Key considerations for designing fenestration systems for success
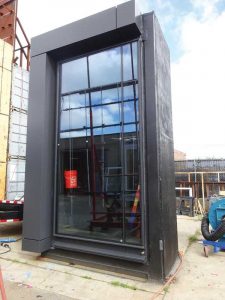
Performance mockup (PMU)
The first test to be specified is a PMU test (Figure 4). This test involves constructing a mockup assembly using all components that will be installed on the building, including the fenestration system and perimeter components, and installing them according to the drawings exactly as they will be installed onsite. This is the first test of the fenestration system and its surrounding components to ensure they will work together to provide the specified performance when installed correctly.
The PMU is also an opportunity to coordinate transitions between different systems on the project and may double as a visual mockup (VMU) for the design team as well. However, the PMU is another commonly value-engineered item as it is a significant task and can lead to additional costs to coordinate the construction and necessary testing.
A PMU is especially important if a custom system is being used for the project. However, if the budget is tight or the project is relatively small, a PMU may not make sense for an off-the-shelf system with proven performance. The project schedule should also be considered when discussing a PMU. Depending on the system to be used for the project, such as a custom system, it may not be manufactured in time for a PMU.
Testing requirements
There are usually two separate paragraphs in a typical specification section describing fenestration performance. The first is lab testing, which was described earlier regarding the various AAMA ratings, and the second is in-situ testing/performance. Often, a fenestration product will easily pass a lab test, but experience failures in the field test once it is installed on the building. This can be due to installation/perimeter conditions, potential damage during installation, or even an issue during manufacturing which occurred once window production started.
Testing standard AAMA 502, Voluntary Specification for Field Testing of Newly Installed Fenestration Products allows field water tests to be conducted at two-thirds of the laboratory test pressure and states the field reduction is used to account for environmental conditions and installation. Manufacturers typically argue for field testing to include this one-third performance reduction; however, neither manufacturers nor AAMA has provided quantitative reasoning or a calculation to confirm why the performance should be reduced by one-third. Many professionals maintain the stance that a window assembly should not be damaged during installation or affected in a manner that would compromise its performance.
AAMA 502 states, unless otherwise specified and clearly stated in the project specifications, in no case shall the specified static water test pressure exceed two-thirds of the tested or rated-laboratory performance. Therefore, the specifications are the only document that can override the AAMA 502 requirement by stating no decrease in the specified test pressures will be permitted in the evaluation of field testing. Unfortunately, having this language in the specifications may not be enough to avoid arguments with manufacturers or installers during testing, both might take the stance of the one-third reduction being an “industry standard” and not up for debate.