High-performance air- and water-resistive barriers deliver improved sustainability
The Air Barrier Association of America (ABAA), which provides a wealth of expertise on air barrier technology, addresses this in each of their specifications in section 1.3J (1.3I for spray polyurethane foam [SPF]). In the document, this clause states, “Obtain primary ABAA Evaluated Materials from a single ABAA Evaluated Manufacturer regularly engaged in manufacturing specified mechanically attached flexible sheet. Obtain secondary materials from a source acceptable to the primary materials manufacturer12.”
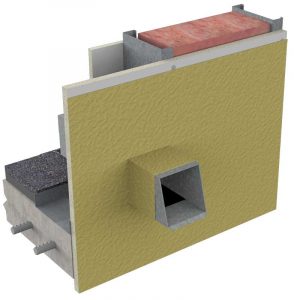
Specifiers can also take the lead by providing a specific maximum air leakage for the building and requiring whole-building air tightness testing. Taking building air leakage from the International Energy Conservation Code’s (IECC’s) maximum rate of 0.18 L/s•m2 (0.40 cfm/sf) to a readily attainable2 0.11 L/s•m2 (0.25 cfm/ft2) or lower does not require more materials or energy use. It simply takes attention to detail from the project team—for example, air barriers being continuous, as in, they should not have holes in them. The State of Washington has also demonstrated leadership in this direction by incorporating the lower maximum air leakage rate into their state building code, and by requiring whole building air tightness testing.
Material specification can be simplified
Architects, specifiers, and general contractors share a common objective: design and construction of a (minimally) code-compliant building. Inspectors and the Authority Having Jurisdiction (AHJ) ensure design intent is met.
Many building product manufacturers provide a fairly straightforward tool to assist with this process. AWRB systems that are supported with an ICC Evaluation Service (ICC-ESR) evaluation report or equivalent document have
met a comprehensive set of material test requirements. Testing is done by certified third-party laboratories. The results are reviewed independently as part of the approval process. Evaluation reports of this kind can provide third-party confirmation of compliance with model building codes both as WRBs and as air barrier systems.
By specifying AWRB systems supported by an ICC-ESR evaluation report or equivalent document, making them fully qualified, specifiers allow competitive bidding by manufacturers of AWRB systems. It is a simple tool to specify high-quality materials without unduly restricting competition.
Testing and inspection
Whole-building air leakage testing, commonly known as blower door testing, is a method used to measure the air tightness of a building envelope. It involves the use of a specialized fan and pressure-measuring equipment to quantify the amount of air leakage in a building. The blower door apparatus consists of a calibrated fan that is temporarily installed in a doorway or an exterior opening. The fan either pressurizes or depressurizes the building, and pressure measurements are taken to assess the air tightness. Various standards and guidelines are available to perform whole-building air leakage testing, including ASTM E779, ASTM E1827, and RESNET/ANSI Standard 380. These documents provide standardized procedures for testing and reporting air leakage measurements.