Closed-cell polyurethane: Insulate, seal, protect
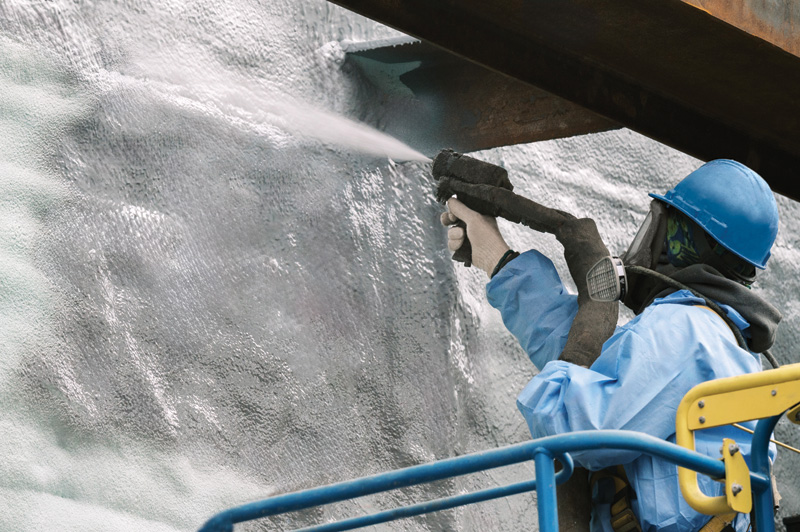
In any construction project, the integrity of a building’s foundation is paramount. Ensuring the longevity and structural soundness of a foundation requires effective waterproofing. If the water infiltrates, it can cause severe damage, including cracks, mold growth, and erosion of building materials. Fortunately, innovations in waterproofing technology—such as polyurethane sprayfoam and polyurea coatings—are revolutionizing the industry and transforming foundation waterproofing, focusing on the technical, economic, and environmental benefits. These advanced materials provide superior protection, enhance energy efficiency, and contribute to the sustainability of commercial buildings.
Effective waterproofing for commercial foundations
Waterproofing is essential for the long-term durability and stability of any building. Foundations, especially in large structures, are subject to various stresses from environmental factors such as temperature changes and moisture to the sheer weight of the building itself. Without proper waterproofing, water can infiltrate the foundation, leading to cracks, corrosion, and even complete structural failure in severe cases.
Traditional waterproofing methods, such as tacked membranes and bitumen coatings, have been used for decades. These are the common insulating/waterproofing materials for foundations in floodplains. However, these systems have limitations, including potential seams and weak points where water can penetrate. In contrast, polyurethane sprayfoam and polyurea coatings, while potentially carrying a higher initial cost, deliver superior seamless, flexible, and durable protection, making them cost-effective over the long term.
The trades involved are typically the same as those handling traditional waterproofing—foundation waterproofing contractors—although specialized training is often necessary to ensure the correct application of sprayfoam and polyurea coatings in accordance with manufacturer specifications.
Polyurethane sprayfoam and polyurea coatings are ideal for commercial waterproofing because they can handle large areas, withstand higher stresses, and resist environmental factors such as moisture and temperature changes. Their flexibility allows customization to meet specific challenges, such as vibrations or chemical exposure. Additionally, these high-performance solutions help commercial buildings meet strict regulatory standards.
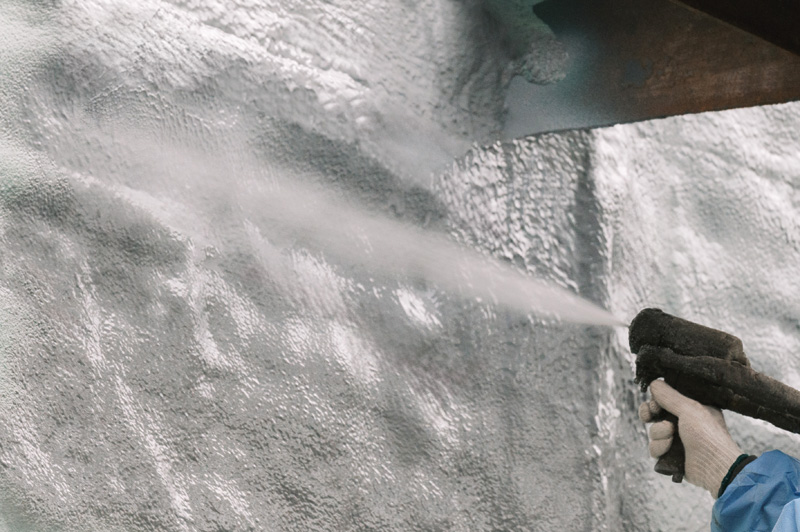
For a dry and durable exterior foundation
A stable and watertight building envelope is difficult to achieve when weather such as rain, snow, and ice affect the foundation. Issues such as cracks, water infiltration, and wood rot undermine the best building structure. The ideal time to insulate and waterproof a foundation is during the external excavation of an existing foundation or before backfilling a new one, ensuring a seamless seal between the footing and the wall.
