Rainscreen systems meet the need of modern buildings
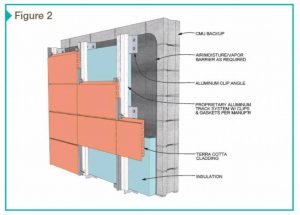
The rainscreen system in Figure 2 shows much of the same function, and offers:
- lightweight cladding with optimal movement capabilities;
- thinner overall wall section;
- low maintenance since joints do not need to be repointed with mortar or re-caulked with sealant;
- all-season installation since water is not involved in the construction process;
- eliminates shelf angles;
- need not be installed from bottom up; and
- allows abundant airflow in the wall cavity.
Depending on the cladding material and system selected, moisture through cladding joints can be moderated by the design and profile of the openings or gasketed connections. Moisture, air/vapor, and thermal loads are then addressed predominantly by the control layers on the backup wall.
A conceptual advantage to open-joint systems, or cavity walls with a significant amount of weep vents, is a possible reduction of negative pressures across the veneer pulling air and moisture into the wall cavity. This ‘pressure-equalization’ effect is the subject of considerable debate and is dependent on many variables, such as geography, exposure, air space volume, calculated number of intentional openings in the veneer, airtightness of the backup wall, and proper execution of wall air space compartments. It takes a high level of detailing, installation, and testing as well as funds to achieve true pressure equalization across a veneer. In fact, with larger air volumes in modern cavity wall design, it is rare. However, the good news is a well-drained and back-ventilated rainscreen wall system is often a default outcome. To deter horizontal airflow and increase vertical airflow in the wall cavity, some designs call for isolation of cavity space by volume. The most effective method to achieve this is by using vertical stainless steel closure strips fastened to the backup wall and extending into a vertical veneer movement joint. Depending on project goals, this can occur at outside corners only and/or approximately 7 m (24-ft) on center (o.c.). Other compartmentalization details such as doubling up insulation or using vertical foam rods to seal air space compartments are generally ineffective in the field because of acceptable air space variance, concerns associated with tight installations of closure pieces pushing on bricks laid in wet mortar, and material movement during the building service life.
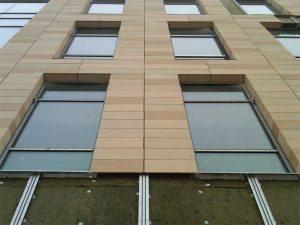
System thinking for materials and delivery, design, and construction
“No single component or material has the capability to provide a complete air barrier system for a building” – Air Barrier Association of America (ABAA).
Since air and vapor tend to move from high pressure to low, high humidity to low, and high temperature to low, the entire enclosure needs to work as a system rather than a collection of materials. A change in one component will have a ripple effect throughout the system and must be examined for unintended consequences.
Coordination between materials and the trades installing them is critical. Problems in the building enclosure tend to occur at the interface between dissimilar materials or functions. Responsibility for performance at the interface conditions is difficult to assess. A single trade performing most of the enclosure can help with construction sequencing, installation, and performance.
Materials
The performance of the enclosure is dependent on skilled craftworkers providing the installation (IMI and International Masonry Training and Education Foundation [IMTEF] work through a network of more than 60 training centers in the United States. Certification programs, craftworker upgrades, and a variety of educational opportunities train tradespersons in current building science and materials, including the ABAA certification and the IMI Rainscreen Certificate program).
The cladding attachment system must carry the dead load of the rainscreen veneer, provide lateral resistance and load transfer, and hold the individual units in place, while allowing for enough flexibility in the system for small amounts of installation tolerances for good aesthetics. One of the key aspects of rainscreen cladding sub-frame installation is coordination between the water/air control layers and how the cladding attachment penetrations are installed to maintain continuity. This topic deserves a pre-installation meeting in the jobsite trailer and testing on the mockup and in the field for verification. These systems may look familiar to designers and builders with some experience in stone cladding. The principles are similar, and so is the installation. A cladding manufacturer may have proprietary details for the track and channel system. They may provide the hardware with the cladding and include engineering services and shop drawings.
Other vendors may provide the cladding material only. In this case, the installation contractor can choose to work with outside vendors to provide a solution.
Another solution is for the installer to work with an engineer to design the support and attachment system and have it manufactured.