Bright ideas ahead: The skylight edge
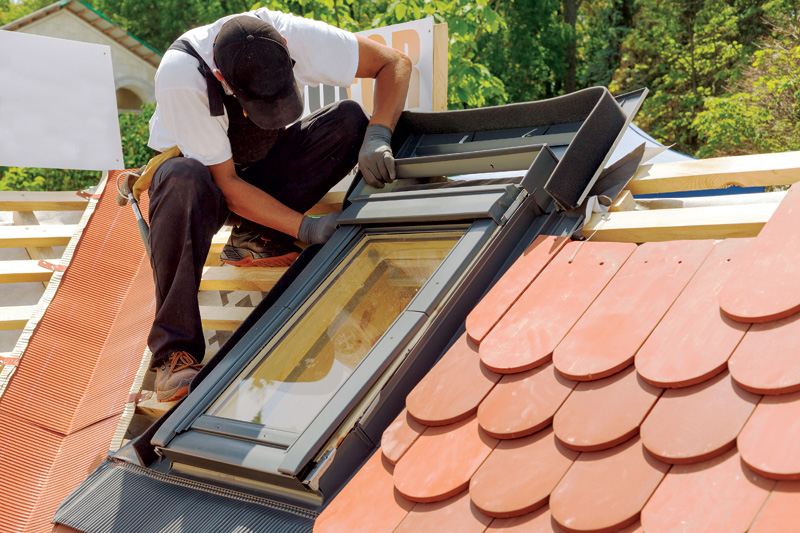
Skylights can be used to provide significant energy savings and enhance the aesthetic appeal of buildings, flooding interior spaces with the warmth and illumination of natural light. Well-designed skylights can take maximum advantage of solar heat gain co-efficient (SHGC) in winter to reduce energy consumption, as well as reduce lighting heat load on cooling systems in summer. These benefits make skylights a welcome addition to buildings.
Skylights may be specified in a variety of sizes and shapes to match nearly any building’s needs. They range from simple rectangles to complex polygons. They can be small to fit between rafters or large enough to run the length of a building. When selecting a skylight, the client’s needs must first be considered. Appearance, lighting requirements, energy performance, structural performance, ventilation capability, and egress requirements play a role in selecting the most appropriate type of skylight for a project. Unit skylights and tubular daylight devices (TDDs) are used for smaller rooms or to evenly distribute light over large open areas such as big box retail and warehouse spaces. Sloped glazing is typically associated with large, monumental applications and can provide an architectural feature as well as deliver natural lighting to a building.
The use of high-quality skylights, materials, and good installation practices will result in a sound, long-lasting, leak-proof installation. However, the very nature of a skylight—being a penetration through the roof—introduces a potential vulnerability: water leakage. Ensuring the long-term, leak-proof performance of a skylight relies heavily on rigorous testing protocols, which can be broadly categorized into laboratory testing conducted on the product itself and onsite (field) testing performed after installation.

Installation component considerations
Curbs, water diverts, ice breakers, sealants, fasteners, and other components are necessary for the proper installation of skylights.
Prefabricated and site-built curbs
A separate roof curb is sometimes used to raise the skylight above the roof deck surface to reduce a skylight’s exposure to water and snow on the roof deck, including ponding or standing water, and large volumes of water moving through the skylight location. The roof curb also provides a means of flashing the roof penetration created by a skylight by effectively integrating it with the roofing system. Roof curbs can also be used to modify the slope of the skylight relative to the roof.
Roof curbs are anchored to the roof deck or framing in a manner that ensures they can handle the design loads of the application. Constructed on the job site, roof curbs are typically made of wood. Prefabricated steel and aluminum roof curbs can also be used. Steep slope roofs generally warrant lower roof curbs. Low-slope and flat roofs sometimes require higher roof curbs as water levels on the roof surface increase. In all cases, the roof curb should fit the requirements of the application regarding proper height, materials, and anchoring.
Water diverters
In situations where a substantial volume of water will flow onto the skylight due to either a large, sloped roof area above the skylight’s location or contributing roof areas draining into and through that location, it would be beneficial to include a water diverter or cricket above the skylight to reduce the volume of water running into the head area of the skylight. These devices will ensure standing water does not accumulate on the roof, as it can degrade bonded roofing material joints over time.