Using sprayfoam insulation with a protective coating offers numerous benefits, simplifying the waterproofing process and enhancing overall efficiency. The foam expands to fill every crack, gap, or hole in the foundation, creating a continuous, seamless barrier that eliminates weak points common in traditional waterproofing methods such as membranes, which require seams or adhesives.
This comprehensive coverage strengthens the system’s integrity, effectively preventing water infiltration. In addition, sprayfoam is more adaptable to various application conditions, being less sensitive to temperature fluctuations than traditional materials. This flexibility allows for installation across a broader environmental conditions, minimizing weather-related delays. Moreover, sprayfoam insulates and seals simultaneously, reducing multiple steps into one trade workflow. This streamlines the process, cutting installation time, labor costs, and ultimately accelerating project completion, while providing superior long-term waterproofing and insulation performance.
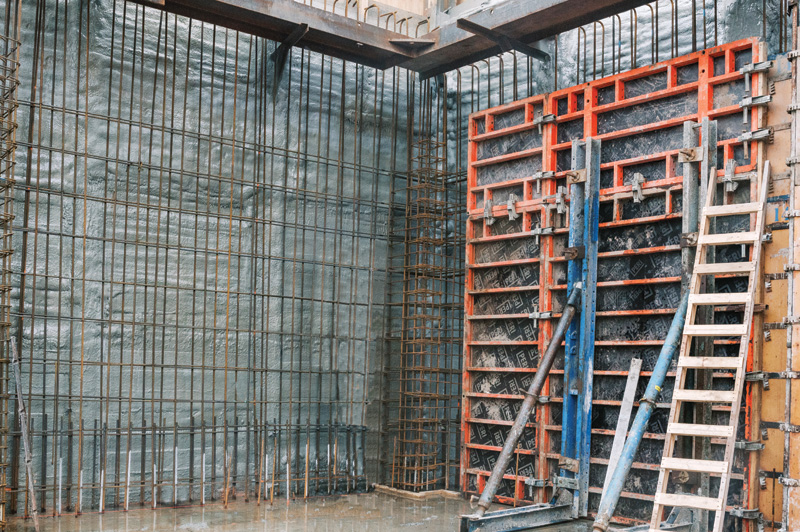
Surface preparation and application considerations
In addition to weather conditions, the condition of the concrete is critical. New foundations require sufficient curing time, typically at least 28 days, to ensure optimal strength before waterproofing.
This minimizes the risk of cracks and moisture infiltration. For existing foundations, the surface must be clean, dry, and free of loose debris for proper adhesion of the waterproofing materials. Following these guidelines ensures a durable, long-lasting seal and protection for the foundation.
Commissioning and testing considerations
In specific design applications, closed-cell sprayfoam insulation with an R-value of six per inch can meet and surpass energy code requirements while safeguarding the foundation. This insulation is applied from the exterior, forming a continuous, bonded, seamless barrier without needing surface prep, sealing seams, filling gaps, or gluing boards. In specific design applications, protection boards are necessary per building codes when using closed-cell sprayfoam insulation to safeguard it from external forces or environmental damage.
For example, a closed-cell polyurethane sprayfoam expands 30 times its original volume in just five seconds, thoroughly sealing the entire foundation. Typically, this sprayfoam is evaluated below grade, and findings show it maintains its integrity and is not prone to water absorption over time. It is resistant to flood damage.1,2
The closed-cell structure of sprayfoam is inherently water-resistant, preventing moisture infiltration and absorption, making it ideal for below-grade waterproofing. Evaluations show it maintains integrity even in prolonged water exposure or flood conditions. Its expanding nature ensures full coverage of foundation contours, eliminating weak points common with traditional methods such as tacked membranes.
