precast concrete structures become even more attractive in terms of cost savings and impact on delivery. A total precast structure uses precast, prestressed concrete for the core and shell above grade. It may or may not have topping for the floor/roof. Precast concrete’s inherent vibration absorption, quick shell enclosure, dedicated safe work regions, and total precast structure condense the functional ROI schedule while maintaining structural integrity.
Precast concrete’s inherent two- or three-hour fire rating, temperature regulation through concrete mass and insulated wall panel construction, and strength, may result in a reduction in overall materials used—such as the number of columns required or volume of composite topping for the floors and roof. These reductions lower embodied carbon and require fewer labor hours onsite, lowering insurance requirements.
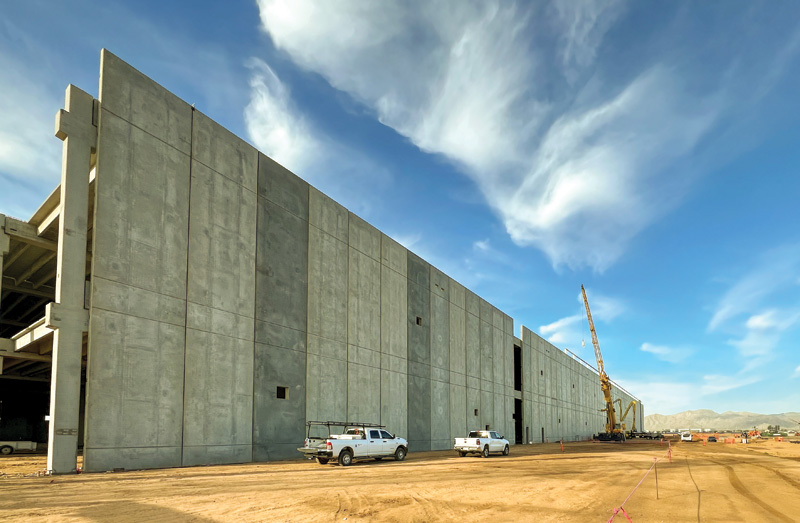

Precast, prestressed concrete finishes have schedule, cost, and design advantages. Using precast means moving the finish from the field to the plant, which saves time and requires less labor at the job site. Precast’s integrated finishes require less long-term maintenance, resulting in lower long-term cost in dollars and carbon. Precast can match a broad range of architectural styles, shapes, sizes, and colors. Formliners and molds give precast practically unlimited and extraordinary design potential.
Numerous precast concrete suppliers exist, resulting in steady pricing and predictable delivery. While site challenges can result in uneven product quality using materials, precast concrete manufacturing happens with the same molds, crew, and location.
Precast/Prestressed Concrete Institute (PCI) certification and producers’ quality assurance and quality control ensure precision is beyond industry standards. Precast concrete producers are certified by PCI to manufacture and deliver specific products. The quality staff is certified to inspect products and hardware before concrete is placed in the form and certified to evaluate the product after the product is removed from the form. Concrete is sampled and tested at regular increments by a certified technician. The raw materials that flow into the plant are monitored and evaluated for compatibility and specification compliance with mill certification review. Historical information on casting and raw materials can be requested to ensure material sourcing and fabrication transparency.
A PCI-certified producer or subcontractor performs product installation. This assurance ensures details and connections are installed according to plans and specifications. Proper product handling and rigging ensure field staff safety and general product performance. Lastly, the team is working on an engineered installation plan developed based on staged loading and unloading, which is often found during construction.
When one considers all the many challenges facing the data center industry today, coupled with the ever-increasing demands precipitated by AI development, total precast structures stand out as a solution. Precast concrete building systems offer value and budget certainty, whether the accelerated schedule advantage yields faster ROIs, vibration control eliminates redundant interior framing, or the high thermal efficiency inherent within insulated precast walls.
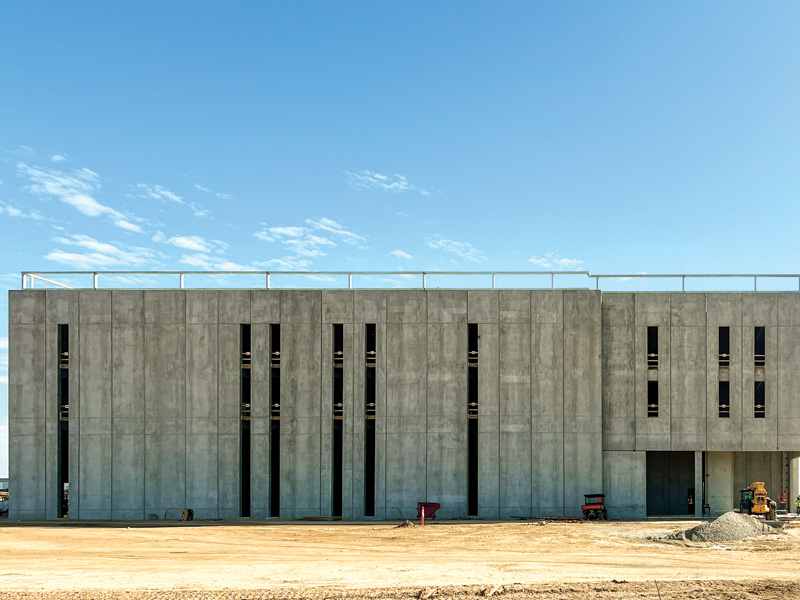
Sustainability advantages
In addition to greater cost advantages and reliability, precast concrete provides data center owners and developers with lower embodied carbon, improved resiliency, and better safety. “Data center owners and developers are driving hard to reduce the embodied carbon in their data centers,” says Allan Bedwell, chief sustainability officer at Clark Pacific, a precast concrete producer based in West Sacramento, Calif.
