Daylighting and performance considerations for polycarbonate glazing systems
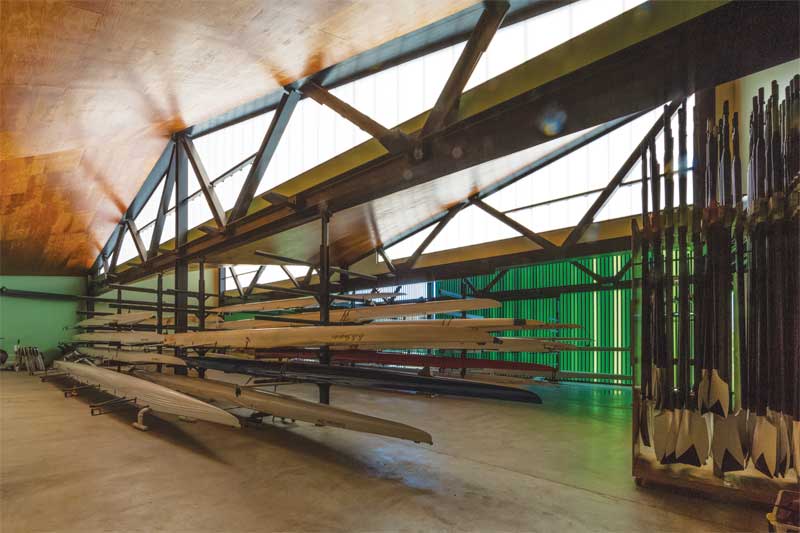
Photo courtesy William Zbaren Photography
Flammability and fire testing
As a material, polycarbonate will not support its own combustion; meaning, when the source of heat or ignition is removed, polycarbonate will cease to combust. In comparison, FRP systems support their own combustion; once ignited, the material continues to burn. Even if the initial source of heat or ignition is removed, FRP continues to burn until all the material is consumed.
ASTM E84-17a, Standard Test Method for Surface Burning Characteristics of Building Materials, is the current, standard test method for surface burning characteristics of building materials, and most often used for translucent vertical wall systems. Code officials often refer to the test values published in ASTM E84 for flame spread index (FSI) and smoke-developed index (SDI) to evaluate acceptable materials for their applications.
FSI and SDI measure how far and how fast flames spread across the surface of a test sample and how much smoke is generated. Both FSI and SDI are expressed as numbers on a continuous scale, where inorganic-reinforced cement board is zero and red oak is 100. FSI and SDI values for polycarbonate glazing vary greatly depending on the thickness, configuration, and composition of the panels.
Based on FSI and SDI numbers, material is categorized as Class A, B, or C. Given smoke inhalation statistically is more deadly than fire, the SDI must be less than 450 to meet all class ratings. The highest level of performance, Class A, most often is required in vertical wall applications.
Air, water, and structural performance
Physical tests typically are conducted to determine the air and water infiltration as well as the structural performance of a daylighting assembly. The relevant test methods for translucent vertical wall systems are:
- ASTM E283-04 (2012), Standard Test Method for Determining Rate of Air Leakage Through Exterior Windows, Curtain Walls, and Doors Under Specified Pressure Differences Across the Specimen. At a test pressure of 0.299 kPa (6.24 psf), high-performance daylighting assemblies typically have air infiltration of no more than 28.32 cm3/sec per 0.093 m2 (0.06 ft3/min per sf) of glazing area.
- ASTM E331-00 (2016), Standard Test Method for Water Penetration of Exterior Windows, Skylights, Doors, and Curtain Walls by Uniform Static Air Pressure Difference. High-performance daylighting assemblies provide for no water penetration when tested vertically at a test pressure equal to 15 percent of the project design pressure.
- ASTM E330/E330M-14, Standard Test Method for Structural Performance of Exterior Windows, Doors, Skylights, and Curtain Walls by Uniform Static Air Pressure Difference. In all cases, the panel must be capable of meeting the design load for the project based on relevant code requirements, and ASTM E330’s test pressure performance, without exceeding deflection requirements.
Sustainability and longevity
In addition to aiding a building’s energy-efficiency and its occupants’ comfort, health, and well-being, polycarbonate glazing systems also support environmental and economical practices.
Polycarbonate glazing may be specified with up to 40 percent recycled content, depending on the project’s performance needs. At the end of its useful life in a vertical wall system, the polycarbonate panels and metal framing are 100 percent recyclable.
A 25-mm (1-in.) thick piece of polycarbonate glazing weighs approximately 3.17 kg/m2 (0.65 lb/sf) compared to 30.5 kg/m2 (6.25 lb/sf) for an IGU of the same thickness. Compared with IGUs and other heavy glazing systems, the lightweight polycarbonate daylighting assemblies require:
- less material for structural supports;
- less fuel, and associated costs and emissions for transportation; and
- less labor, and associated time, cost, and potential for injuries or damages.
These systems also involve minimal cleaning and maintenance. If necessary, the tongue-and-groove assembly usually makes repairs or replacements that are simple and quick.
For 50 years, European buildings have incorporated polycarbonate glazing systems in vertical wall applications. Some have remained unaltered for more than four decades. Manufacturers say warranty claims are very rare. Typically, they list DYI, LT changes, and brittleness of polycarbonate glazing panels and framing finish within their system warranty.