High-rise building codes for insulated penetrations
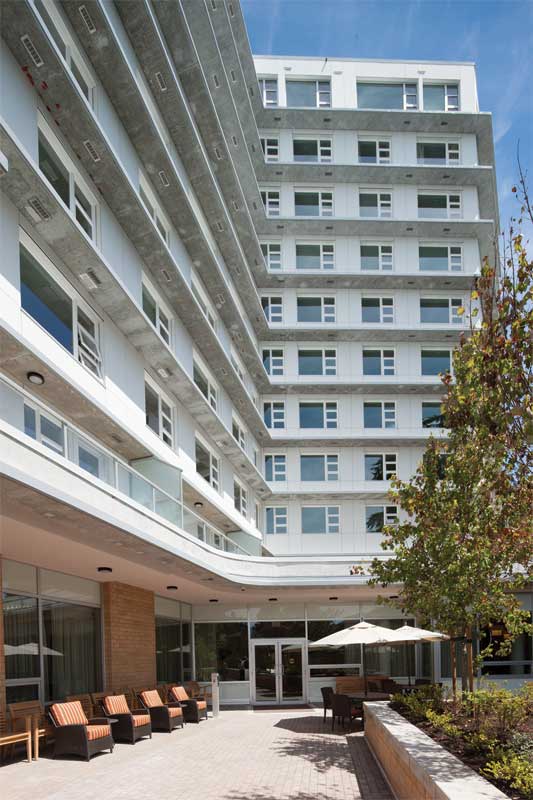
Photo courtesy PARC Retirement Living
Three paths to compliance
The 2016 iteration of ASHRAE 90.1 offers three paths to compliance. The prescriptive method specifies details of building elements such as:
- continuous insulation (ci);
- specific R-values for components depending on construction type and geographic region; and
- glass-to-opaque-wall ratios limited to 40 percent of wall surface.
The energy cost budget (ECB) method is an alternative performance-based system for determining compliance, and available as a free web program. (For more information, click here.) ECB compares two models of a building: the proposed building as designed and the budget building design (a structure of the same size and constructed to minimum ASHRAE 90.1 prescriptive requirements), calculating costs and identifying areas needing change. The program simulates the building’s proposed energy costs, comparing them with those of the code-compliant structure, and indicating whether the proposed costs are less than or equal to the baseline and, thus, compliant. ECB can also summarize a building’s energy performance as a percentage of ASHRAE 90.1 standards.
In the performance rating method (PRM), the project team applies software modeling tools to prove the building will perform at least as well as under the prescriptive requirements with an equal or lower annual energy cost. PRM is also used for “beyond code” programs such as LEED or the International Green Construction Code (IgCC).
Canada has introduced similar “objective-based” codes, providing a consistent means of evaluating and accepting alternative solutions to code requirements. Each technical requirement now includes objective, functional intent statements accommodating innovative approaches.
The performance-oriented ECB and PRM paths allow energy tradeoffs comparable to carbon credits (e.g. more roof insulation or solar panels to offset energy loss from weakly performing glazing or other thermal bridges). These flexible paths are preferable for designs with less-efficient features such as floor-to-ceiling windows, or to allow new best practices not previously covered in prescriptive codes. STBs can enhance an envelope’s ability to meet performance criteria.
The implementation of ASHRAE 90.1 or IECC standards is not straightforward. As energy standards evolve, architects, developers, and even code officials may be unclear about whether local codes require STBs. For a project on the ECB or PRM performance path to compliance, accurate energy modeling can be an art form. Today’s 3D modeling software is very precise mathematically but the practitioner needs to put the correct and realistic information into the model to derive accurate output. For example, it is essential to include balcony slabs among inputs rather than treating it as part of the continuous exterior surface of the building. If one ignores thermal bridges, even though they appear small, they will compound and have a significant effect. Precise input is, therefore, critical to accuracy of the model.
