Design assist: Reshaping the project experience
TOOLS OF THE TRADE
John Scorsone
Architects are not experts in building materials, and sometimes they may specify a product for a particular project element without realizing it may not be the right fit for their design needs. Through the design-assist process, a manufacturer could fill this knowledge gap by providing the project team with everything they need to make the most informed decision possible.
Projects with architectural metal are especially suited for the design-assist process. Widely used in construction, architectural metal can be seen in almost any application imaginable, whether one is working with stainless steel, coated aluminum, or another natural metal. It also has the ability to form shapes and profiles in many ways—whether extruded, formed, or perforated—to achieve an architect’s vision. Metal, however, has a few constraints, sometimes due to an architect’s limited expertise regarding a manufacturer’s fabrication capabilities, and the fact that, like any other product, there are restrictions to working with solid metals, such as size, proportions, and how the building material is affected when it is manipulated. Design assist allows the project team and product manufacturer to collaborate and determine the most suitable approach.
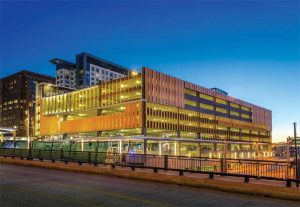
What is design assist?
The traditional design, bid, build workflow is adopted by many in the industry, but it may not be the most effective method to get the job done. Different teams are only brought into the process on an as-needed basis. For example, the general contractor (GC), specialty trades, or product manufacturers are only involved at the bid stage. Design assist can promote collaboration and a shared understanding of what a project entails at an earlier stage itself.
“Design assist has evolved as a procedure to address complexity in the construction industry and how technology has advanced and diversified over the last 30 or 40 years,” says Robert Matthew Noblett, partner, Behnisch Architekten.
In this approach, the architect develops their concept, but then includes the GC, construction manager (CM), contractor, and material supplier in a series of collaborative discussions to ultimately finalize the design. This enables the architect to maintain the project budget and modify expectations or design elements as needed. With design assist, all participants work together with the same key objectives in mind: To develop and maintain a project budget while simultaneously working through the design and establishing the means and methods to turn the concept into a reality. This is also known as a ‘constructability review.’
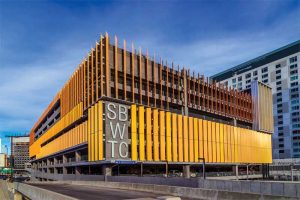
Case studies: Where design assist was successful
It is advisable to employ design-assist for projects with metal as it is a complex building material. Some projects using this process include the Hartford Hospital Bone and Joint Institute, Connecticut, South Boston Waterfront Transportation Center’s (SBWTC’s) parking garage, Massachusetts, and Pennsylvania State University (PSU) Chemical and Biomedical Engineering Building. Each project is currently in a different phase of completion, but all have followed a similar path. Hartford Hospital was completed in 2015 and SBWTC’s garage was finished in May 2018. At the time of the writing, the PSU project was still under construction/fabrication.
PSU
The design-assist process for the PSU project started early when the architect was developing the schematic designs for the building’s shell. The architect created hand-drawn sketches illustrating the general makeup of the wall construction and identified items such as studs, sheathing, air/vapor (A/V) barriers, and metal panels, but the outline lacked information for panel sizes and joint locations.
The manufacturer worked with the entire team from an early stage and learned several things about the project’s requirements. The architect was looking for an economical zinc façade and solid aluminum plate for accent panels, a soffit at the ground floor exterior, and one for canopy cladding. To keep costs down on the zinc panels, a standard wall system was modified and a custom panel reveal joint mimicking a standard one was also created.
The final appearance included the sightlines and panel reveal joints originally specified by the architect. Thanks to this collaboration, the installation contractor had to use only 50 percent of the total number of zinc panels estimated, saving the owner money on field labor costs and time.
Additionally, the exchange of information was fluid, yet effective. A building information model of the project was created with computer-aided design (CAD) and continuously shared with the entire team.