Kinetic façade systems: Adding a dynamic element to building structures
Budget considerations
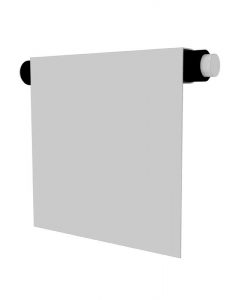
A project’s design and specification phase is the best opportunity to critically analyze the aesthetic and performance requirements, and to make adjustments to ensure its success. Once the project moves into fabrication and installation, corrections become more costly.
Budgeting for a kinetic façade system usually entails striking a balance between the desired aesthetic and performance goals of the product. Since kinetic façade systems are delivered to a jobsite in pre-assembled units, most installations range from $9 to $15 per 1 m2 (11 sf), depending on several factors. Note this does not include material cost.
Additional costs also may be incurred as a result of testing requirements of the location or the application. Local labor costs, union requirements, site access, street closures, timing and scheduling, and project duration, are just some of the installation-related factors that can affect the final cost of kinetic façade systems.
In addition to the costs associated with installation, system type, and testing, other relatively small hardware or structural changes can have a profound impact on the final cost. These include the following.
Flapper density
Flapper density is defined as the number of flappers per 1 m2. The smaller the flappers, the more individual handling, assembly, labor, and mounting parts are required. For example, it would take about four 130 x 130 mm (5 x 5 in.) flappers to fill a 1-m2 area, assuming a 25-mm (1-in.) space between flappers, while it would take nine 76 x 76 mm (3 x 3 in.) flappers to fill the same area. This increased number of flappers translates to more than double the amount of assembly time, labor, mounting hardware, etc.
Flapper finishing
Flapper elements produced from pre-finished sheet material, such as anodized or painted aluminum, typically are more cost-effective than post-finished flappers. The type of finish also influences the overall cost of the kinetic façade. For example, standard anodize and painted colors will be more economically priced than exotic colors and multistep coatings. The cost and benefits of each type
of finish should be analyzed to ensure the flapper finish does not adversely affect the project budget.
Finish on back of flappers
Finishing the back-side of flappers can incur additional costs because it requires the use of extra material and resources. Anodized flappers will have both front and back faces coated with the same process. Painted flappers, on the other hand, can accommodate different coatings on the front and back face. While both sides can be coated with the same finish, opting for a wash coating on the rear face may reduce overall cost. This painting method is acceptable on the back side of the flapper when it is either invisible or barely visible, which will be the majority of applications.
Supporting structure finish
In addition to the finish on flapper elements, the finish applied to the supporting structure, (i.e. the horizontal and vertical mounting rails), also influences the cost of the total façade system. A darker, low-sheen finish is applied to the supporting elements to accentuate the aesthetic quality of the flapper elements. These framing members are usually painted.
Building spans and loads
The required span and environmental loads can affect the weight and size of the kinetic façade’s structural elements. This can, in turn, impact the cost of the system.
Mounting hardware
The mounting hardware and anchoring systems of the flapper elements depend heavily on the required span, deflections, and building substrate materials. This hardware can consist of embeds integrated into the building structure or post-applied anchors supplied by the façade system manufacturer.