Vancouver in the vanguard
Canadian codes have imposed higher standards than those in most U.S. jurisdictions. The 2017 NECB requires all new buildings to be “net zero-energy ready” by 2030. Vancouver, B.C., takes performance, particularly seriously. The city has an interesting market. There is not a lot of free space for new construction, and property is expensive. Most of the projects are infills, redevelopments, and construction of condos on parking lots. These types of projects need rezoning, and application approval requires very efficient construction such as Passive House certification or meeting a new metric called thermal energy demand intensity (TEDI). Measured in kWh/m2 annually, TEDI is the amount of heat required to keep a building warm after offsets from building envelope losses and heating of ventilation air regardless of how efficiently the heat source is produced. This metric directly reflects the building enclosure performance.
Vancouver building officials, aware of the performance challenges facing their densely-built environment, have instituted a green buildings policy—starting with rezoning of high-rises—requiring all rezoning applications after May 1, 2017, to meet standards for “near zero-emissions buildings” (equivalent to Passive House or the International Living Future Institute’s [ILFI’s] Zero Energy Building [EZB] certification) or “low-emissions, green buildings,” which address building envelope performance. (For more information, click here.)
A building ahead of its time in addressing building envelope performance is Cedar Springs Retirement Residence, a 146-unit, 11-story building in North Vancouver owned by Pacific Arbour Retirement Communities. Completed in 2012, architects Besharat Friars and structural engineers Glotman Simpson achieved LEED Gold certification by paying close attention to design and materials throughout the building. At cantilevered concrete “eyebrows” shading the building’s south and west façades on each floor, STBs help control energy loss, earning the building LEED credits for Innovation in Design and Thermal Comfort.
Additionally, STBs helped the Smithsonian’s National Museum of African American History and Culture in Washington, D.C., conserve energy and reduce humidity to protect artifacts from the effects of condensation.
The museum’s façade was designed to provide ci, but thermal bridging was a significant concern where the rooftop cooling towers are connected. Steel posts supporting the cooling towers penetrate the roof. Since an exhibit space lies directly below the cooling towers, thermal bridging had to be eliminated to prevent condensation from forming on the warm interior side of the building envelope, thereby preventing the prospect of mold growth and moisture damage that could threaten the museum’s collection.
STBs for steel construction were installed at 16 connection points per cooling tower to simultaneously insulate and support the columns penetrating the rooftop. The energy savings from the thermal breaks reduce heat loss at each point of penetration by up to 50 percent, contributing to sustainable design and LEED certification.
Thermal modeling may influence codes
B.C. Hydro has published the Building Envelope Thermal Bridging Guide containing 3D models of common envelope details and heat-transfer patterns. The guide refines industry-wide benchmarks for whole-building thermal performance, and may possibly influence future code development. The authors
are optimistic if the work from these guides can be incorporated into the ASHRAE standards, then ci could really gain leverage because building professionals across the board recognize ASHRAE and this standard.
The latest version of ASHRAE 90.1 requires specific modeling of “uninsulated assemblies” (e.g. projecting balconies, slab edges, and roof parapets where ci is not covered) in the envelope trade-off option (Appendix C1.2.6) and the ECB method of compliance (Appendix G Table G3.1 row 5.a.1). The next IECC iteration slated for publication later this year is expected to follow many of the changes from the 2016 version of ASHRAE 90.1. The next version of 90.1, to be released in 2019, is expected to provide more explicit requirements to address structural elements causing thermal bridging.
The future should see more STB use, driven by evolving codes and increased awareness and desire for energy savings, moisture avoidance, and thermal comfort. Agencies setting codes, and architects, engineers, and constructors are increasingly recognizing how leaving penetrations in a building envelope uninsulated “is like wearing a down jacket but leaving it unzipped,” as once described by Hao Ko, managing director of Gensler.
Jonathan Carreiro, P. Eng., is product manager for Schöck North America. He has been in this position since 2015 after moving from the builder side of the industry. Carreiro has a bachelor’s degree in civil engineering from Royal Military College of Canada and an MBA from Carleton University. He is a member of the American Society of Heating, Refrigerating and Air-conditioning Engineers (ASHRAE). Carreiro can be reached at jonathan.carreiro@schoeck.com.
Patrick M.B. Chan is regional engineering and sales manager with Schöck North America. He manages the Pacific Northwest, Alberta, and the Prairies territories. Chan holds a civil engineering degree from the University of British Columbia. Based in Vancouver, B.C., he focuses on simple solutions to reduce the environmental footprint of structures by addressing building envelopes. Chan can be reached at patrick.chan@schock-na.com.