While sprayfoam resists moisture well, polyurea coatings are required for first-rate durability. Polyurea provides superior resistance to water, chemicals, and abrasion, making it essential for foundations exposed to harsh conditions, continuous water pressure, or heavy foot traffic. The combination of sprayfoam for sealing and polyurea for waterproofing and added protection offers the best defense against long-term water damage, especially in flood-prone areas.
For new construction, the foundation is accessible from the exterior and can be insulated on its cold side, below grade, or before backfilling; this is the preferred approach for insulating below-grade foundations. Insulating the foundation from the exterior enhances energy efficiency, eliminates thermal bridges, stabilizes interior temperatures, and reduces the likelihood of condensation. In existing buildings, excavation may be necessary for waterproofing due to inadequate initial design or poor construction. A closed-cell polyurethane can be applied across the foundation surface, including over the footing, to direct water toward drainage systems. Depending on the foundation type, applying polyurethane directly onto concrete, block, or stone foundations is advisable. Some sprayfoam options are classified as damp-proof materials. Still, when waterproofing is critical, additional layers such as polyurea coatings, bituminous coatings, or drainage membranes may be installed directly on the foam where high water levels or accumulation risks exist.
Post-installation testing is sometimes required, particularly if the foundation waterproofing is tied to the building envelope commissioning (BECx) process. In such cases, visual inspections, adhesion testing, and/or electronic leak detection (ELD) might be used to verify the integrity of the waterproofing system. Commissioning activities typically focus on confirming proper installation, coverage, adhesion, and absence of voids in critical areas.
Maintaining the above-grade aesthetic during excavation
What should be considered for the above-ground portion of the foundation? There are several viable solutions, but one efficient method involves installing a galvanized Z-bar structure along the above-ground sections. This setup allows for the continuity of the exterior finish that extends both below and above ground. Installation of this structure is essential before any polyurethane product is applied. After insulating, it is advisable to mount a lightweight cement board onto the Z-bars. Following backfilling, a finishing layer can be applied to the cement board to achieve the desired aesthetic.
Polyurethane sprayfoam
Polyurethane sprayfoam is a dual-purpose material that delivers both high-performance insulation and an effective air and moisture barrier, which is particularly valuable in commercial foundation applications. The closed-cell formulation expands rapidly upon application, filling irregular voids, joints, and surface gaps to create a continuous bond across the foundation surface. For example, closed-cell polyurethane sprayfoam can expand up to 30 times its liquid volume within five seconds, ensuring thorough coverage even on complex geometries.
With an R-value of approximately six per inch, it meets or exceeds most commercial energy code requirements. Its rigid structure contributes significantly to thermal performance while minimizing thermal bridging. Its R-value adds dimensional stability and supports long-term durability, particularly when used below grade.
Sprayfoam is less sensitive to temperature and substrate conditions during application than traditional materials. It adheres well to substrates such as concrete, wood, metal, and masonry, forming a reliable base for subsequent protective layers—especially polyurea coatings. These coatings bond directly to the sprayfoam surface without requiring primers or adhesives, creating a monolithic system that resists water infiltration, freeze-thaw cycles, and mechanical stress.
Polyurea coatings
Polyurea coatings are critical for commercial foundation waterproofing due to their fast-curing, flexible, and highly durable nature. Combined with polyurethane sprayfoam, they create a fully bonded, monolithic barrier that resists water intrusion, mechanical wear, and chemical exposure—even under harsh site conditions.
To ensure proper adhesion and long-term performance, surface prep is essential. Concrete must be clean, dry, and have a moisture content below four percent, with a pH between seven and 10. Application should be performed only when substrate temperatures exceed 5 C (41 F), ambient temperatures range from 15 to 35 C (59 to 95 F), and relative humidity (RH) is below 85 percent. The substrate also needs to be at least 3 C (5.4 F) above the dew point to avoid condensation.
Polyurea is applied using high-pressure spray equipment and cures within minutes, allowing rapid progress on commercial builds. Once cured, it forms an elastic, seamless membrane that expands and contracts with the foundation and maintains its integrity during freeze-thaw cycles, water exposure, or prolonged stress.