Ice breakers
When the building is in an area that experiences heavy snowfall in winter, a high volume of snow can collect on the roof. In these situations, it is possible for ice and snow to break loose during milder temperatures and slide through the skylight. Ice breakers can help protect the skylight from the tremendous force a large ice slide typically generates. Metal roof applications are most susceptible to this force.
Sealants
Where required, the proper use of sealants plays an important part in skylight installations. Sealants need to meet performance requirements such as:
- They must not adversely react with or weaken the material they contact.
- They must have good long-term adhesion, so always follow manufacturer recommendations about surface preparation, cleaning procedures, and primers.
- They require corresponding service temperature performance in installations involving elevated temperatures.
- They must be capable of maintaining the required flexibility and integrity over time.
- They must have the correct bead size and adhere to other application details to ensure a well-performing joint.
Fastening and anchoring
The following considerations should be taken into account for fasteners or anchoring devices:
- Use anchors intended for the substrate involved.
- Select the type and size of anchor in sufficient quantity and spacing to meet the structural requirements (i.e. wind loads, snow loads, etc.).
- Choose corrosion-resistant fasteners.
- Be aware of instances where fasteners may react chemically with materials they contact (e.g. galvanic action between metals and coatings or anti-corrosion treatments)
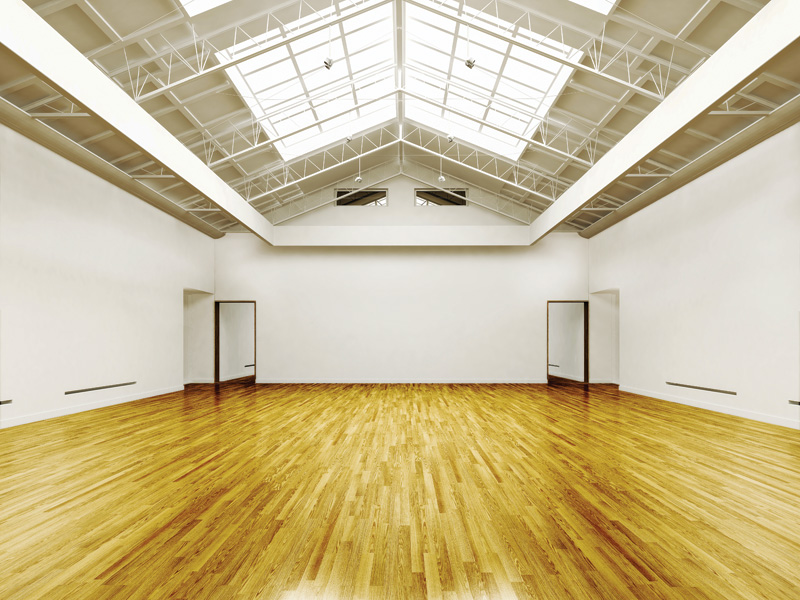
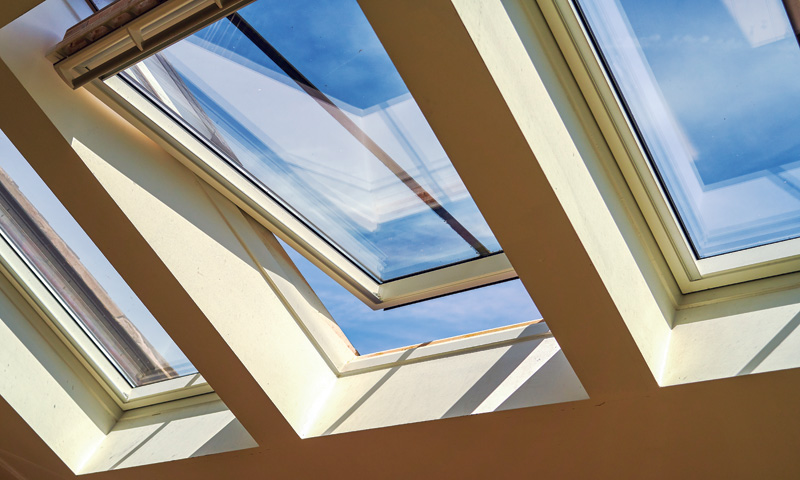
Installation best practices
The installation location of skylights must be properly sized, level, and square. If a site-built curb is used, it should be level and square. In all cases, the roof deck, support framing, and curb must be structurally adequate for anchoring the skylight and to withstand load reactions from the skylight.
