Customize acoustic ceilings with specialty coatings
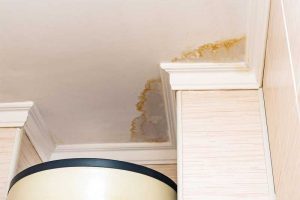
Installation is important
Every product is only as good as its installation. At best, it is risky to specify a product without assurance the application will be performed in accordance with the manufacturer’s recommended procedure. To ensure an applicator properly applies the product, specifiers and designers can utilize Section 09 51 23–Acoustical Tile Ceilings, which defines the requisite qualifications. It also spells out the consequences of substituting with an unauthorized product ‘equivalent.’
In the author’s experience, many of the common techniques used by the commercial painter negatively impact the absorption of sound because most contractors have not been informed of the need to maintain acoustical properties and are unfamiliar with the finer points of such a process. Further, they are not necessarily adept at protecting merchandise or furnishings in fully occupied spaces, a necessary requirement in the field of commercial property renovation.
In response, some acoustical coating manufacturers have developed a training program for contractors, specific to the application of their products in occupied spaces. Understandably, the applicators completing such a program satisfactorily are more likely to make a proper installation than others. Under the quality assurance (QA) portion of the guide spec, it is recommended that a trained applicator be identified with the provision the manufacturer of the specified product offers such a training program.
New construction
It must be acknowledged greater attention is now being paid to the benefits of using an acoustical coating on new construction projects as architects and specifiers are concerned with what many call “performance characteristics.” Does the product under consideration offer a level of performance that satisfies the project requirements? As an example, is the NRC at a satisfactory level? Is there a need for a Class-A fire retardant rating? What about toxicity in case of a fire? Is the physical size/shape of the product appropriate in the space provided? All these and other questions need to be answered by the architect before settling on a product that can be expected to perform as required.
Additionally, specifiers are concerned with the need to provide a design satisfying the “aesthetic standards” they wish to achieve. The acoustical product must have a shape and size that is appealing and appears natural in the space it is intended to occupy. The overall appearance is also dependent on using the proper mix of colors. Until the advent of the acoustical coating, color was a significant stumbling block.
Colors galore
Typically, acoustical product manufacturers are limited in the number of colors they can provide. The solution is to resurface the product with a coating tinted to a designer color. However, just as with the restoration of acoustical products, conventional paints cannot be used to provide the desired colors on new products without compromising the acoustical properties. This is not the case with an acoustical coating.
The better acoustical coating manufacturers have three formulations (product bases) for pastel, mid-tone, and deep-tone colors. In other words, any color—from white to black—can be produced as quickly as it takes to tint the appropriate base. The additional cost associated with the production and application of the coating is significantly less than the up-charge would have been if the manufacturer of the acoustical product had been able to produce the desired color. Further, there is very little wait time, as it takes a matter of days to tint the product and ship it out.
On some projects, the color-tinted acoustical coating is applied prior to shipping the product to the jobsite. In other instances, it is more practical to install the product first, and then spray the entire ceiling system with the coating at one time. When sprayed in place, the T-bars and air-diffusers can be coated at the same time for a more complete and consistent result. The approach taken varies from project to project.