Make smart concrete: A study on self-sealing
Crystalline admixtures
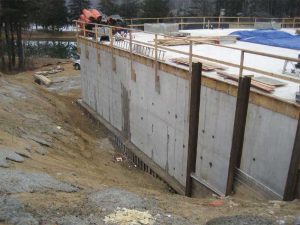
Images courtesy Kryton International
Some type of waterproofing protection is essential to secure the durability and resulting sustainability of concrete structures. Protective systems can be classified based on their application method: surface-applied systems consist of coatings and sheet membranes (described in ACI Report 515.2R-13, Guide to Selecting Protective Treatments for Concrete), while integral systems consist of an admixture that is added to concrete and protects it from within (described in ACI Report 212.3R-16, Report on Chemical Admixtures for Concrete). Some problems exist with sheet membranes. The installation of membranes calls for careful finishing, temperature control, clean and dry concrete, and dependable surface adhesion. Even the simplest membrane system requires a level of skilled application and the most dedicated tradesperson can make mistakes while applying it, often while battling poor weather conditions. Membrane sheets have to be individually applied, and even the smallest gap between them makes concrete highly susceptible to the influx of water. Moreover, membranes have been known to peel, tear, rip, debond, or puncture, especially during backfilling. Membranes are also usually inaccessible for repairs after installation, increasing the cost of maintenance.
Integral crystalline waterproofing (ICW) technology addresses this issue in a more permanent way. Crystalline waterproofing admixtures are usually a dry-powder mix of Portland cement, fine silica sand, and a proprietary blend of other chemicals. The admixture (typically up to two percent of cementitious content by weight) is used during the mixing stage of concrete.
The principles of ICW technology are similar to the process that occurs during concrete hydration. When cement particles are mixed with water, a chemical reaction occurs. As a result of this chemical reaction, two main types of crystals (calcium silicate hydrate [CSH] and calcium hydroxide [CH]) are generated.
Conventional concrete
The hydration reaction that takes place when cement is mixed with water is responsible for concrete’s setting, hardening, and strength development.
However, when crystalline technology is used, the passive admixture in the matrix gets activated as soon as it comes in contact with moisture. On activation, this particular admixture starts crystallization and develops a microstructure of needle-like crystals in concrete.
Concrete modified using crystalline technology
The needle-shaped crystals grow to fill and block the microscopic capillary pores and micro-cracks. As long as moisture is present, crystals continue to grow throughout the concrete, filling up voids, cracks, and capillary pores. Once the concrete has dried, the crystalline chemicals sit dormant until another dose of water (such as a through a new crack) causes the chemical reaction (i.e. crystallization) to restart.
The ability to reactivate in the presence of water gives concrete treated with this admixture the ability to self-seal. When cracks form due to drying shrinkage, setting, seismic activity, or similar, water entering through them causes new crystals to form and grow, blocking the cracks. In the case of this specific admixture, crystals can seal cracks up to 0.5 mm (0.02 in.) in width. Enabling the self-sealing ability of concrete is one of crystalline technology’s most useful features because it helps maintain durability in service and reduce the long-term maintenance costs of a concrete structure. Unlike sheet membranes that could separate from the structure over time—thereby removing all waterproofing—the crystalline admixture stays integral to the slab, protecting concrete from water penetration.
A case study in self-sealing
The Newburyport Wastewater Treatment Facility (NWTF) in Massachusetts is a sludge treatment facility providing biological treatment of wastewater prior to discharge into the Merrimack River.
It can handle up to 12.9 million L (3.4 million gal) per day of wastewater. Originally constructed in 1984, improvements to the plant were recommended in 2012 to modernize and improve its ability to handle current and future water flows. The construction of a new operations, control, and laboratory building on a lot adjacent to the existing facility was part of the renovation. The architects were looking for a permanent waterproofing solution that would continue to self-seal over time.