If sealants are required, it is advisable to follow the sealant manufacturer’s instructions with regards to application temperature, surface preparation, application technique, chemical compatibility, sealant location and dimensions, and ability to withstand specified movement.
AAMA 1607, Voluntary Installation Guidelines for Unit Skylights, provides guidance for installing pre-assembled unit skylights onto a roof. Sections 6.1 to 6.13 of AAMA 1607, a Fenestration and Glazing Industry Alliance (FGIA) document, cover pitched/steep slope applications, and Sections 6.14 to 6.19 cover low slope/flat applications. Unit skylights are typically designed to be installed at specific slope ranges, and some can even be installed at near-vertical slopes.
To ensure the integrity and performance of the entire roof system, including skylights, both the roof structure and the skylight are typically required to resist higher combined design loads when snow loads are expected. It is advisable to use skylights that are compliant with AAMA/Window and Doors Manufacturers Association (WDMA)/CSA 101/I.S.2/A440, North American Fenestration Standard/Specification (NAFS). Depending on the location, products may need to meet other performance requirements such as high velocity hurricane zone (HVHZ) conditions, per the American Society of Civil Engineers/ Structural Engineering Institute (ASCE/SEI) 7, Minimum Design Loads for Buildings and Other Structures. Skylights, and the roofs they are mounted in, are designed to resist the applicable environmental load requirements such as snow loads, wind loads, dead loads, and, in some cases, hurricane-induced wind-borne debris impact loads.
Lab testing
Laboratory testing of skylights is typically conducted by manufacturers prior to the product being released for sale or as part of independent certification processes. This form of testing takes place in a highly controlled environment, free from external variables such as wind and rain. This allows for focused assessment of the skylight’s design and construction. Within a laboratory setting, factors such as water pressure, spray patterns, and the duration of the test can be precisely regulated and consistently replicated. This allows for a thorough evaluation of the inherent water resistance capabilities of the skylight unit itself.
Limitations
A significant limitation of lab testing is that it cannot account for the complexities of real-world installation. The way a skylight is integrated into the roof structure, including flashing details, sealant application, and the compatibility with the roofing material, are all critical factors that are not assessed in a lab setting.
Additionally, lab tests are performed on sample units and provide a general indication of the product’s potential performance. However, variations in manufacturing tolerances and the specific conditions of each installation site can influence the actual performance of a skylight.
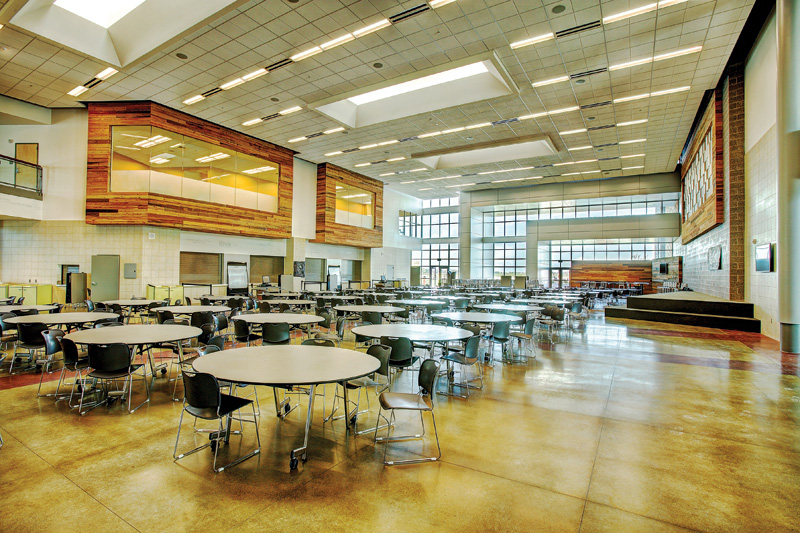
Onsite testing
Skylights often get unfairly blamed for leaks when it is almost always the fault of improper installation. Hence, it is important to conduct onsite testing after a skylight is installed.