Precast concrete structures are ideal for adaptive reuse by providing longer spans with larger open spaces and fewer interior columns. This allows for easy building renovation as future occupancy needs change. Precast concrete construction also benefits from the pre-dominant use of bonded prestress strand reinforcement as compared to un-bonded which is typical in cast-in-place concrete structures. A bonded strand can often be cut, knowing it will still provide reinforcement benefits in other areas. Prestress concrete stemmed floor systems have the benefit of the bonded prestressing strand being concentrated in the lower two-thirds of the stems. This design allows for a lot of flexibility for future floor openings. Many precast concrete wall panel systems are designed and reinforced for future openings, even providing reveals to show where future cuts can be made.
Bedwell’s company focuses on concrete mixes that use less cement and optimizes designs to minimize the quantity of concrete and steel in data centers and reduce embodied carbon. Clark Pacific will soon release its ASTM-verified environmental product disclosure (EPD) for a data center and third-party lifecycle analysis (LCA) that compares the total carbon emissions of a precast concrete data center to a steel data center.
The new three-story 65,032-m2 (700,000-sf) total precast concrete data center in the Phoenix, Ariz., metropolitan area recently received the U.S. Resiliency Council’s first Platinum Seismic Rating and Platinum Wind Rating.
“These platinum ratings indicate that the data center has the highest level of building performance and is expected to suffer negligible damage and repair cost, with a functional recovery time within a few days following a major seismic or wind event,” says Bedwell.
“The benefit of utilizing precast concrete is its inherent strength and durability to withstand the loads from heavy equipment,” says AG&E’s Taghizadeh. “The hardened shell with its typically windowless exterior walls are ready-made to withstand all manner of weather and fire.”
PCI forms data center task group
For decades, parking structures have been the focal structure type for the precast concrete industry. However, recent trends indicate a significant interest and expansion of data centers constructed using precast concrete.
Precast concrete structural and envelope systems meet the high-performance demands of data centers by providing cost-effective open spans, passive fire resistance, and durable, high-efficiency, low-maintenance building envelopes. This is very important to mission-critical facilities—which data centers often are. Precast concrete is a high-performance material that integrates easily with other systems and inherently provides the versatility, efficiency, and resiliency needed to meet the multi-hazard requirements and long-term demands of high-performance structures.
To support this growing market, the PCI Technical Activities Council has formed a Data Center task group with the support of the PCI Marketing Council. The task group’s mission is to develop recommended practices for using precast concrete in data centers, organize the body of knowledge for total–precast concrete and precast concrete–clad data centers, and provide recommendations for integrating precast concrete with other trade requirements.
The Data Center task group is developing a new PCI document titled “Precast Concrete Data Centers: Recommended Practice for Design and Construction.” This document will guide designers in addressing the unique challenges of data center design and demonstrate to developers and architects the benefits of using precast concrete for data center construction.
Precast concrete is the ideal construction material for data centers for many reasons. It is reliable and long-lasting, stands up to these buildings’ increased loads, and does not have unpredictable pricing often associated with other building materials. Certification and quality assurance ensure the precision of the product, all to the benefit of building owners.
Authors
Tim Cullen is the PCI director of technical activities. He has more than 17 years of experience in designing, detailing, constructing, maintaining, and renovating precast and prestressed concrete structures. Before joining PCI in 2022, he was vice president of Blue Ridge Design, a structural engineering firm, and previously a design engineer with High Concrete Group.
Tom Bagsarian, PCI editorial content manager. He has more than 25 years of experience writing about construction, and was managing editor of Concrete Construction and The Concrete Producer magazines. He has been with PCI for seven years.
Key Takeaways
As artificial intelligence (AI) fuels rapid growth in data center construction, precast concrete is emerging as a preferred building material due to its speed, durability, and sustainability. With off-site manufacturing, predictable quality, and accelerated installation, precast solutions help meet the surging demand while reducing project timelines and costs. Total precast structures provide fire resistance, vibration control, and high structural integrity, making them ideal for the evolving needs of AI-driven facilities. Additionally, precast concrete lowers embodied carbon, enhances resilience against seismic and wind events, and offers long-term adaptability, ensuring data centers remain efficient and future-proofed.