Designing with foam plastic insulating sheathing
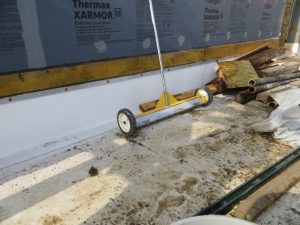
Cladding specific applications
Each manufacturer publishes their own test report outlining different overall wall assemblies viable with their FPIS. These reports outline numerous allowable cladding types, including masonry, metal panel, cement board, and stucco along with air/weather barrier accessories.
Masonry systems often require a single anchor style lateral tie plus solid cap washer to limit the penetrations through the insulation board. Thermally, these single penetration lateral ties outperform dual anchor lateral ties; however, they may limit installation tolerance when compared with a standard two-piece adjustable lateral tie. In addition, the single attachment point style of lateral tie inherently lacks the redundancy of a two-point system.
Stucco systems over metal lath involve a series of regularly spaced fasteners offset from the FPIS substrate. The offset fastener configuration prevents an adequate seal where the anchor penetrates the FPIS. To accommodate this issue, manufacturers may require either pre-striping anchorage points with FPIS accessory tape or fluid at stud locations, or the introduction of furring strips and pre-striping. This is not to mention quantity of attachment points for stucco (177.8 mm [7 in.] spacing at framing members) compared with standard 406.4 mm (16 in.) lateral tie spacing for masonry.
Metal panel systems, which are frequently attached to a subgirt system, present relatively fewer installation challenges. The girts can be sealed to the FPIS prior to cladding attachment, and no blind fastening through FPIS occurs. Metal cladding systems may be utilized in an open joint fashion; in this case, long-term ultraviolet (UV) stability should be factored into the design of the air and weather barrier system. Additionally, metal conductivity and related heat buildup may present a separate set of issues related to dimensional stability. Research has consistently shown that foam plastics experience both elastic and inelastic (i.e. permanent) board deformation at elevated service temperatures. However, these studies typically focus on roofing type assemblies where conductive heat transfer should be anticipated.
Each cladding type will have its own series of nuances. This is not meant to sway a designer away from FPIS systems or from a certain cladding and FPIS pairing, but rather to bring attention to potential challenges presented by various product combinations. In general, any cladding system requiring direct attachment, concealed or exposed, will likely require supplementary steps to ensure a sealed penetration, as compared with a cladding attached to sub-framing.
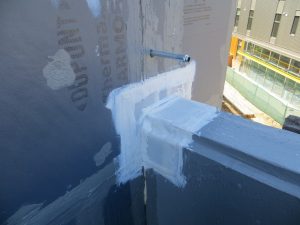
Construction challenges
For every benefit, there is always a countering cost. This may become an actual financial cost, but typically this presents as a construction variable. There are several challenges designers should consider as they proceed with an all-in-one FPIS system.
Proprietary-like assembly
To achieve code compliance, FPIS systems require full assembly testing to confirm several performance metrics–the result provides rating for an assembly of components working together. Testing is an expensive endeavor, and thus most manufacturers have only performed limited tests relative to the available products on the market. This means assembly components are not interchangeable. In construction, it is routine for product shortages, time constraints, or other limitations to necessitate a building component substitution.
In short, if a single assembly component is not available, the system may not be viable or may require modifications to meet testing or code requirements. For non-combustible assembly components, substitution options may abound. For combustible components, on the other hand, options may be severely limited. For example, if a manufacturer has a tested assembly with a specific closed cell spray foam which is not available, substituting an alternate spray foam may trigger significant detail changes (Figures 4-5).
Engineering Judgements (EJ) may provide one workaround to create some measure of interchangeability. Some manufacturers facilitate the designer’s cladding selection process by listing options it believes would be acceptable with an EJ.10 However, there are caveats. EJs are used to resolve field needs when a tested design, system, or assembly is unavailable but there are two critical issues with pursuing an EJ. First, a fire protection engineer may not find a substitution material equivalent to the tested material. Second, acceptance of the EJ is at the sole discretion of the authority having jurisdiction (AHJ), which may review the report and deny the request.
Material resilience
Polyiso is low density; this is an inherent property necessary to create the desired thermal resistance. However, low density also creates a material vulnerable to site damage during construction (Figure 6), and because the FPIS in our scenario provides all the building enclosure barriers, damage to FPIS equates to damage to the entire building enclosure assembly.
This is easily remedied where an issue is exposed; however, concealed deterioration is just as likely to occur. Where a cladding contactor lacks familiarity with FPIS systems, breaches may go unnoticed and become buried within the completed wall assembly. Requiring coordinated mockups with all parties participating in a joint discussion may limit this issue.