The primary benefit of onsite testing is its ability to assess the quality of installation, which is paramount to preventing water leakage. This includes the effectiveness of flashing, sealants, and integration with the specific roof construction.
Further, onsite testing provides a specific evaluation of a particular skylight and its unique installation conditions. This accounts for the specific roof slope, roofing material, and other site-specific challenges.
When water leakage issues arise, onsite testing can be an invaluable diagnostic tool to pinpoint the source of the problem.
It is important to note that onsite testing takes place in an uncontrolled environment, where factors such as wind, temperature fluctuations, and accessibility to the roof can influence test results. Due to the uncontrolled environment, achieving the same level of precision and repeatability as in a laboratory can be challenging. Further, conducting onsite tests requires coordination after installation and access to both the interior and exterior of the building, which can sometimes be logistically complex, so it is recommended to perform tests in accordance with AAMA 501.2, Quality Assurance and Diagnostic Water Leakage Field Check of Installed Storefronts, Curtain Walls, and Sloped Glazing System, and AAMA 503, Voluntary Specification for Field Testing of Newly Installed Storefronts, Curtain Walls and Sloped Glazing Systems. Additional test methods of a more stringent nature incorporating the effects of wind can also be used per AAMA 501, Methods of Test for Exterior Walls.
The tests should be performed immediately after the skylight is installed, and before the installation of drywall or other interior finish materials. This can help determine water intrusion. If interior ceiling materials have been installed, they should be removed at the test area to allow visual access to check for water penetration. Alternate means of visual access can also be provided.
Water penetration resistance performance test must be performed in accordance with ASTM E1105, Standard Test Method for Field Determination of Water Penetration of Installed Exterior Windows, Skylights, Doors, and Curtain Walls, by Uniform or Cyclic Static Air Pressure Difference using Procedure A, “Uniform Static Air Pressure Difference.” The test involves applying a uniform water spray to the exterior of the specimen while maintaining the specified pressure difference. The field water penetration resistance tests should be conducted at a static test pressure of two-thirds of the specified project water penetration test pressure, but not less than 200 Pa (4.18 psf). The specifier may increase the field water test pressure to the value specified for the project. However, this should be stipulated in the project specifications.
The field installation conditions will influence product performance. Products tested in the laboratory are typically installed near-perfect for plumb, level, and square within a precision opening. Field test specimens, although installed within acceptable industry tolerances, are rarely perfectly plumb, level, and square. Shipping, handling, acts of subsequent trades, aging, and other environmental conditions may have an adverse effect on the performance of the installed specimen. Therefore, a one-third reduction of the test pressure for field testing is specified as a reasonable adjustment for the differences between a laboratory test environment and a field test environment.
Unless defined otherwise in project specifications, water penetration shall be defined as:
- Water penetration attributable to surrounding building conditions—The presence of water not contained within drained flashing, gutters, and sills, which did not originate from the fenestration product or the joint between the fenestration product specimen and the wall/roof;
- Water penetration attributable to the fenestration product specimen—The collection of up to 15 mL (0.5 oz) of water on an interior horizontal framing member surface in the 15-minute test period shall not be deemed a failure; or
- Water penetration attributable to the perimeter joint—Water not controlled by a water management system that indisputably originates at the perimeter joint.
If any of the specimen(s) do not conform to the prescribed water penetration resistance requirements, the installer must perform another detailed site inspection to determine the reason for non-compliance. Non-compliant specimen(s) must be repaired as required and retested as soon as practical.