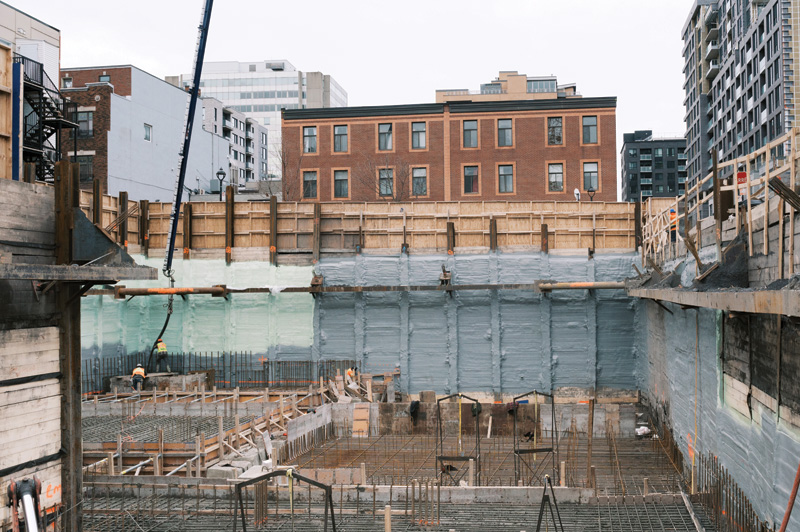
Case study
To illustrate the effectiveness of polyurethane sprayfoam and polyurea coatings, consider this project on a commercial construction site. A leading insulation and waterproofing company was tasked with addressing the foundation waterproofing needs of a commercial building.
During the assessment and planning stage, they meticulously evaluated the steps needed to perform the work with the highest quality and on time. The project, conducted in cold weather conditions, involved a building with a blindside wall constructed directly adjacent to an existing structure or retention system. With the project being downtown and the limited space, it was challenging to waterproof the foundation to be poured. Traditional excavation methods were impractical due to the building’s proximity to other structures, sidewalks, and towers.
Using traditional materials, the new foundations would need to be poured and excavated on its exterior, and then the insulation and waterproofing would be applied on the exterior of the new foundation. All this was not entirely possible. To overcome this challenge, the project team decided to insulate the retaining wall instead, apply the sprayfoam first, the waterproofing on top, and then pour the concrete, inverting the process. The team used a crane to gain a clear vantage point, enabling them to apply the waterproofing system effectively. From this elevated position, they applied a 76-mm (3-in.) layer of high-performance sprayfoam, followed by a polyurea coating to the surface of the adjacent structure or retention system. Once the membrane was installed, the concrete foundation was poured directly on top, reaching a depth of 9 m (30 ft). This approach allowed for precise application of the waterproofing membrane and ensured project completion within the confined space. In contrast to traditional methods requiring extensive excavation, polyurethane sprayfoam eliminates the need for significant digging, reducing costs and installation time.
Combining polyurethane sprayfoam and polyurea coating proved the optimal solution for durable, long-lasting waterproofing. This system involves a two-component assembly, with a polyurea membrane applied directly over the hydroflouroolefin (HFO) sprayfoam. This waterproofing solution meets AC29 standards for below-grade applications. It complies with the International Building Code (IBC) as confirmed by a UL report.
The results of the project demonstrated several key benefits. The combination of polyurethane foam and polyurea coating improved the foundation’s structural integrity by creating a monolithic barrier that prevented water infiltration and protected against structural movement and freeze-thaw cycles. Additionally, the high R-value of sprayfoam enhanced the building’s thermal efficiency, reducing heating and cooling costs while improving occupant comfort. The project was completed efficiently, even with space limitations, resulting in significant cost savings compared to traditional methods, with reduced site preparation, maintenance and energy costs, providing a rapid return on investment (ROI). The polyurea coating’s flexibility and elongation allowed it to adapt to the foundation’s movement, preventing cracks and leaks even in extreme temperatures, while its resistance to chemicals and mechanical wear further contributed to the foundation’s long-term durability.
Economic and environmental benefits
In combination, polyurethane sprayfoam insulation and polyurea coatings offer significant economic and environmental benefits. Some of the key advantages include:
- Long-term cost savings—Although the initial investment in polyurethane and polyurea systems may be higher than traditional materials, they offer significant advantages, including quicker installation times and substantial long-term energy savings, making them a cost-effective solution over time.
- Energy efficiency—Polyurethane sprayfoam provides excellent insulation, which helps regulate the building’s temperature and reduces energy consumption. This lowers heating and cooling costs, making the building more energy efficient.
