Design considerations for metallic finishes on architectural aluminum
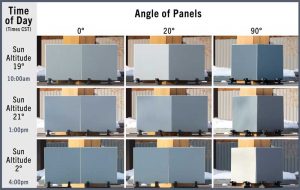
Images courtesy Linetec
Managing visible variation
With all of the variables to control in spray-applied metallic coatings, the reality is some inconsistencies will result. The first step in managing and minimizing visible variation is to recognize and mitigate for the greatest risks.
Be aware the same qualities that create the vibrancy and reflectivity of metallic coatings can also cause variations in appearance within a project, an elevation, or even a single part of a metal building product. A project with lots of aluminum wall panels is more likely to show variation than one with extrusions, such as on window or curtain wall framing, or one with panels separated by masonry or other materials that disrupt the overall visual continuity of a building’s exterior. It is pertinent to always paint the same elevations and adjacent panels on the same application run.
It is recommended to specify all the paint be made in a single batch, especially when working on a large project or one with multiple phases. Similarly, when possible, it is important to indicate a single finisher should apply all the paint to ensure the greatest consistency and quality control. This will minimize the potential variation between different paint applicators and equipment.
Panels painted in a factory setting can measure within specification and appear visibly to match panel to panel on the paint line, but when installed, they can be perceived as non-matching under natural light conditions. The difference in actual versus perceived color is known as metamerism. Remember that sunlight and shade show color differently, and that metamerism will be experienced differently throughout the day and year. The reflective properties of the metallic flakes means that the same painted surface will look different depending on the viewing angle, the angle of the sun or other light source, and the intensity and type of the light source.
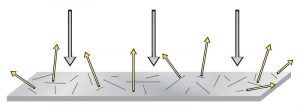
Metamerism can also present challenges when creating and viewing samples. A complete color range of sample variations is not possible with these paints since the ‘color space’ is a three-dimensional sphere and there are an infinite number of directions a color can range. The ‘L-scale’ is one of the three axis in the Lab color sphere and the one that best measures brightness. For most realistic metallic paint samples, it is advisable to review a sample in the L-scale. Also, it is recommended to request color chips from the applicator rather than the paint manufacturer. The finisher’s application equipment can result in a slightly different color or appearance relative to the paint manufacturer’s laboratory-produced samples.
Some metallic colors have a greater propensity for visible variation. This can be particularly noticeable with bright, semi-transparent colors such as silver metallics. When bright silver metallic coatings are specified, it is important to consult with the finisher to avoid unpleasant surprises and discuss alternatives such as clear anodize. When a uniform aluminum alloy is specified, an anodize finish can enhance the metallic aesthetic and may have less visible variation than the flop of the flake phenomenon seen with painted metallic coatings.
As another, economical alternative to metallic coatings, mica paint coatings provide a similar appearance with slightly less brilliance or depth. These two-coat systems are manufactured with a non-conductive mineral rather than with conductive metal. Due to their inert formulation, they eliminate the need for a clear coat, are less sensitive to flake orientation, and minimize visible variation improving the overall color consistency.
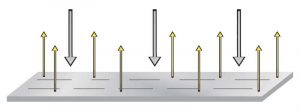
Performance specifications
The industry-leading specification guidelines for applying architectural coatings and anodize finishes are published by the American Architectural Manufacturers Association (AAMA).
For painted metallic coatings on exterior aluminum building products, AAMA 2605, Voluntary Specification, Performance Requirements and Test Procedures for Superior Performing Organic Coatings on Aluminum Extrusions and Panels (with Coil Coating Appendix) and 2604, Voluntary Specification, Performance Requirements and Test Procedures for High Performance Organic Coatings on Aluminum Extrusions and Panels (with Coil Coating Appendix) are the appropriate performance specifications.
AAMA 2605
This is the high-performance exterior specification. A paint that meets this specification would be a 70-percent fluoropolymer resin-based coating. These finishes exhibit outstanding resistance to humidity, salt spray, color change, chalk, gloss loss, and chemicals. An application for this finish would include monumental architectural projects and ones that require long-lasting aluminum surfaces.