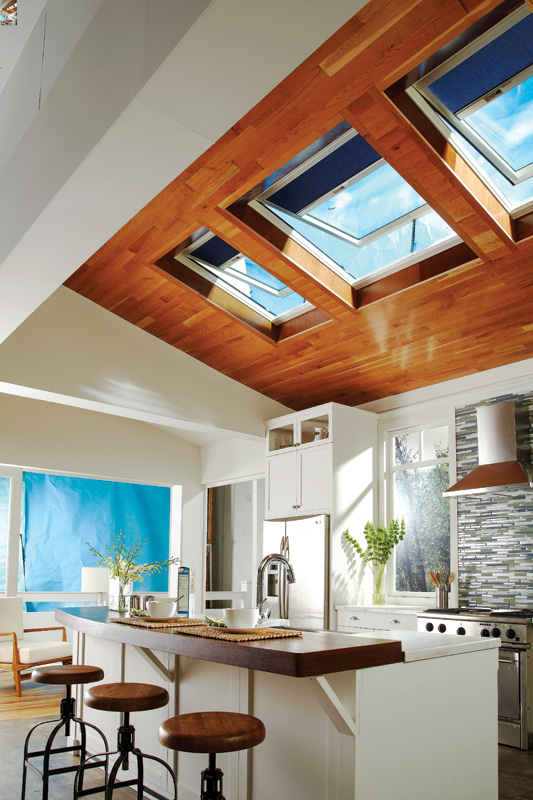
Sample specification
To standardize and simplify the writing of field-testing specifications for storefronts, curtain walls, and sloped glazing systems, FGIA has drafted the following short-form specification that can be used by architects and specifiers:
The newly installed (__________________) shall be field tested, as contractually agreed upon by the interested parties, by an AAMA-accredited independent laboratory, as engaged by (__________________), in accordance with AAMA 503, Voluntary Specification for Field Testing of Newly Installed Storefronts, Curtain Walls and Sloped Glazing Systems.
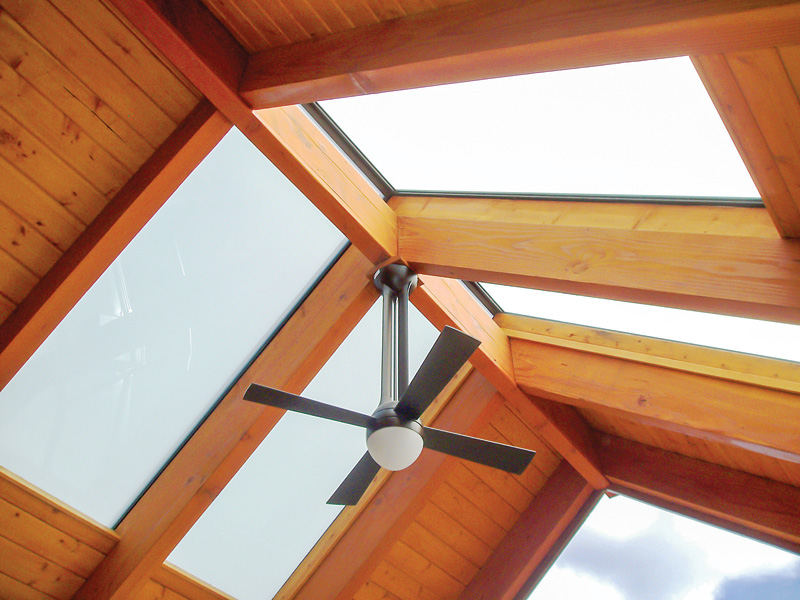
Remedial work
Regardless of when water resistance testing is performed, it is important to properly determine the cause when a leak occurs. Guessing the cause or charging forward with a remedy before fully understanding the cause is a big mistake. This approach will only eliminate the symptom in the short term, magnify the problem, and make correct remedial work more complex and costlier.
It should be noted that a leak at the skylight does not always mean the leak is caused by the skylight or the installation. It could also be a roofing system leak or a roof/wall interface issue at some other remote location (e.g. chimney flashing or flashing at a parapet/roof intersection).
When performing a water test to accurately determine the cause of leakage and location per AAMA 501.2 and/or AAMA 503, observers must be placed inside the building as the water spray is slowly distributed methodically from below the skylight first, working up to the skylight and then above the skylight. Time must be given to allow for water to work its way through to reveal its entry point and pathway. If water leakage occurs and the source cannot be identified, an isolation technique, per Section 4 of AAMA 501.2, should be followed to pinpoint water entry. Once the cause is determined, the remedy is usually clear. Good skylight design follows the principles of excellent watertight design in combination with provisions for condensation and “controlled” water collection and removal through the skylight frame to the exterior. Too often, the improper use of sealants to dam up water pathways that need to be maintained only worsens the problem. Poor remedial work can destroy the skylight’s ability to function as it was originally intended. In a similar manner, good installation practices can also be rendered dysfunctional. Thoughtful troubleshooting gets issues resolved simply, cost-effectively, and in a permanent manner.
