A Blindside Waterproofing Primer: Factors to consider when selecting the correct membrane

Challenges ahead
Blindside projects take planning and forethought. Things quickly get complex because applying and detailing waterproofing ahead of the foundation pour is a matter of anticipating problems and weak spots.
However, this approach also means sites with little access—often valuable urban infill locations—can be made usable. It is ideal for:
- buildings on office, medical, or college campuses;
- tunnels and other transportation venues;
- pits; and
- additions to existing buildings where access is blocked by parking garages, roads, or other infrastructure.
Pre-applied can be used throughout, forming a ‘bathtub’ encasing the entire foundation in waterproof material. This means water and, in most cases, vapor from beneath the foundation is also controlled, which can be significant to the building’s health and longevity.
However, many jobs use blindside along one or two walls and then combine with vapor retarders at the slab or to conventional waterproofing along walls with greater access. Blindside can also be used for renovation projects. How it is used depends on site conditions and regional practices. In the Southwest, for example, the practice may be used on the walls, but a vapor retarder is considered adequate where the water table is low. (See “Using Blindside at the Arizona Center for Law and Society”).
Even where there is plenty of space, excavating large areas means disturbing the existing ecosystem more than necessary. Use of blindside waterproofing means less excavation and potential to benefit from Leadership in Energy and Environmental (LEED) credits for minimizing site disturbance. Even for projects not pursuing LEED, it may be a priority of the landholders to preserve plantings and animal habitats.
Alternatively, a site may be close to an old landfill, industrial waste area, or other source of contamination. Churning the soil in these areas may mean digging into hazardous chemical locations. The U.S. Environmental Protection Agency (EPA) estimates there are more than 450,000 brownfields in the country.
Waterproofing a true brownfield site is beyond the scope of this article, but it is not unusual to work at a site near a brownfield. In these cases, the geotechnical engineer will provide guidance—which may include steering the project away from excessive excavation and toward blindside methods.
Choosing a membrane
A blindside membrane must, first and foremost, adhere tightly to the concrete. Since it goes in early, it must also be tough enough to withstand foot and even truck traffic. While it relies upon the soil retention system to form a substrate for its application, the membrane must stay put once that system falls apart, sags, and reacts to the pressures of soil and water. This is a tall order.
There are many choices for membrane materials, but they fall into roughly two categories: bentonite and composites. These adhere to the concrete either mechanically or chemically, depending on the materials used.
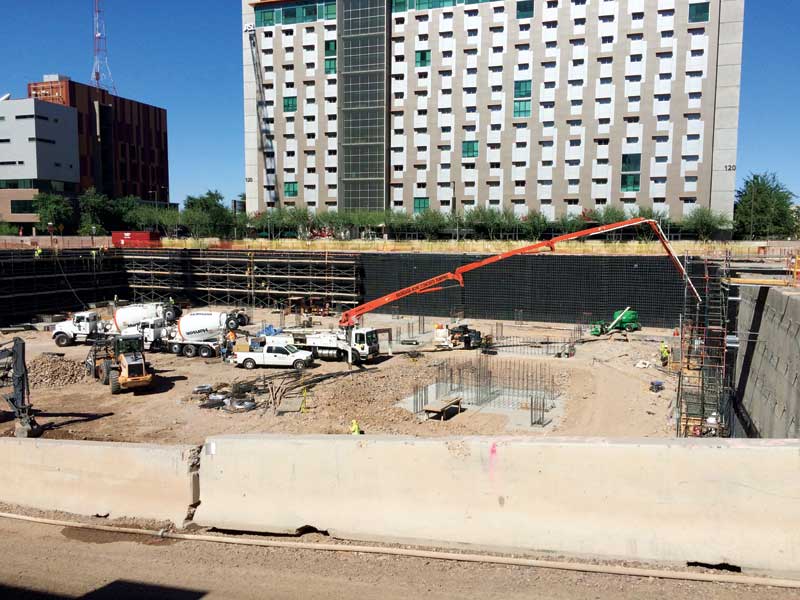
Bentonites
Bentonite is a group of clays that, when in contact with moisture, expand and seal to irregular surfaces, penetrations, cracks, and voids in concrete. It is a good choice for blindside applications due to its ability to repair itself, but it also has a tendency to migrate away from the foundation if there is enough water.
It is essential to keep bentonite confined and compressed against the foundation walls. In the past, installers relied on the soil retention system to accomplish this. However, these systems shift and degrade, so manufacturers are now placing the clay between multi-layered sheets of geotextiles or plastics to add tenacity and strength. These sheets may also function as vapor barriers, as bentonite alone is not effective in this regard.
Composites
Composites are proprietary mixtures that include layers of bituminous materials and/or plastics laminated for strength and durability. A common ingredient is polymer-modified asphalt. This is asphalt with performance-boosting additives, such as styrene-butadiene-styrene (SBS).
Some membranes incorporate high-density polyethylene (HDPE), polyvinyl chloride (PVC), butyl rubber, or thermoplastic polyolefin (TPO). Others include woven and non-woven geotextiles. Every manufacturer offers its own proprietary formula.
Membranes are tested based on a series of ASTM standards that include tests for resistance to hydrostatic head, elongation, tensile strength, and puncture resistance. Some manufacturers have modified the standard tests to create their own performance criteria. There is some debate over whether this is valid. Regardless, ASTM tests provide an unbiased platform for the evaluation of performance.
Testing is just part of the picture when it comes to evaluating a manufacturer and a membrane. The potential for problems is present regardless of which membrane is used. There is no single blindside product or brand right for every jobsite.