Properly soldering no-lead copper alloys
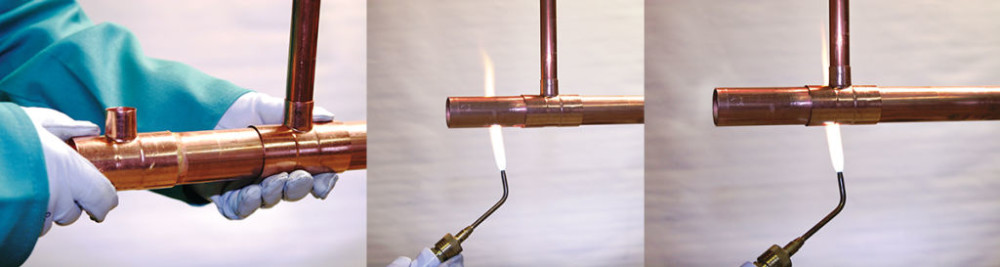
Lead-free copper-base alloys evolve
For more than two decades, the U.S. plumbing market has continuously moved to reduce the levels of lead in manufactured plumbing components, including those made of copper alloys like brass and bronze. Brasses and bronzes have long been used due to their relatively low melting point, high strength, exceptional castability and machinability, and good corrosion resistance.
Historically, leaded copper casting alloys like unified numbering system (UNS) alloys C83600 (i.e. red brass) and C84400 (i.e. semi-red brass), were used specifically for their beneficial casting and machining properties that facilitated the manufacture of complex parts like valve bodies and plumbing fittings. For highly machined parts like valve stems and parts, the wrought alloy C36000 (i.e. free-cutting brass), which sets the standard for machinability of all metal alloys, was a mainstay.
As the Safe Drinking Water Act (SWDA) took effect, manufacturers began to introduce alloys that primarily used a combination of bismuth and selenium to replace lead. While these alloys retained the beneficial properties of brass and bronzes for cast plumbing components, selenium was expensive so they came with a cost disadvantage. Alloy developers, foundries, and plumbing manufacturers continued to work to develop new alloys that did not rely on the use of selenium; thus developing new copper-bismuth and copper-silicon alloys for use in manufacturing lead-free plumbing components.
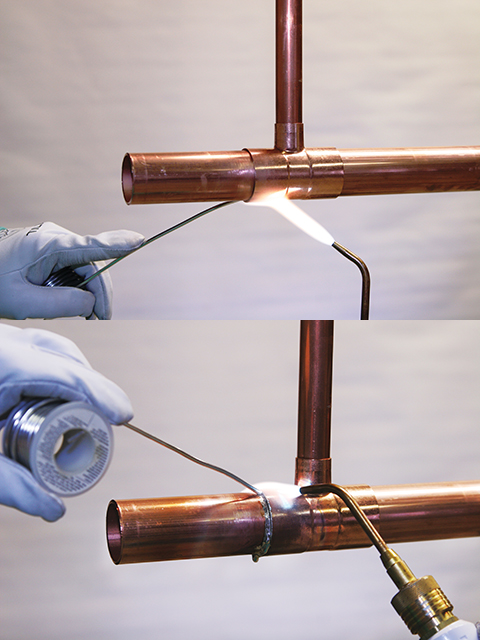
Some of the popular copper-bismuth (bismuth brass) alloys are C89844, C89833, and C89836 for casting, along with C49300 for wrought products. In these alloys, bismuth acts much like lead did. As a low melt point alloy with relatively low solubility during casting of plumbing components, it solidifies in the alloy-filling casting porosity voids and acts as a chip-breaker making downstream machining processes such as threading easier. However, since bismuth is not soluble in the alloy matrix, it gives no additional strength to the alloy. Additionally, there are concerns that any bismuth-containing alloys require special segregation when plumbing components are removed after use and recycled.
Copper-silicon (e.g. silicon brass, silicon bronze) alloys have started to become more popular in manufacturing plumbing components. This includes the casting alloys C87850 and C87600, as well as the wrought alloy C69300 (which has essentially the same chemical composition as the C87850 casting alloy). Unlike bismuth in the copper-bismuth alloys, silicon is highly soluble in the alloy matrix, so it does not fill porosity voids during product casting, but it does add mechanical strength. When combined with phosphorous in the alloy, it also improves machining properties. From a resource standpoint, silicon is more abundant than bismuth, but like bismuth, silicon-containing copper alloys may also require special segregation during recycling. Further, silicon decreases the thermal conductivity of the alloy and may create a surface layer that decreases solderability. As a result, solder joint plumbing products made of these alloys do require special care during installation.
More recently, existing low-lead alloys like C27450 and others are being used to replace C36000 in machined parts, and new casting alloys that do not use lead, bismuth, or silicon like C83470 are arriving on the scene. Plumbing manufacturers and alloy developers continue to use or create other low-lead and lead-free copper alloys to create long-lasting, reliable plumbing valves, fittings, and components that can be recycled over and over again.
Conclusion
The copper industry and plumbing component manufacturers have come a long way in a short amount of time to put new no-lead brass and bronze valves, fittings, and components into the market that meet the Federal Reduction of Lead in Drinking Water Act and retain the long-lasting, reliable performance the industry has come to expect. Following the steps outlined in this article for installing these components through proper soldering helps ensure these products perform leak-free from installation and throughout the plumbing’s lifecycle.
Andy Kireta Jr., vice president of the Copper Development Association (CDA), is responsible for the use of copper and copper alloy systems and products in building construction applications, including plumbing, mechanical, and architectural systems. Kireta has been active in the development, specification, application, code, and standards acceptance and market promotion and education of the use of copper in building construction for CDA since 1992. He can be contacted by e-mail at andrew.kiretajr@copperalliance.us.