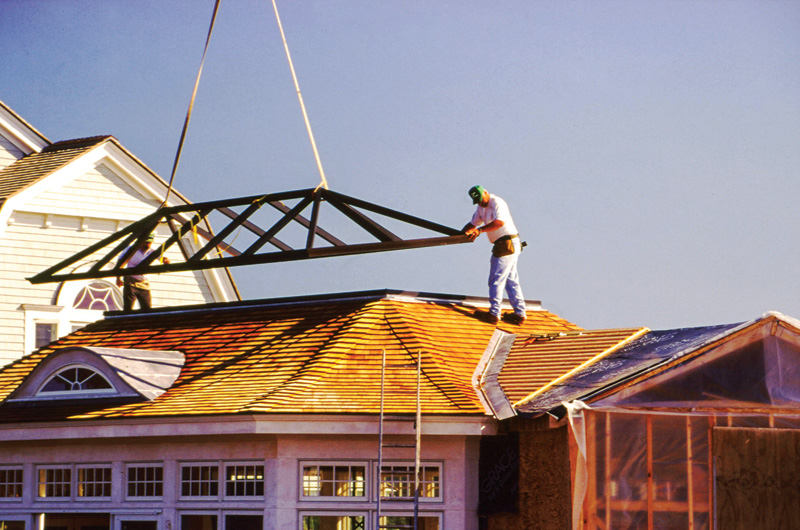
Conclusion
It is evident laboratory testing and onsite testing serve complementary roles in ensuring the watertight performance of skylights. Lab testing provides a fundamental assessment of the product’s inherent capabilities under ideal conditions, allowing manufacturers to develop and refine water-resistant designs. However, the ultimate performance of a skylight in a building is highly dependent on the quality of its installation. This is why onsite testing is crucial, as it validates the installed system under real-world conditions and identifies any potential weaknesses arising from the installation process or site-specific environmental factors.
With respect to proper installation and long-term performance, clear specifications for skylights are critical. Rely on available documents for best results. As mentioned earlier, lab testing assesses the skylight’s inherent design, while onsite testing specifically evaluates whether the system, including the installation, is effective. The emphasis on field testing in the context of skylights underscores the fact that even a well-designed and lab-tested skylight can be prone to leaks if not installed correctly.
References
∙ FGIA Documents. These are available in the FGIA Online Store at FGIAonline.org/store.
∙ AAMA 1607, Voluntary Installation Guidelines for Unit Skylights
∙ AAMA 501.2, Quality Assurance and Diagnostic Water Leakage Field Check of Installed Storefronts, Curtain Walls, and Sloped Glazing System, and AAMA 503, Voluntary Specification for Field Testing of Newly Installed Storefronts, Curtain Walls and Sloped Glazing Systems
∙ AAMA 501, Methods of Test for Exterior Walls
∙ AAMA/Window and Doors Manufacturers Association (WDMA)/CSA 101/I.S.2/A440, North American Fenestration Standard/Specification
Other resources
∙ American Society of Civil Engineers/Structural Engineering Institute (ASCE/SEI) 7, Minimum Design Loads for Buildings and other Structures
∙ More on performance testing.
∙ AAMA Laboratory Accreditation Program.
Author
Glenn Ferris is FGIA’s fenestration standards specialist. He began his career with the association in 2018. He has extensive experience in the fenestration industry dating back to 1992. Ferris is a liaison for many councils, committees, and study/work/task groups guiding them in the completion of the scope of each group. He can be reached directly at gferris@fgiaonline.org.
Key Takeaways
Skylights enhance aesthetics and energy efficiency by bringing natural light into buildings, but their performance depends heavily on proper design, material selection, and installation. Key considerations include skylight type, size, slope, and structural integration, along with components like curbs, diverters, ice breakers, sealants, and fasteners. Water leakage remains a major concern, making rigorous testing essential. Laboratory testing evaluates the product’s baseline water resistance, while onsite field testing verifies installation integrity under real-world conditions. Standards such as AAMA 1607, AAMA 503, and ASTM E1105 provide guidance for best practices and quality assurance. Field testing should occur before interior finishes are installed to catch issues early. Accurate diagnosis of leaks is critical—misidentifying causes can lead to ineffective and costly remediation. Ultimately, the combination of robust product design, proper installation, and clear specifications ensures long-term skylight performance and water resistance.