- Eco-friendly formulations—Many polyurethanes and polyurea products are crafted with environmentally responsible ingredients, such as low levels of volatile organic compounds (VOCs) and sustainable blowing agents. For instance, some formulations feature an Ozone Depleting Potential (ODP) of 0.0, meaning they do not harm the ozone layer, and a Global Warming Potential (GWP) of less than one, indicating minimal impact on global warming compared to CO2. These formulations promote healthier indoor air quality (IAQ) by reducing VOC emissions and limiting exposure to harmful chemicals. At the same time, their low ODP and GWP contribute to more sustainable construction practices, as supported by their Environmental Product Declaration (EPD). This combination helps create safer indoor environments and lessens the overall environmental footprint.
- Sustainability—Polyurethane sprayfoam insulation helps reduce the building’s overall carbon footprint by improving its energy efficiency. The long-lasting protection these materials ensures the building remains in good condition for decades, minimizing the need for reconstruction or extensive repairs.
- Waste reduction—The seamless application of sprayfoam and polyurea coatings reduces material waste compared to traditional waterproofing methods, aligning with sustainability goals.
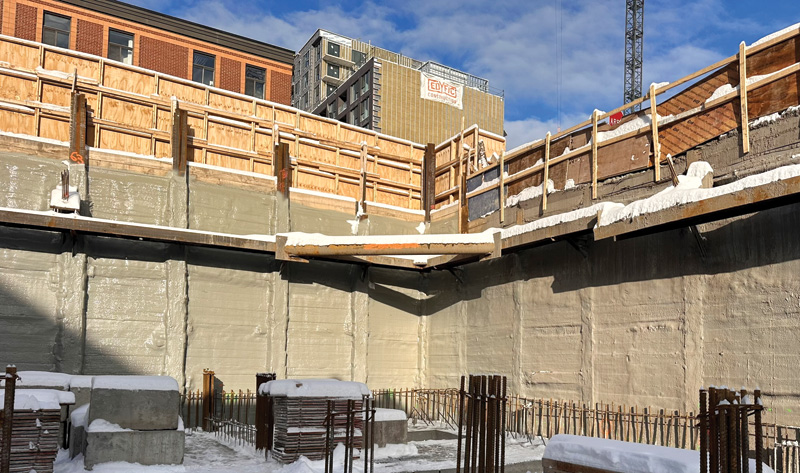
Best practices for application and maintenance
Following best practices for application and maintenance is essential to fully capitalize on the advantages of polyurethane sprayfoam and polyurea coatings.
During application, it is critical to properly prepare the surface by ensuring the foundation is clean, dry, and free of contaminants, as this promotes optimal adhesion. It is also important to follow the manufacturer’s recommendations for the appropriate thickness of the polyurethane foam and polyurea coatings. Applying too thin a layer may reduce waterproofing effectiveness, while an overly thick layer can lead to
material waste.
Additionally, applying these materials under suitable environmental conditions is crucial. Extreme temperatures or high humidity can affect curing times and adhesion, so scheduling the application during optimal weather conditions ensures the best results.
The future of commercial foundation waterproofing
Polyurethane sprayfoam and polyurea coatings represent the future of commercial foundation waterproofing. As demonstrated by the case study, the combination of sprayfoam and polyurea coatings enhances the structural integrity of a foundation alongside further benefits.
Investing in polyurethane and polyurea systems is a smart choice for builders, architects, and engineers looking to future-proof their commercial projects. These materials offer superior protection, contribute to sustainability goals, and provide a return on investment that traditional waterproofing methods cannot match.
By adopting these cutting-edge solutions, construction professionals can ensure that commercial foundations remain strong, secure, and impervious to the elements for decades.
Notes
1 Refer to Technical Bulletin 2, Flood Damage – Resistant Materials Requirements, FEMA, August 2008.
2 Read “Severe Weather and Closed-Cell Spray Foam: A Better Building Technology” on Honeywell.
Author
Jean-François Lupien is the global director of product management at Huntsman Building Solutions.
Key Takeaways
Closed-cell sprayfoam and polyurea coatings offer seamless, energy-efficient, and long-lasting waterproofing for commercial foundations. Together, they protect against moisture, cracks, and wear while reducing labor, improving insulation, and supporting sustainability goals—making them a smart, modern alternative to traditional waterproofing methods.