Field mockups for exterior wall systems: Will the design pass the test?
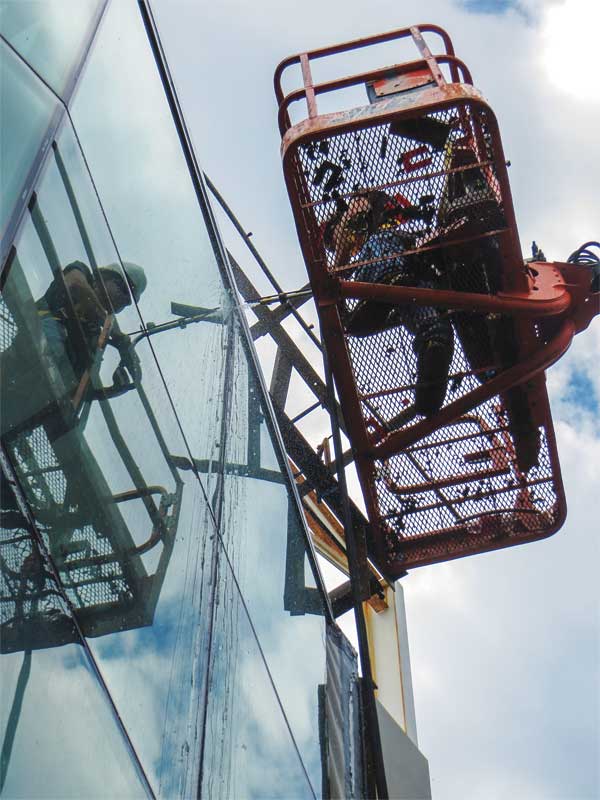
Case studies
The following two cases studies illustrate the benefits of mockup testing and lessons learned.The first case study includes laboratory, field, and in-situ mockups for an elaborate custom faceted curtain wall system, and illustrates a mockup’s usefulness in resolving performance issues before they become manifest within the construction. The curtain wall system consisted of structural steel mullions, which supported aluminum carrier and cassette framing onto which the insulated glass unit (IGU) was structurally glazed. The system included field-applied primary and secondary weather seals. Given the complexity and nonstandard use of the curtain wall system, the authors determined a full-scale laboratory mockup would be required in addition to a visual field mockup.
The laboratory performance testing included the standard testing protocol outlined in AAMA 501. The authors also incorporated AAMA 501.2, Quality Assurance and Diagnostic Water Leakage Field Check of Installed Storefronts, Curtain Walls and Sloped Glazing Systems, which involves a calibrated spray nozzle, for testing the primary and secondary weather seals after both are installed for water infiltration resistance. Additionally, the project team incorporated a modified AAMA nozzle test to evaluate the effectiveness of the drainage plane between the primary and secondary seals. The AAMA nozzle test was conducted at a modified water pressure; water was applied to the openings made in the primary weather seal to confirm adequate drainage from the weeps within the system.
During nozzle testing, holes were cut in the secondary weather seal at the head of the mockup (Figure 2) and the nozzle was used at a low pressure 34 kPa (5 psi) and volume to test the drainage plane between the sealant joints (Figure 3). Within minutes, water leakage was observed on the interior side of the curtain wall mullions. However, water was not draining from the weeps. Portions of the primary seals were then removed to discover primary and secondary seals had bonded together at certain locations, thus preventing drainage (Figure 4). It was determined the leakage was a result of tooling marks during the application of the secondary weather seal around the cassettes and glazing chairs (Figure 5).
Given the laboratory mockup was offsite at a testing facility, the project team elected to use the onsite visual mockup (Figure 6) as an opportunity to correct the observed defects in the sealant installation. The visual mockup did not have either the primary or secondary seals installed previously, which allowed for further review of the sealant detailing around the cassettes and chairs as these seals were installed. The project team modified the backer rod sizes to better accommodate the required spacing needed to adequately install the sealant while allowing drainage. Testing was then performed in two phases. First, the AAMA nozzle testing of the primary seal without the secondary seal installed (Figure 7) was performed, and then the AAMA nozzle test was repeated with the secondary seal installed. The modified AAMA nozzle test to verify drainage capability was also conducted.
The nozzle testing allowed the design team to evaluate all of the sealant joints installed within the curtain wall assembly, which would have been cost prohibitive with a chamber test. Without the modified AAMA nozzle testing procedure, the project team would likely not have identified the potential water leakage problems that could have occurred after the building was occupied and in service. This was a fitting example of the entire team working together to ensure a successful outcome.
The second case study is an example of why it is critical to engage all parties involved in the mockup as early as possible to establish requirements for mockup construction, including elements for supporting it. The mockup was a combination of a glass/metal curtain wall and fiber cement panel rainscreen wall system. It consisted of a full-scale, two-story laboratory mockup. The performance testing included structural performance, static air and water infiltration, and deflection and dynamic water testing. The structural testing was conducted in two phases: an initial 100 percent design load test with subsequent air and water infiltration tests, followed by a second structural test at 150 percent of design load (Figure 8). During the second structural test the authors observed a failure in the ad-hoc stud wall supporting the mockup because the stud framing installed had not been designed for the applied structural load. In this case, the mockup was constructed and tested before a framing subcontractor was hired for the project and before the wall framing was engineered. Fortunately, the observed failure occurred at the end of the testing protocol after all of the other testing was successfully conducted. The project team could design the framing system and incorporate the changes into the final construction documents.
Conclusion
The integrity of a building enclosure is dependent on both the performance of its individual components and systems, and the performance of the transitions between these systems.
Mockups are useful to help verify the enclosure design is constructible, integrates properly, and meets required performance expectations. When properly used, mockup construction and performance testing allow the project team to collaboratively work out detailing and compatibility issues arising during the course of construction, verify proper function of the intended construction, and apply the results from the process to the project, thereby avoiding costly, repeated defects in the completed building.
Daniel Clark joined Simpson Gumpertz & Heger Inc.’s building technology group in 2009. He has worked on multiple projects involving investigation, survey, rehabilitation of historic buildings, peer reviews, and design of building enclosure systems, and construction administration services for repairs or new construction of building enclosures and roofing/waterproofing systems. Clark can be reached at dpclark@sgh.com.
Eric Olson, PE, is an associate principal in Simpson Gumpertz & Heger Inc.’s building technology group. He has 20 years of experience in the investigation and repair design of building enclosure systems, including windows, curtain walls, masonry, exterior insulation finish system (EIFS), and stucco, roofing, and plaza and below-grade waterproofing. Olson can be reached via e-mail at ekolson@sgh.com.